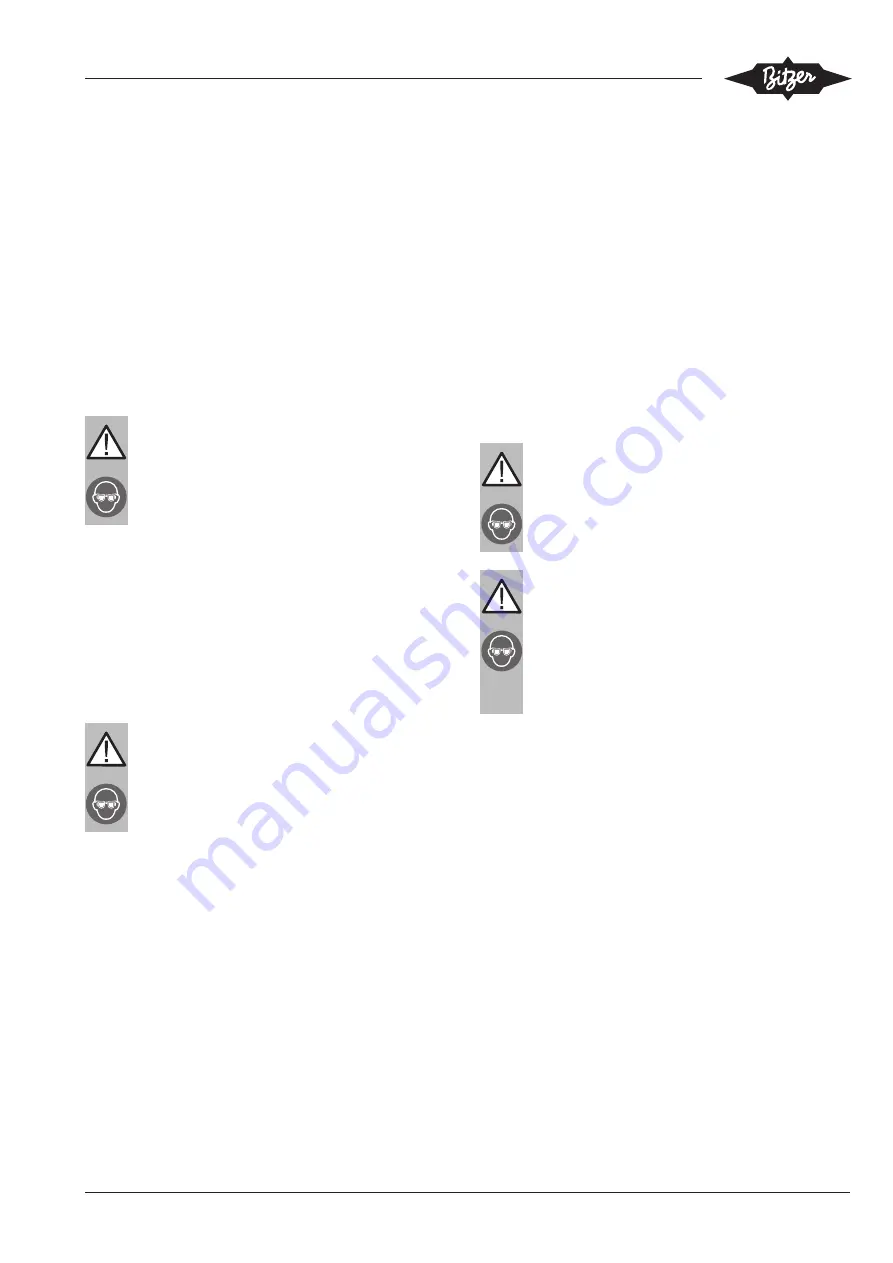
SB-110-4
53
8.3
Integrated pressure relief valve
The valve is maintenance-free.
However, after repeated venting, it may leak constantly
due to abnormal operating conditions. The con-
sequences are reduced performance and a higher dis-
charge gas temperature. Check the valve and replace it
if necessary.
8.4
Integrated check valve
If the check valve is defective or contaminated, the
compressor runs for some time in reverse direction
after it has been switched off. The valve must then be
changed.
WARNING
The compressor is under pressure!
Serious injuries are possible.
Depressurize the compressor!
Wear safety goggles!
8.5
Oil stop valve
In case of damage or contamination, the compressor
can be charged with oil during a prolonged shut-off
period.
HS.85: Valve installed on the compressor as part of the
oil management system.
HS.95: External solenoid valve.
WARNING
The compressor is under pressure!
Serious injuries are possible.
Depressurize the compressor!
Wear safety goggles!
8.6
Oil filter
HS.85: Oil filter integrated into the compressor and
mounted at the factory.
HS.95: Oil filter available as an optional accessory, in-
stalled externally (without integrated pressure drop
check).
HS.85: Replacing the internal oil filter (see figure
13, page 53)
Changing the oil filter for the first time is recommended
after 50 .. 100 operating hours. During operation, the oil
filter monitoring system constantly checks the pollution
degree. If the signal lamp of the oil filter monitoring
lights up (F10, see figure 10, page 46), check the oil fil-
ter for contamination and replace it if necessary.
WARNING
The compressor is under pressure!
Serious injuries are possible.
Depressurize the compressor!
Wear safety goggles!
WARNING
The oil filter chamber and the compressor are
pressure chambers independent of each other!
Serious injuries are possible.
For maintenance work, relieve separately the
compressor and the oil filter chamber of pres-
sure!
Wear safety goggles!