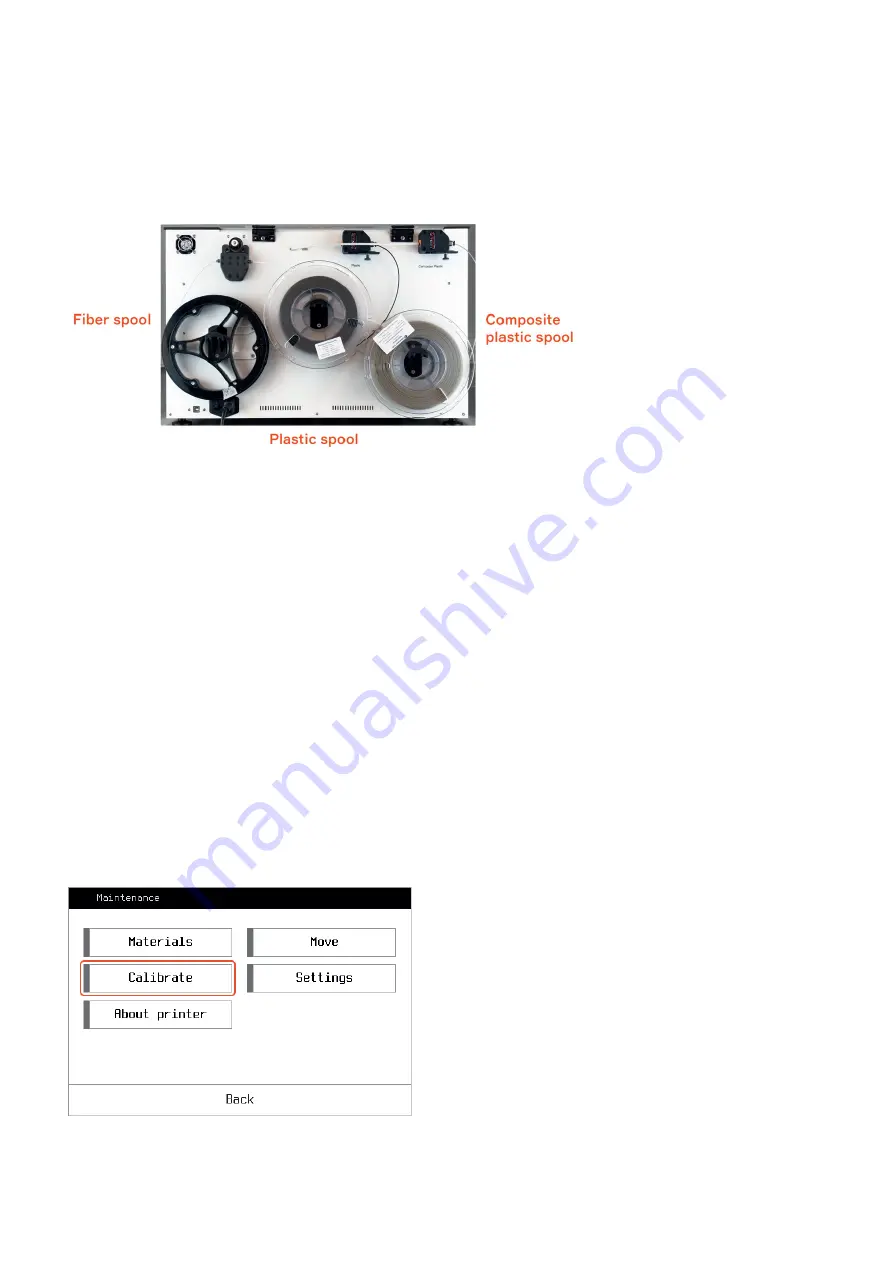
Composer User Manual
7.3. Loading materials
1. Take the 3 spools (plastic, composite plastic, and fiber) out of package and place them
onto the holders.
2. On the Composer screen, click
Maintenance > Materials >
and choose the material you want to load. Follow
instructions on the screen.
NOTICE:
Plastic can leak out of the composite heat block inlet during plastic filament loading in the composite
extruder. Just remove the leaked plastic with tweezers to prevent dripping of the plastic on the printed part.
7.4. Buildplate calibration
Your Composer had already been pre-calibrated before shipping, but due to transport vibrations, it could be
uncalibrated. Thus, you may need to go through the entire calibration procedure after the printer installation.
NOTICE
: Clean and preheat the nozzles and the buildplate to its printing temperatures before all the calibration
procedures (buildplate, Z axis, Z-offset) to prevent incorrect calibration.
You need to go through the buildplate calibration procedure after any changes affecting the positioning of the
buildplate, e.g. shaking or moving the printer. While printing a large part occupying the whole buildplate area, you
can notice layer thickness varies from one end of the part to another, which as well means the buildplate requires
recalibration.
19 / 57
Summary of Contents for Composer
Page 1: ...Composer User Manual Composer User Manual by Anisoprint Support 1 57...
Page 15: ...Composer User Manual Change active extruder Initiate fiber cutting mechanism 15 57...
Page 34: ...Composer User Manual 34 57...
Page 48: ...Composer User Manual 48 57...
Page 52: ...Composer User Manual 4 Using the wrench key or pliers unscrew the fiber guiding bushing 52 57...
Page 55: ...Composer User Manual 2 Remove the excessed fibers from the tube 55 57...
Page 56: ...Composer User Manual 3 Connect the tube to the printing head 56 57...
Page 57: ...Composer User Manual Powered by TCPDF www tcpdf org 57 57...