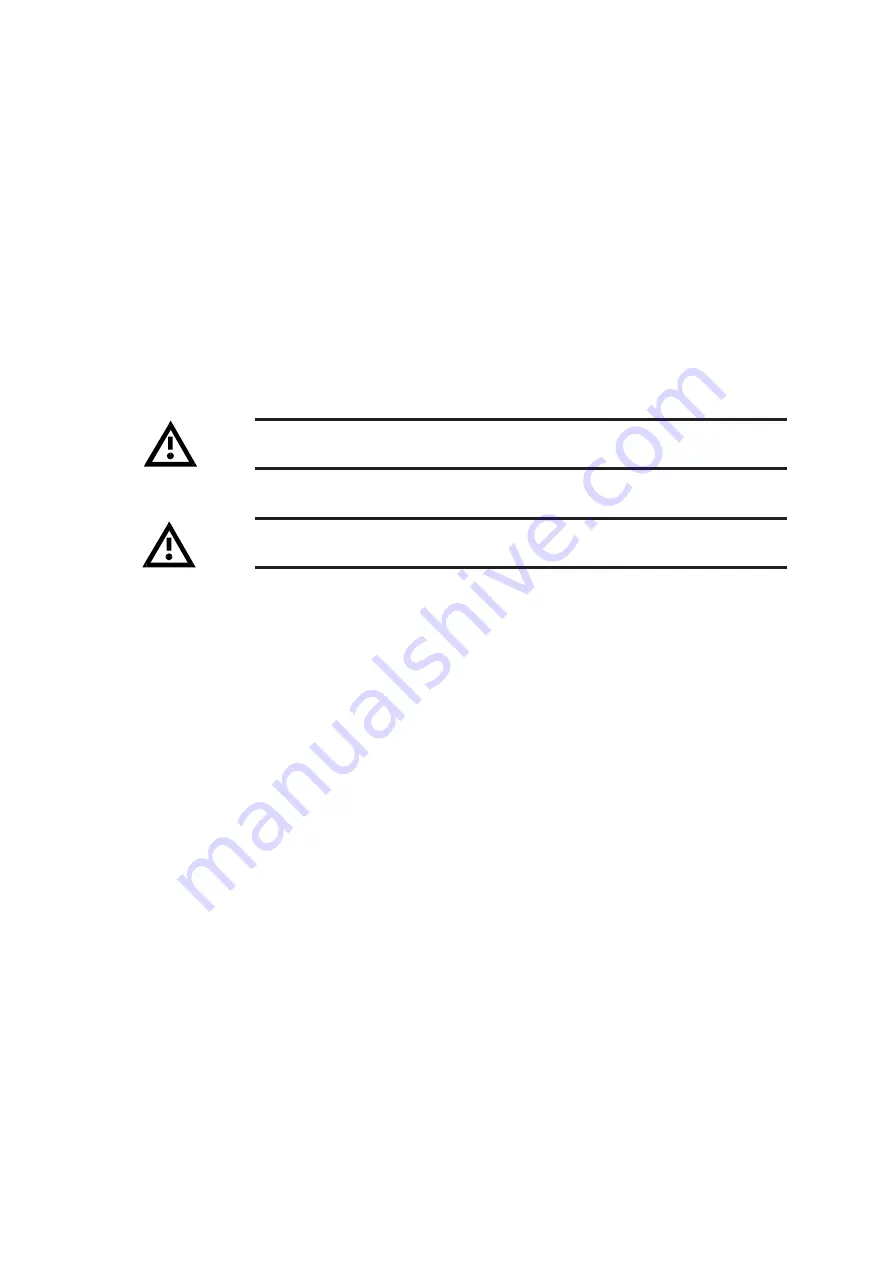
26
5. START-UP
5. START-UP
5. START-UP
5. START-UP
5. START-UP
5.1 PRELIMINARY CHECKS
5.1 PRELIMINARY CHECKS
5.1 PRELIMINARY CHECKS
5.1 PRELIMINARY CHECKS
5.1 PRELIMINARY CHECKS
- Check the electrical connections are correct and ensure that all terminal clamps are fully tightened down.
- Check that the voltage on the RST terminals is 400 V ± 5% (or otherwise that indicated on the unit dataplate).
If the voltage is highly variable, contact our technical department for the recommended protection devices.
- Check that the display shows the refrigerant gas pressure of the refrigerant circuits.
- Check for refrigerant leaks with a leak detector.
- Check the power supply rating on the casing heating elements.
To check that the heating elements are operating correctly, check that the lower section of the compressor is
warm and around 10 - 15 °C above ambient temperature.
- Check that the hydraulic connections are in compliance with the indications on the unit dataplates.
- Check that the water circuit has been properly bled: charge gradually while keeping the upper bleed valves
open - these will have been installed by the fitter together with a suitably sized expansion tank (see section 4.2
for details).
The heating elements must be switched on at least 12 hours before start
The heating elements must be switched on at least 12 hours before start
The heating elements must be switched on at least 12 hours before start
The heating elements must be switched on at least 12 hours before start
The heating elements must be switched on at least 12 hours before start
up; this happens automatically when the main power switch is closed.
up; this happens automatically when the main power switch is closed.
up; this happens automatically when the main power switch is closed.
up; this happens automatically when the main power switch is closed.
up; this happens automatically when the main power switch is closed.
Large refrigerant gas leakage change the composition of the remaining
Large refrigerant gas leakage change the composition of the remaining
Large refrigerant gas leakage change the composition of the remaining
Large refrigerant gas leakage change the composition of the remaining
Large refrigerant gas leakage change the composition of the remaining
refrigerant gas mixture and reduce the performance of the unit.
refrigerant gas mixture and reduce the performance of the unit.
refrigerant gas mixture and reduce the performance of the unit.
refrigerant gas mixture and reduce the performance of the unit.
refrigerant gas mixture and reduce the performance of the unit.
5.2
5.2
5.2
5.2
5.2 WORKING DESCRIPTION
WORKING DESCRIPTION
WORKING DESCRIPTION
WORKING DESCRIPTION
WORKING DESCRIPTION
5.2.1 General
5.2.1 General
5.2.1 General
5.2.1 General
5.2.1 General
The regulator is designed to maintain water temperature in the unit in which it is installed at the set value; this is
achieved through the control of compressor operation.
The controller has 2-step capacity control over each compressor.
Besides the compressors, the controller also actuates other components of the cooling system, such as pumps (ST
version) and fans, the operation of which is determined by time settings and alarms, as well as “accessory”
functions, such as condensation and evaporation, which are described below.
Almost all operating parameters (set points, differentials, calibration, delays, etc.) described below can be configured
from the program pages.
For specific information see the instruction manuala of pCO
2
controller.
5.2.2 Unit in stand-by mode
5.2.2 Unit in stand-by mode
5.2.2 Unit in stand-by mode
5.2.2 Unit in stand-by mode
5.2.2 Unit in stand-by mode
The unit is in stand-by mode when it is correctly powered but not enabled for operation.
When in this condition, the unit may be put into service in various ways: by pressing the “on-off” key, by means
Summary of Contents for KAPPA V 2001
Page 69: ......