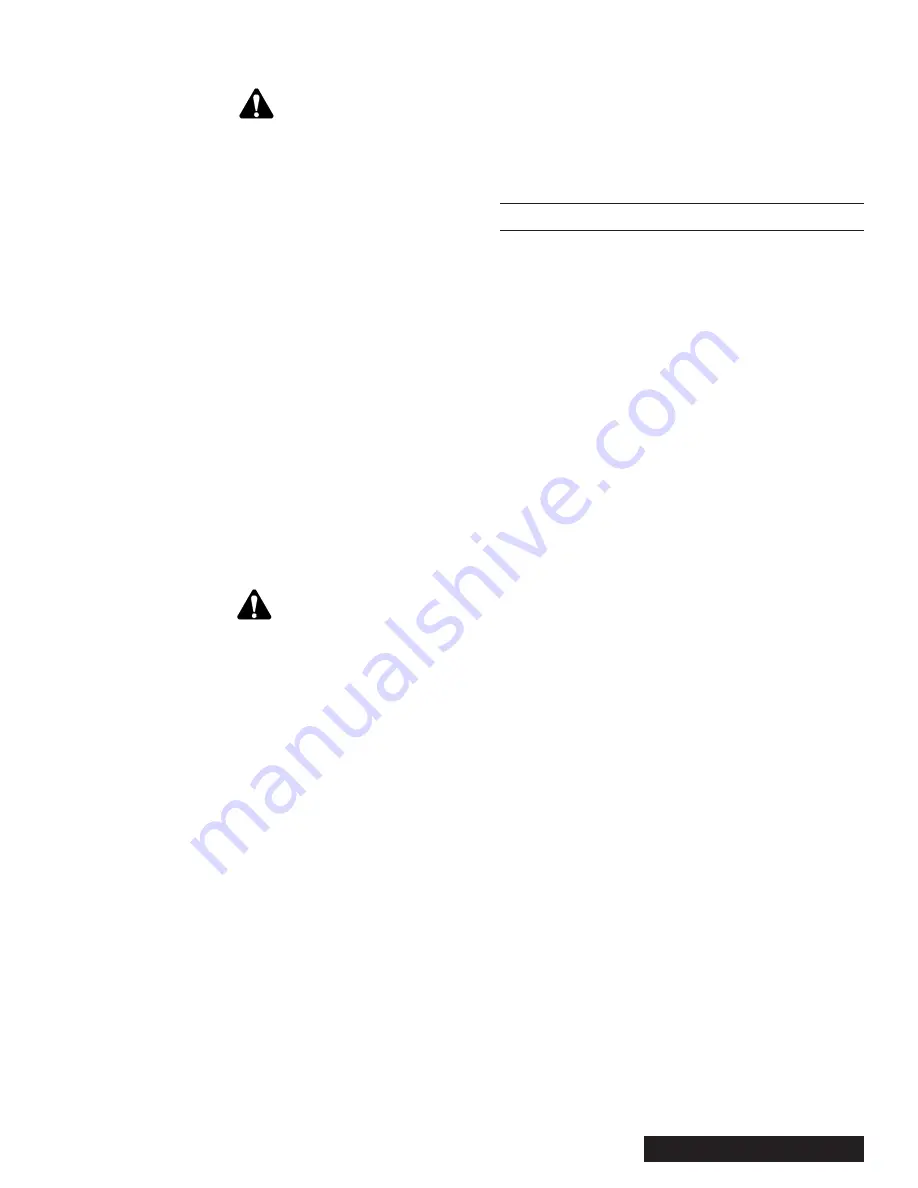
Section 7 — Maintenance • 45
Caution
Spilled hydraulic oil creates slick surfaces and can
cause personnel to slip and/or fall. Keep the unit and
work areas clean.
If a pressure washer or steam cleaner is used to clean
the unit, be careful where the spray is directed. Do not
direct the spray where the cleaning liquid might get into
electrical components, such as electrical connections,
switches or lights. Even though all electrical components
on the unit are designed for all weather use, it is possible
for water pressure from the nozzle to push a seal out of
position. Do not direct the spray at the filler breather cap
of the reservoir. The high pressure can force water and
cleaning liquid into the reservoir and contaminate the
hydraulic oil. Do not clean any of the hydraulic valve spool
ends or near cylinder rod seals with direct pressure from
a pressure washer. Limit the water pressure to 500 psi
(34.47 bar) and keep the spray tip at least 18
″
(45.72 cm)
away from these components while washing. After wash-
ing and cleaning the unit, relubricate as necessary.
Welds
All welds on the unit are originally applied in conformance
to AWS standards. Every weld on the unit is important
and should be periodically inspected.
Warning
Death or serious injury can result from improper
use of solvents. Follow the manufacturer’s label for
proper use and disposal.
