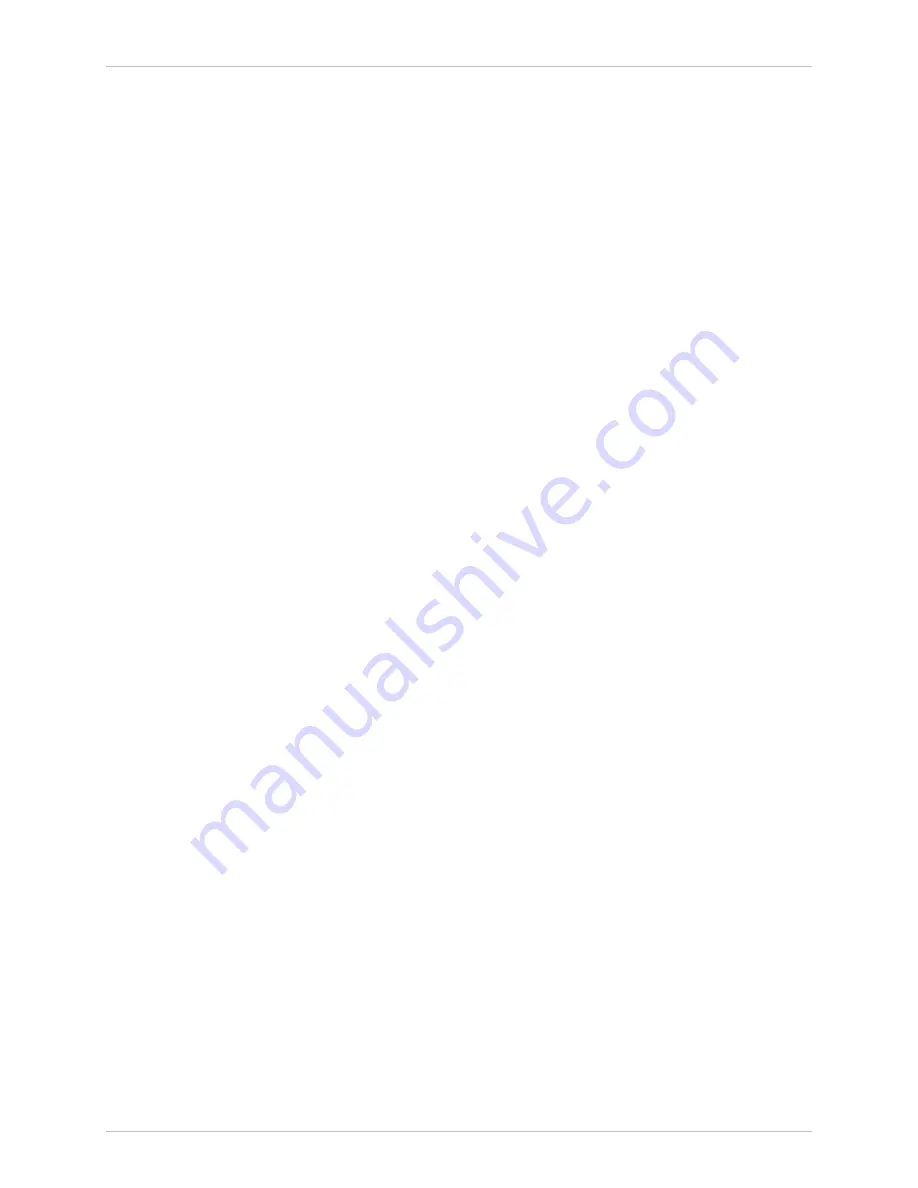
Chapter 1 Introduction
MT1000A
Installation and Operation Manual
1-6 Functional
Description
Front panel indicators display each alarm condition. In addition, a dedicated
connector is used to provide major and minor alarm indications, by means of dry
contacts.
The major alarm is activated in the following cases:
•
MT1000A is not powered, or total power supply failure (e.g., when two power
supplies are installed, failure of both supplies).
•
Loss of fiber optic input signals, or loss of fiber optic frame synchronization.
•
Loss of tributary input signals, or loss of frame synchronization
•
Unable to activate redundancy.
The minor alarm is activated in the following cases:
•
Reception of AIS signal on the fiber optic input.
•
Reception of AIS signal on tributary inputs.
Management and Monitoring
MT1000A units are equipped with a front panel serial RS-232 management port
and an Ethernet management port. The RS-232 port operates at user-selectable
rates of 9.6, 19.2, 38.4, 57.6 and 115.2 kbps over a null-modem cable. The
Ethernet port operates at a rate of 10 Mbps and can be set to full- or half-duplex.
The management interface supports the following management methods:
•
Supervision Terminal
–An ASCII terminal connected to the RS-232 port (or a
PC running a terminal emulation program) can be used as a supervision
terminal. All software required for the various management functions available
through the terminal is contained in the MT1000A.
•
SNMP Management
–The management interface includes an SNMP agent that
enables SNMP management of the MT1000A, using the UDP-over-SLIP (Serial
Link Internet Protocol) protocol. The SNMP agent also enables management
by other SNMP-based systems.
•
Ethernet Management
–A management terminal can be connected to the
MT1000A via an Ethernet connection, using a UTP-CAT5 cable. The 10BaseT
Ethernet interface supports a throughput of 10 Mbps. All software required for
the various management functions available through the terminal is contained
in the MT1000A.
Power Requirements
MT1000A can be ordered with one or two power supplies. Two types of power
supplies are available:
•
AC/DC wide-range for operation on AC (100 to 240 VAC) or on
DC (40-72 VDC) sources
•
DC operation on 24 VDC source.
Each power supply (A and B) can be ordered as one of the above power supply
types).
Summary of Contents for MT1000A-13-R3
Page 2: ......
Page 16: ...Chapter 1 Introduction MT1000A Installation and Operation Manual 1 10 Technical Specifications...
Page 28: ...Chapter 3 Operation MT1000A Installation and Operation Manual 3 4 Turning MT1000A Off...
Page 72: ...Appendix B MT1000A MIBs MT1000A Installation and Operation Manual B 2...