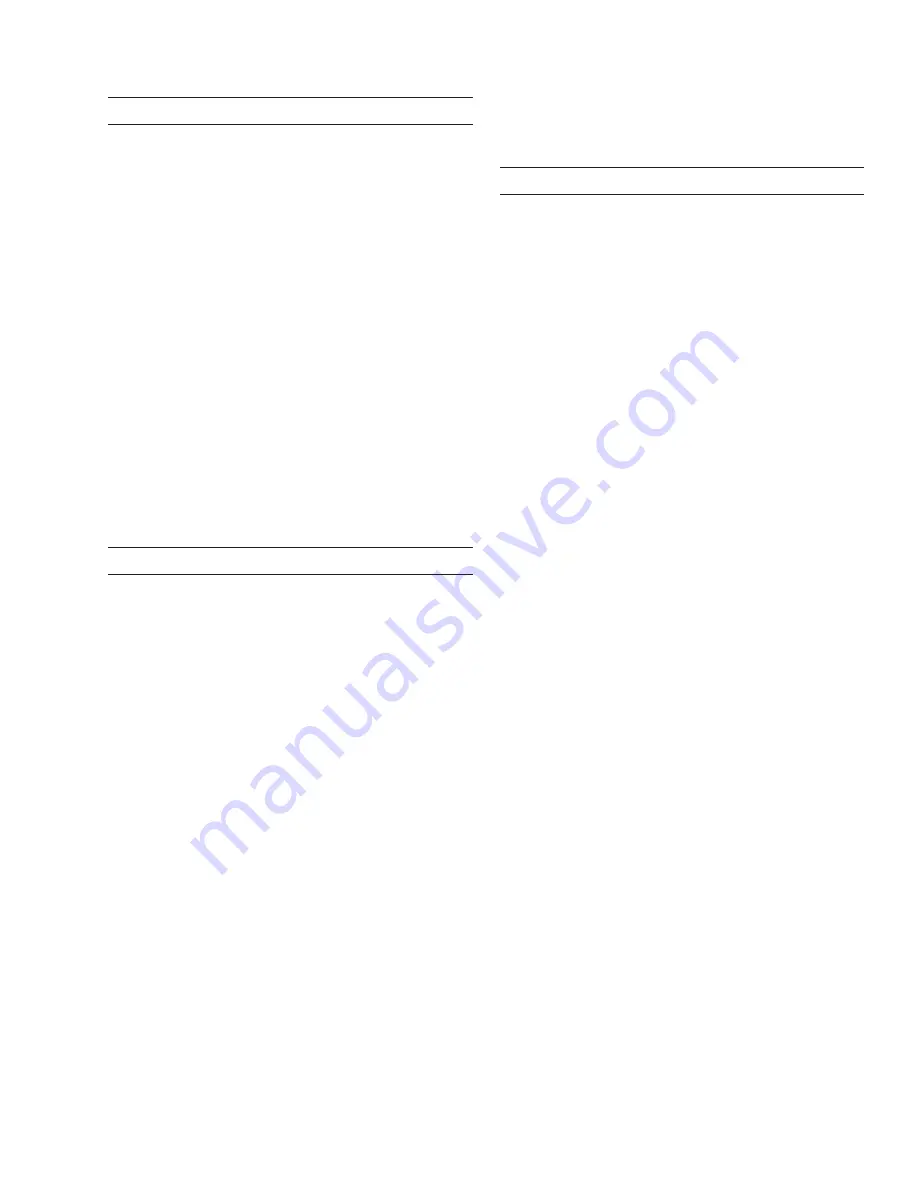
Section 6 — Care of the Unit • 35
Chipper Electric Braking System
The primary activation of the braking system is through
the brake controller of the tow vehicle to the electrical
chipper/tow vehicle connection through the chipper
wiring harness and into the electrically operated brake
assemblies. A secondary system starts with the chipper
battery through the breakaway switch, chipper wiring
harness and into the electrically operated brake assem-
blies. This secondary system is only operational when
the breakaway switch is activated. This system should
never be activated except for testing or in an emergency
chipper/tow vehicle separation.