If paint has lifted off the weld, or if rust is found, a closer
inspection is required. Remove any loose paint or rust
with a wire brush. Clean the area with a solvent such
as acetone. Closely inspect the area for cracks in the
welds. Dye penetration and magnetic particle testing are
simple processes that may be used to verify or disprove
a suspected problem.
Visual inspections can be very effective if conducted
properly. Clean the area to be inspected. Look for vis-
ible cracks in the weld and at the weld-to-parent material
joint. Use a bright light to provide adequate visibility of
the inspection area.
Pay close attention to welds that are located where
changes in cross section take place and near the attach-
ment points of highly loaded components. If any cracks
or unacceptable conditions are discovered, report them
to your Altec representative.
Any welds added in the field should be done by qualified
personnel and also conform to AWS standards.
After doing repair work on the unit, such as weld repair,
some testing of the unit may be required.
Fasteners
A variety of fasteners are used on the unit. Different fas
-
teners have different inspection and installation require-
ments depending on their use and design.
The standard grade of fastener used on the unit is a
zinc plated, SAE Grade 8, steel cap screw. A variety
of fasteners such as hex socket head, flat countersunk
head, button head cap screws, eye bolts and carriage
bolts are also used on the unit.
Check all fasteners for tightness as recommended by
the checklists.
When inspecting fasteners, pay particular attention to
the following fasteners.
• Blade fasteners
• Anvil fasteners
• Hitch and/or tongue fasteners
• Cutter bearing fasteners
• Control bar linkage fasteners
• Panic bar linkage fasteners
Refer to Torque Values in the Appendix as a guide to
determine the proper cap screw torque value. The proper
value is necessary to overcome the friction of the threads
and develop the required clamping force.
A properly installed cap screw applies a clamping force
equal to or greater than the load applied to it. A cap screw
installed at less than the recommended torque value
does not provide enough clamping force. The cap screw
may fatigue, causing it to loosen or fail. If the cap screw
is torqued beyond the recommended torque value, the
elastic range of the cap screw may be exceeded. This
may result in premature failure of the cap screw.
When checking fastener torque value, check at 90 percent
of the original value. For example, if the torque value for
a cap screw is 100 foot-pounds (136 N•m), check the cap
screw for tightness at 90 foot-pounds (122 N•m).
Certain types of fasteners or fasteners used in special
applications often require torque values that differ from
common torque charts. Check the Fastener Specific
Torque Application Chart in the Appendix.
Summary of Contents for DRM 12
Page 3: ......
Page 7: ...2 Section 1 Introduction...
Page 17: ...12 Section 3 Safety Rear View Top View Bottom View 12 5 22 19 10 23 10 17 30 20 3 2 30...
Page 18: ...Section 3 Safety 13 4 8 7 2 3 970116658 1 6 5...
Page 19: ...14 Section 3 Safety 970116649 970116652 12 14 13 10 11 9...
Page 21: ...16 Section 3 Safety D G G D 25 26 24 27 23 22...
Page 22: ...Section 3 Safety 17 970137595 3X 30 31 28 29...
Page 23: ...18 Section 3 Safety...
Page 41: ...36 Section 6 Care of the Unit...
Page 62: ...Appendix...
Page 63: ......
Page 79: ...16 Appendix Glossary...
Page 83: ...Appendix Daily Preoperational Checklist...
Page 85: ...Appendix Preventive Maintenance and Inspection Checklist...
Page 88: ......
Page 89: ......
Page 91: ......
Page 93: ......
Page 96: ...07 13 970413443 A 2A PAGE 1 OF 2 ASSEMBLY FEED SYSTEM HYDRAULIC LIFT DRM 12...
Page 99: ...07 13 970413407 A 3A PAGE 1 OF 4 ASSEMBLY FEED CONTROL HYDRAULIC LIFT DRM 12...
Page 103: ...08 13 970485929 A 4A PAGE 1 OF 3 ASSEMBLY HAND CRANK CHUTE ROTATION DRUM CHIPPER...
Page 108: ...07 13 970413409 A 5A PAGE 1 OF 3 ASSEMBLY POWER SYSTEM KUBOTA 67 HP 74 HP 99 HP DIESEL DRM 12...
Page 113: ...07 13 970413438 A 6A PAGE 1 OF 4 FINAL ASSEMBLY DRM 12...
Page 117: ......
Page 118: ......
Page 119: ......
Page 120: ......
Page 121: ......
Page 122: ......
Page 123: ......
Page 124: ......
Page 125: ......
Page 127: ......
Page 128: ......
Page 129: ......
Page 138: ...79A PAGE 1 OF 3 05 13 970457633 A ASSEMBLY FUEL SYSTEM DRM12 CFD1217...