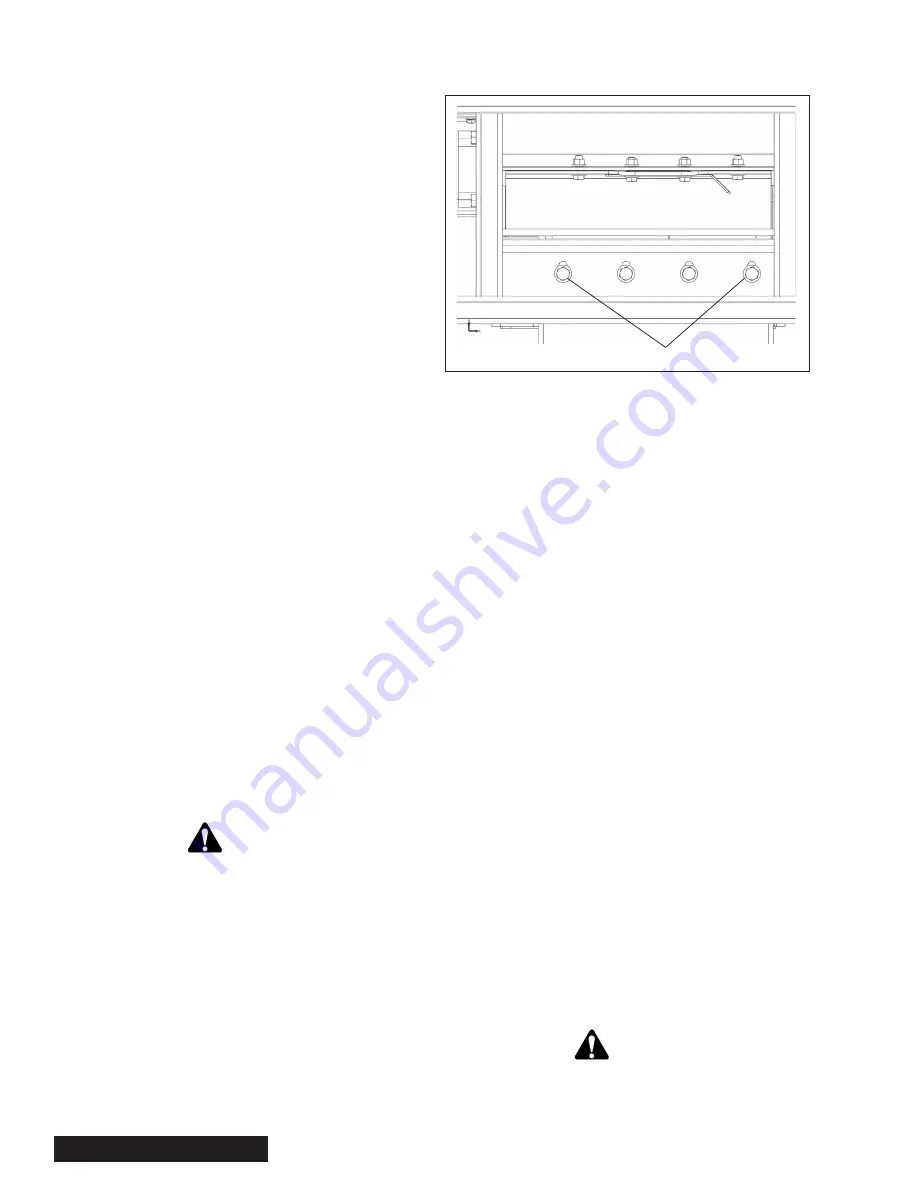
52 • Section 7 — Maintenance
can prevent the blade from lying perfectly flat on
its matting surface. Improper cap screw torque or
use of worn or damage cap screws can cause blade
separation. Always make sure proper maintenance
and replacement parts are used.
Notice
When installing new or sharpened blades, discard
the existing mounting cap screws and use new Altec
approved cap screws. Repeated reuse of the cap
screws will decrease their clamping capacity.
Drum Inspection
The cutter drum, air paddles, and blade pockets must
be thoroughly inspected for cracking or deformation. If
cracking or deformation is found please contact Altec
Environmental Products.
Blade Sharpening
Notice
The blades are double edged and have a minimum
usable size of 2” (5.08 cm) measured from the center-
line of the cap screw holes to the blade edge. Do not
use a side of a blade that measures less than this.
