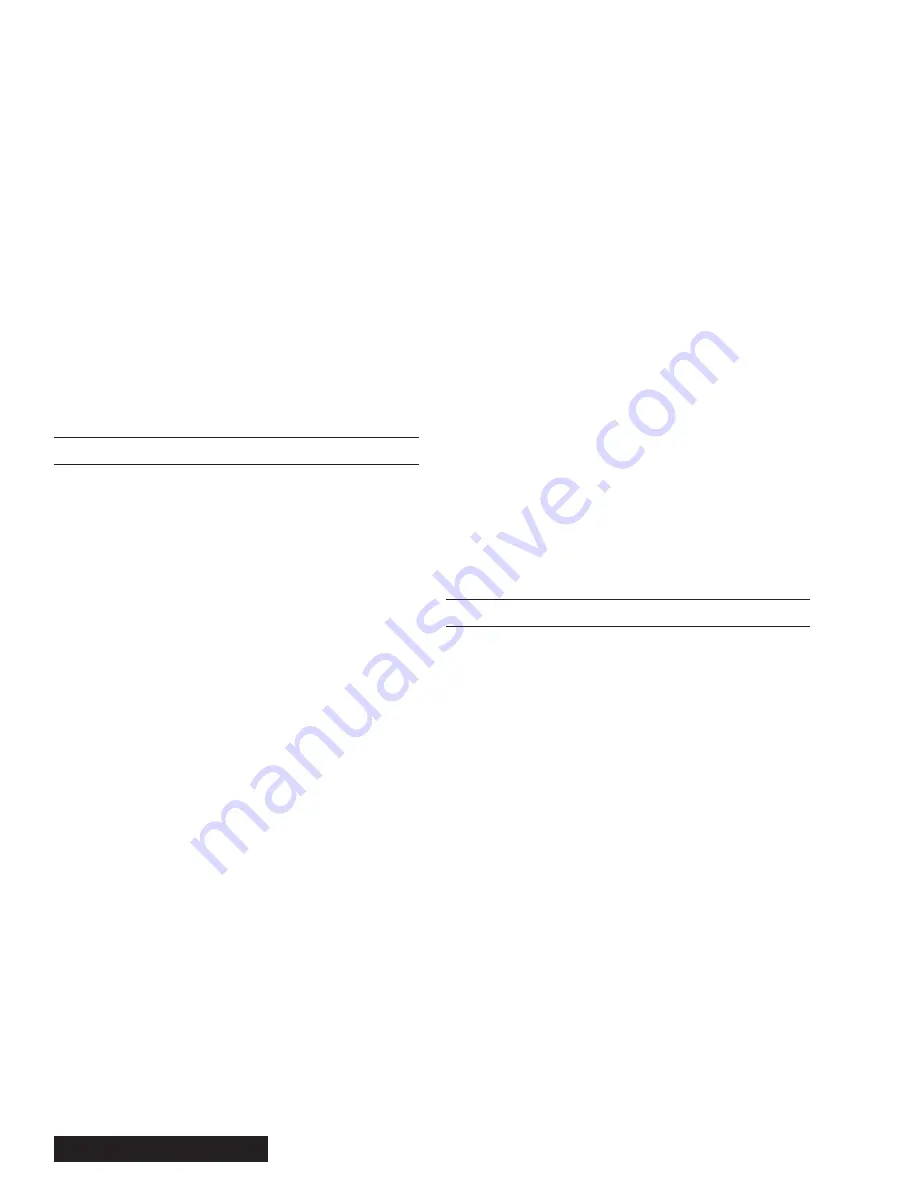
38 • Section 7 — Maintenance
General Maintenance Information
• Read and understand the complete procedure before
beginning.
• Remove the pressure in a hydraulic circuit before
disconnecting its components.
• Use lifting devices of suitable capacity to support
and handle components.
• Use a test block to adjust the relief setting on coun
-
terbalance holding valves.
• Be aware of your surroundings.
• Fully open all shutoff valves after servicing the unit.
• Complete the required procedures before returning
the unit to operation.
• After completing a procedure, check the oil level in
the hydraulic reservoir and add oil if necessary.
• Many inspections require the removal of covers.
After the inspection is complete, replace the covers
before returning the unit to service.
Equipment Storage
Mobile hydraulic equipment needs maintenance when
stored, or not used, for extensive periods of time. De
-
pending upon the climate, lack of use may begin to have
a negative effect in as little as two weeks. Storage for a
period of several months will almost certainly produce
some deterioration of the equipment.