Brake Adjustment
Adjust brakes at the following intervals. Refer to the axle
owners manual.
• After the first 200 miles of operation when the brake
shoes and drums have seated.
• At 3,000 mile intervals.
• As use and performance requires.
Hinge and Friction Points
Chipper operation and longevity can be improved by
keeping all hinges and friction points lubricated. Altec
Environmental Products, LLC recommends that lubri-
cation be performed weekly. Use SAE 30 weight oil on
hinges and a premium grade, high temperature lithium
based EP #2 grease on friction points.
Drum and Feed Roll Bearings
Lubricate daily with a premium quality NLGI #2 grade
multipurpose roller bearing grease. Some suggested
greases are: Mobile Mobilith AW 2, Shell Alvaina Grease
2, Texaco 1939 Premium RB, Amoco Rykon Premium
Grease #2 or an equivalent. Grease each bearing daily
with three or four pumps using a standard grease gun.
Feed Roller Pivot Points
Feed roller pivot points have a non-greaseable, oil impreg-
nated bushing. Lubrication of these points will inhibit the
designed method of lubrication and may cause excessive
wear of the bushings and shaft.
Notice
Always lubricate bearings and fill fuel and hydraulic
tanks at the end of each work day. This will displace
any moisture in the bearings and tanks. Also lubri
-
cate thoroughly prior to any extended shutdown or
storage.
Due to extended use or extreme conditions, additional
maintenance intervals and/or component inspections
may be necessary.
Summary of Contents for DRM 12
Page 3: ......
Page 7: ...2 Section 1 Introduction...
Page 17: ...12 Section 3 Safety Rear View Top View Bottom View 12 5 22 19 10 23 10 17 30 20 3 2 30...
Page 18: ...Section 3 Safety 13 4 8 7 2 3 970116658 1 6 5...
Page 19: ...14 Section 3 Safety 970116649 970116652 12 14 13 10 11 9...
Page 21: ...16 Section 3 Safety D G G D 25 26 24 27 23 22...
Page 22: ...Section 3 Safety 17 970137595 3X 30 31 28 29...
Page 23: ...18 Section 3 Safety...
Page 41: ...36 Section 6 Care of the Unit...
Page 62: ...Appendix...
Page 63: ......
Page 79: ...16 Appendix Glossary...
Page 83: ...Appendix Daily Preoperational Checklist...
Page 85: ...Appendix Preventive Maintenance and Inspection Checklist...
Page 88: ......
Page 89: ......
Page 91: ......
Page 93: ......
Page 96: ...07 13 970413443 A 2A PAGE 1 OF 2 ASSEMBLY FEED SYSTEM HYDRAULIC LIFT DRM 12...
Page 99: ...07 13 970413407 A 3A PAGE 1 OF 4 ASSEMBLY FEED CONTROL HYDRAULIC LIFT DRM 12...
Page 103: ...08 13 970485929 A 4A PAGE 1 OF 3 ASSEMBLY HAND CRANK CHUTE ROTATION DRUM CHIPPER...
Page 108: ...07 13 970413409 A 5A PAGE 1 OF 3 ASSEMBLY POWER SYSTEM KUBOTA 67 HP 74 HP 99 HP DIESEL DRM 12...
Page 113: ...07 13 970413438 A 6A PAGE 1 OF 4 FINAL ASSEMBLY DRM 12...
Page 117: ......
Page 118: ......
Page 119: ......
Page 120: ......
Page 121: ......
Page 122: ......
Page 123: ......
Page 124: ......
Page 125: ......
Page 127: ......
Page 128: ......
Page 129: ......
Page 138: ...79A PAGE 1 OF 3 05 13 970457633 A ASSEMBLY FUEL SYSTEM DRM12 CFD1217...