• Sharpen blades at a 30 degree angle.
• Use a soft J grade grinding wheel with a 36 to 40
grit.
• Use adequate coolant while grinding.
• Hone blades between sharpening.
Notice
On resharpened blades, measure the distance from
the mounting holes to the sharpened edges. Mount
blades so edges with the same measurements are
oriented the same way at both blade locations.
Anvil Removal/Installation
Danger
Blades and anvils are extremely sharp and can
severely cut your hands. Anytime you are storing,
handling or performing maintenance on blades or
anvils you must wear good quality leather palm
work gloves. This will greatly reduce the possibility
of serious injury.
Falling objects can cause serious eye injury.
Always wear goggles when working overhead.
Anvil Removal
1. Remove the four
1
/
2
-13 cap screws securing the hinged
anvil access cover and anvil/blade gap gauge.
Figure 7.6 — Anvil
2. If needed rotate the drum so cutter blades are not in
the work area.
3. Remove the four
5
/
8
-11 cap screws.
4. Remove the anvil and thoroughly clean all anvil/drum
head mating surfaces.
Anvil Installation
1. If blades are to be rotated or changed this should be
completed first. Refer to blade installation.
2. With all areas in the anvil location clean and free of
debris, install the anvil positioned with an unused
cutting edge at the blade to anvil cutting point.
3. Install the four anvil cap screws, do not tighten.
4. Slowly hand rotate the drum. Using the anvil gap
gauge, set the anvil to a blade clearance at the out-
board cap screw to
1
/
8
”. Hand tighten this outboard
cap screw.
5. Rotate the drum to the other blade, set the outboard
gap and hand tighten the outboard cap screw.
6. While verifying correct gap setting. Slowly hand
rotate the rotor across all anvil/blade contact points
to ensure proper blade/anvil clearance. Adjust as
necessary.
7. Torque anvil cap screws to specifications in the
fastener torque table.
Warning
Death or serious injury can occur from blade separa-
tion. Never use an impact wrench to tighten blade
or anvil cap screws. Always use a torque wrench.
Outboard Cap Screws
Summary of Contents for DRM 12
Page 3: ......
Page 7: ...2 Section 1 Introduction...
Page 17: ...12 Section 3 Safety Rear View Top View Bottom View 12 5 22 19 10 23 10 17 30 20 3 2 30...
Page 18: ...Section 3 Safety 13 4 8 7 2 3 970116658 1 6 5...
Page 19: ...14 Section 3 Safety 970116649 970116652 12 14 13 10 11 9...
Page 21: ...16 Section 3 Safety D G G D 25 26 24 27 23 22...
Page 22: ...Section 3 Safety 17 970137595 3X 30 31 28 29...
Page 23: ...18 Section 3 Safety...
Page 41: ...36 Section 6 Care of the Unit...
Page 62: ...Appendix...
Page 63: ......
Page 79: ...16 Appendix Glossary...
Page 83: ...Appendix Daily Preoperational Checklist...
Page 85: ...Appendix Preventive Maintenance and Inspection Checklist...
Page 88: ......
Page 89: ......
Page 91: ......
Page 93: ......
Page 96: ...07 13 970413443 A 2A PAGE 1 OF 2 ASSEMBLY FEED SYSTEM HYDRAULIC LIFT DRM 12...
Page 99: ...07 13 970413407 A 3A PAGE 1 OF 4 ASSEMBLY FEED CONTROL HYDRAULIC LIFT DRM 12...
Page 103: ...08 13 970485929 A 4A PAGE 1 OF 3 ASSEMBLY HAND CRANK CHUTE ROTATION DRUM CHIPPER...
Page 108: ...07 13 970413409 A 5A PAGE 1 OF 3 ASSEMBLY POWER SYSTEM KUBOTA 67 HP 74 HP 99 HP DIESEL DRM 12...
Page 113: ...07 13 970413438 A 6A PAGE 1 OF 4 FINAL ASSEMBLY DRM 12...
Page 117: ......
Page 118: ......
Page 119: ......
Page 120: ......
Page 121: ......
Page 122: ......
Page 123: ......
Page 124: ......
Page 125: ......
Page 127: ......
Page 128: ......
Page 129: ......
Page 138: ...79A PAGE 1 OF 3 05 13 970457633 A ASSEMBLY FUEL SYSTEM DRM12 CFD1217...