Rust will form on unprotected ferrous metal surfaces very
quickly and water will collect inside unit structures. In dry
climates, gaskets will begin to shrink during long periods
of non-use, and lubricants will lose their ability to provide
lubrication. In cold climates, condensation may occur in
fluid reservoirs and other components.
Even when protective measures have been taken prior
to storage, some degradation of performance must be
expected when the equipment is put back into use.
Protective Measures
If it is known that equipment will be stored for a month
or more, some steps should be taken to preserve the
equipment.
1. The best preservative is to fully cycle (operate) the
equipment once weekly if even for a short time.
2. Coat exposed ferrous (iron or steel) bare metal
surfaces with a light grease or heavy oil compatible
with system hydraulic oil. This includes cylinder rods,
shafts, gears, linkages, and unpainted parts.
3. Top off fluid reservoirs to allow as little air space as
possible, to limit the effects of condensation. Remove
excess oil before operating to limit the chance of
overflow when cylinders are cycled.
4. Cover or wrap exposed rubber or neoprene parts
with an ultraviolet resistant covering to shield the
parts from sun exposure.
5. Unplug electrical connectors and apply a dielectric
grease or an aerosol product designed for protect-
ing electrical connectors. Plug the connector back
together.
6. Cover switch panels and control panels to prevent
direct intrusion of rain or moisture, while allowing air
to circulate over the panel.
7. While greasing slowly rotate all bearings until new
grease is seen purging from the bearing.
8. Repack axle wheel bearings.
9. Refer to engine manufacturer’s recommendations
on storage procedures.
10. Make sure the engine exhaust system and air intake
system are protected from water intake.
11. Secure all padlocks and remove keys from ignition.
12. Disconnect or remove battery.
Extended Storage
Engine Storage
Prior to extended storage, please refer to your engine
owner’s manual for proper storage procedure.
Chipper Storage
Things to do prior to extended chipper storage.
• Let the chipper cool to ambient temperature.
• While slowly rotating the drum, grease both bearings
until new grease is seen purging from the bearing
shaft/seal area.
• Repack wheel bearings.
• While slowly rotating the drive rollers, grease all drive
roll bearings until new grease is seen purging from
the shaft seal area.
• Make sure the fuel tank is full and not containing
water.
• Make sure the hydraulic tank is full and not containing
water.
Summary of Contents for DRM 12
Page 3: ......
Page 7: ...2 Section 1 Introduction...
Page 17: ...12 Section 3 Safety Rear View Top View Bottom View 12 5 22 19 10 23 10 17 30 20 3 2 30...
Page 18: ...Section 3 Safety 13 4 8 7 2 3 970116658 1 6 5...
Page 19: ...14 Section 3 Safety 970116649 970116652 12 14 13 10 11 9...
Page 21: ...16 Section 3 Safety D G G D 25 26 24 27 23 22...
Page 22: ...Section 3 Safety 17 970137595 3X 30 31 28 29...
Page 23: ...18 Section 3 Safety...
Page 41: ...36 Section 6 Care of the Unit...
Page 62: ...Appendix...
Page 63: ......
Page 79: ...16 Appendix Glossary...
Page 83: ...Appendix Daily Preoperational Checklist...
Page 85: ...Appendix Preventive Maintenance and Inspection Checklist...
Page 88: ......
Page 89: ......
Page 91: ......
Page 93: ......
Page 96: ...07 13 970413443 A 2A PAGE 1 OF 2 ASSEMBLY FEED SYSTEM HYDRAULIC LIFT DRM 12...
Page 99: ...07 13 970413407 A 3A PAGE 1 OF 4 ASSEMBLY FEED CONTROL HYDRAULIC LIFT DRM 12...
Page 103: ...08 13 970485929 A 4A PAGE 1 OF 3 ASSEMBLY HAND CRANK CHUTE ROTATION DRUM CHIPPER...
Page 108: ...07 13 970413409 A 5A PAGE 1 OF 3 ASSEMBLY POWER SYSTEM KUBOTA 67 HP 74 HP 99 HP DIESEL DRM 12...
Page 113: ...07 13 970413438 A 6A PAGE 1 OF 4 FINAL ASSEMBLY DRM 12...
Page 117: ......
Page 118: ......
Page 119: ......
Page 120: ......
Page 121: ......
Page 122: ......
Page 123: ......
Page 124: ......
Page 125: ......
Page 127: ......
Page 128: ......
Page 129: ......
Page 138: ...79A PAGE 1 OF 3 05 13 970457633 A ASSEMBLY FUEL SYSTEM DRM12 CFD1217...