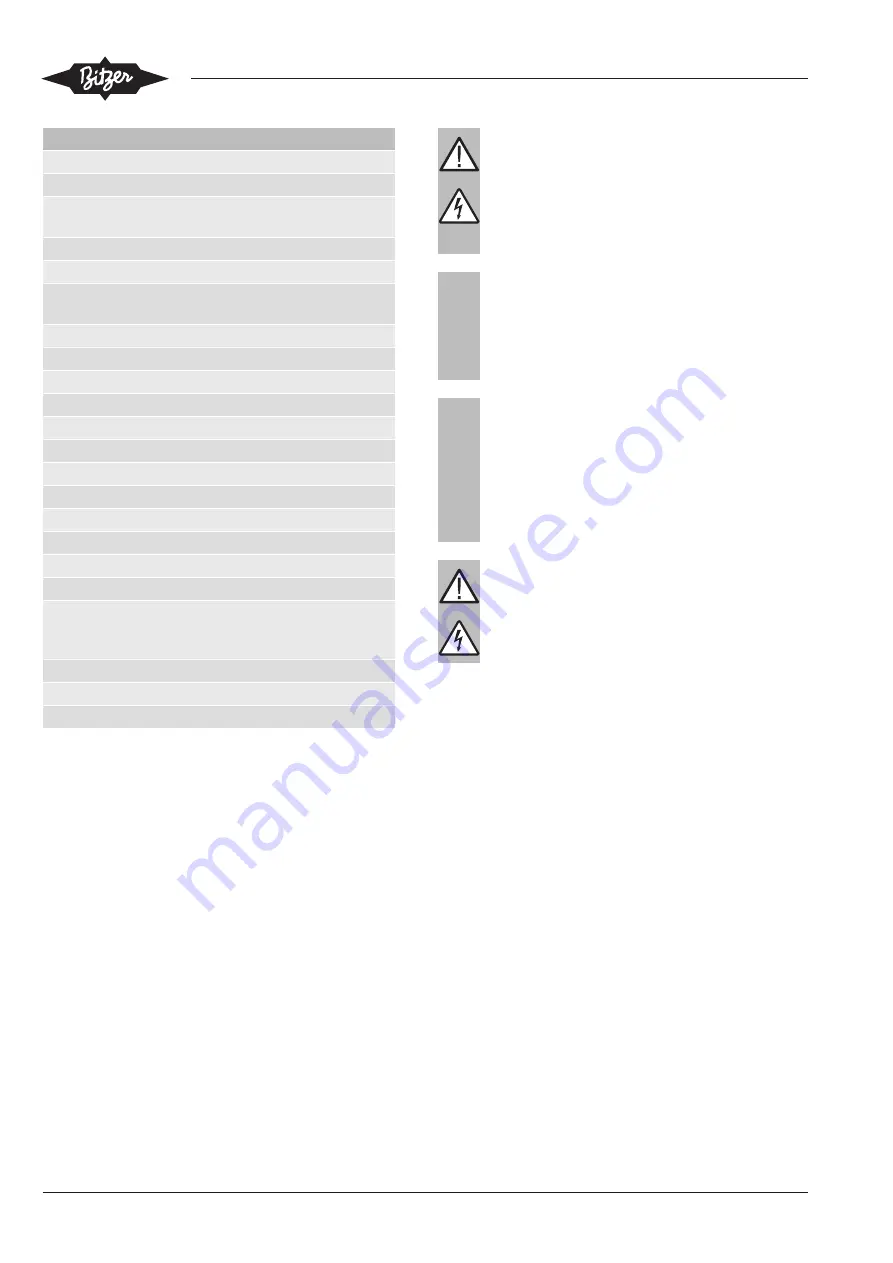
SB-110-4
44
Connection positions
7
Oil drain (motor housing)
7a
Oil drain (suction gas filter)
7b
Oil drain from shaft seal (maintenance con-
nection)
7c
Oil drain hose (shaft seal)
8
Threaded bore for foot fastening
9
Threaded bore for pipe fixture (ECO and LI
lines)
10
Maintenance connection for oil filter
11
Oil drain (oil filter)
13
Oil filter monitoring
14
Oil flow switch
15
Earth screw for housing
16
Pressure blow-off (oil filter chamber)
17
Maintenance connection for shaft seal
18
Liquid injection (LI)
19
Compressor module
20
Slider position indicator
21
Oil level switch
22
Oil pressure transmitter
23
Connection for oil and gas return (for sys-
tems with flooded evaporator adaptor op-
tional)
24
Access to oil circulation restrictor
SL
Suction gas line
DL
Discharge gas line
Tab. 6: Connection positions
Dimensions (if specified) may have tolerances accord-
ing to EN ISO13920-B.
The legend applies to all open drive and semi-hermetic
BITZER screw compressors and includes connection
positions that do not exist in every compressor series.
5
Electrical connection
According to the EU Machinery Directive 2006/42/EC
annex I, the compressors and their electrical accessor-
ies are subject to the protection objectives of the EU
Low Voltage Directive 2014/35/EU. For any work per-
formed on the electrical system: EN60204-1, the
IEC60364 series of safety standards and national
safety regulations must be observed.
WARNING
Risk of electric shock!
Before performing any work in the terminal box
of the compressor: Switch off the main switch
and secure it against being switched on again!
Close the terminal box of the compressor before
switching on again!
!
!
NOTICE
Risk of short-circuit due to condensation water
in the terminal box!
Use only standardised components for cable
bushing.
When mounting, pay attention to proper sealing.
!
!
NOTICE
Risk of motor damage!
Improper electrical connection or compressor
operation at incorrect voltage or frequency may
lead to motor overload.
Observe the specifications on the name plate.
Connect properly and check the connections for
tight fitting.
DANGER
Danger of electric shock due to spontaneous
electrostatic discharge at high voltage.
Carefully design protective earth conductor sys-
tem.
Heating the terminal box
For critical applications (low-temperature applications)
and, in particular, for environments with high air humid-
ity, the terminal box may require heating. A heater can
be retrofitted as an accessory.
Coating terminal plate and pins
During low-temperature applications with low suction
gas superheat, frost may form on the motor side and
partly also on the terminal box. To prevent voltage
flashovers due to moisture, we recommend coating the
terminal plate and terminal pins with contact grease
(e.g. Shell Vaseline 8401, contact grease 6432 or equi-
valent).
5.1
Dimensioning components
▶ Select motor contactors, cables and fuses according
to the maximum operating current of the compressor
and the maximum power consumption of the motor
in case of direct-on-line start. With other starting
methods according to the lower load.
▶ Use the motor contactors according to the opera-
tional category AC3.