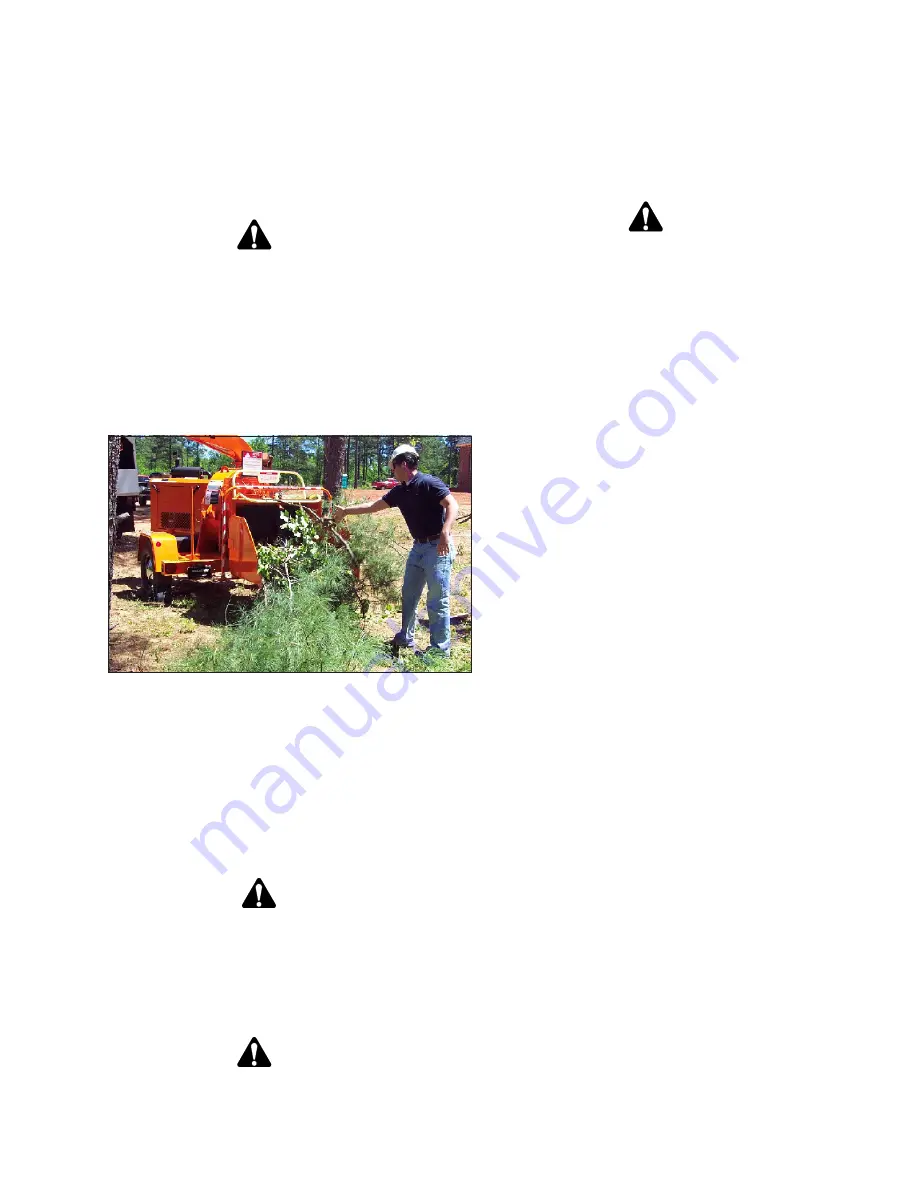
Section 4 — Before You Operate… • 29
7. Instruct operators to grip the handle with a relaxed
grip and to release if entrapped in brush or feed roller.
8. Replace damaged or missing pusher. Do not use
the paddle to push rakings that may contain rocks,
metal or other non-wood materials.
Warning
Death or serious injury can result if proper feeding
techniques are not followed. Never place any part
of the body including hands, arms, face, or torso
above a piece of material that is being engaged into
the feed rollers.
Material can be violently kicked up or shifted causing
direct impact or entrapment between the material being
fed and the chipper infeed chute.
Figure 4.6 — Releasing the Material
Slide large material along bottom of infeed chute from
the rear pushing it into the chipper feeding rolls. Release
material as soon as it engages with the rolls.
Winch Safety and Operation
(Optional Equipment)
Read and understand the entire manual prior to operation
of the chipper or the winch.
Danger
Death or serious injury will result from careless or
improper use of the unit. Do not operate the unit
without proper training.
Only those properly trained and authorized by the em-
ployer shall operate the winch.
Warning
Death, serious injury, and/or property damage can
result from feeding material that is not wood into
the chipper. Inspect all material before it is fed into
the chipper.
Always remove the cable assembly prior to feeding mate-
rial into the chipper.
Warning
Death or serious injury can result from personnel
entanglement or crushing. Always make sure person-
nel are aware of cable/material location and changing
pinch point hazards.
Safety
Wear all personal protective clothing and equipment
as designated by your company policy, OSHA, or other
governing organizations.
Make sure you place yourself and coworkers in proper,
safe positions while hoisting. Always increase chipper
operational area during winch operations. While hoist-
ing always be aware of the pinch points between hand,
foot, and body with the cable, wood and between towed
object and any fixed objects. These pinch points are
constantly changing during the hoisting operation. Cable
may create loops on the ground. Caution must be taken
to avoid entrapment in these loops. Never pull with tow
vehicle using the cable as a dragline. Always attempt to
pull from directly behind the chipper. When not in use
always properly stow hook and cable out of the feed zone
area. Chipper must always be properly hitched to the tow
vehicle and the vehicle must be properly chocked in place.
Daily Inspection
Inspect winch line, hook assembly, and winch structure
for damage or excessive wear prior to use. Ensure proper
operation of winch controls. Cable must be inspected for
broken/worn strands, or other physical damage which
would degrade the operational load capacity. The hook
must be inspected for wear and deformation such as
hook opening spread. Winch structure must be inspected
for structural deformation, cracked or broken welds and
proper fasteners in place and tight.
Operation
Place panic bar in the non-operational position. This will
stop feed roller movement, and allow the winch and lift
cylinder to continue operation. The winch control valve
is located on the curb side of the infeed chute. Always
keep tension on the cable while unspooling. Have an
assistant walk the cable out to the desired location.
Secure the cable to the material to be chipped 2’ to 3’
(61 to 91.4 cm) from the end. This will allow you to place
the end of the material on the infeed chute. After hoisting
the material to the desired position. Remove the cable
and secure the hook in the storage position putting slight
Summary of Contents for DRM 12
Page 3: ......
Page 7: ...2 Section 1 Introduction...
Page 17: ...12 Section 3 Safety Rear View Top View Bottom View 12 5 22 19 10 23 10 17 30 20 3 2 30...
Page 18: ...Section 3 Safety 13 4 8 7 2 3 970116658 1 6 5...
Page 19: ...14 Section 3 Safety 970116649 970116652 12 14 13 10 11 9...
Page 21: ...16 Section 3 Safety D G G D 25 26 24 27 23 22...
Page 22: ...Section 3 Safety 17 970137595 3X 30 31 28 29...
Page 23: ...18 Section 3 Safety...
Page 41: ...36 Section 6 Care of the Unit...
Page 62: ...Appendix...
Page 63: ......
Page 79: ...16 Appendix Glossary...
Page 83: ...Appendix Daily Preoperational Checklist...
Page 85: ...Appendix Preventive Maintenance and Inspection Checklist...
Page 88: ......
Page 89: ......
Page 91: ......
Page 93: ......
Page 96: ...07 13 970413443 A 2A PAGE 1 OF 2 ASSEMBLY FEED SYSTEM HYDRAULIC LIFT DRM 12...
Page 99: ...07 13 970413407 A 3A PAGE 1 OF 4 ASSEMBLY FEED CONTROL HYDRAULIC LIFT DRM 12...
Page 103: ...08 13 970485929 A 4A PAGE 1 OF 3 ASSEMBLY HAND CRANK CHUTE ROTATION DRUM CHIPPER...
Page 108: ...07 13 970413409 A 5A PAGE 1 OF 3 ASSEMBLY POWER SYSTEM KUBOTA 67 HP 74 HP 99 HP DIESEL DRM 12...
Page 113: ...07 13 970413438 A 6A PAGE 1 OF 4 FINAL ASSEMBLY DRM 12...
Page 117: ......
Page 118: ......
Page 119: ......
Page 120: ......
Page 121: ......
Page 122: ......
Page 123: ......
Page 124: ......
Page 125: ......
Page 127: ......
Page 128: ......
Page 129: ......
Page 138: ...79A PAGE 1 OF 3 05 13 970457633 A ASSEMBLY FUEL SYSTEM DRM12 CFD1217...