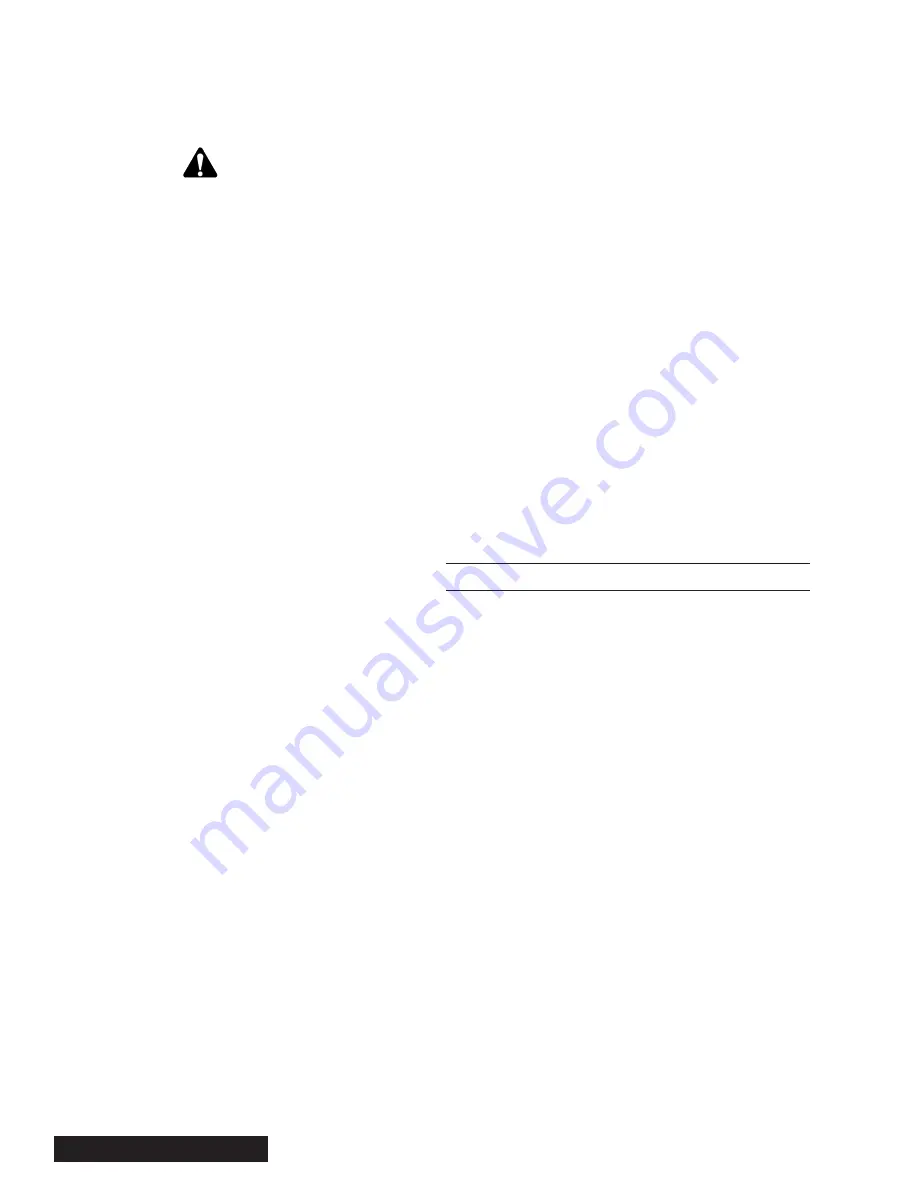
42 • Section 7 — Maintenance
3. Wipe off the top of the reservoir and the filler breather
cap.
Warning
Death or serious injury can result from improper
use of solvents. Follow the manufacturer’s label for
proper use and disposal.
4. Inspect the inside of the reservoir. If sludge or other
contamination is found, thoroughly clean the inside
of the tank using lint free wipes and a solvent which
leaves no residue. Change the return line filter and
clean or change the suction filter.
Notice
Only use hydraulic oil as recommended. Other fluids
added to the hydraulic system can increase compo-
nent wear and affect the lubricating characteristics
of the oil.
5. Fill the reservoir with new hydraulic oil of the proper
grade. The proper oil level is between 2” and 3”
(5.08 and 7.62 cm) from the top of the tank. Do not
fill tank completely full so as to leave room for fluid
expansion. Filter the oil through a 10 micron filter as
it is put into the reservoir.
6. Install the filler breather cap. If the filler breather cap
has not been replaced in one year, or is damaged,
replace it.
Notice
Oil change has been completed at step 6 for routine
oil changes. If changing oil due to contamination,
continue through step 11.
7. Cycle all cylinders, hydraulic motor and all valves to
flush contaminated oil from the lines and components
of the hydraulic system.
8. Change the return line filter cartridge and clean
the suction filter element.
9. Drain the reservoir completely.
10. Fill the reservoir with new hydraulic oil of the proper
grade. The proper oil level is between 2” and 3”
(5.08 and 7.62 cm) from the top of the tank. Do not
fill tank completely full so as to leave room for fluid
expansion. Filter the oil through a 10 micron filter as
it is put into the reservoir.
11. Change the return line filter cartridge after approxi
-
mately 25 hours.
Water Removal
If the hydraulic system was contaminated with water,
special water removal filtration may be necessary. An
oil supplier or a qualified laboratory can determine if
water has caused excessive oil oxidation or additive
deterioration.
If analysis shows oil deterioration beyond an accept-
able level, drain the reservoir and flush the system as
described earlier in this section. Use a water removal
filtration system during the flushing process to remove
any residual water from the system.
If the condition of the oil is acceptable except for the water
content, allow time for it to separate from the oil. Then
drain the water off the bottom of the reservoir. Circulate
the oil in the entire system through a separate water
removal filter system.
Continue this process until the water content in the oil is
reduced to an acceptable level. The preferred method
of determining the water content in the oil is laboratory
testing. Once the water content has been reduced to an
acceptable level, replace the cartridge with a new return
line cartridge.
Lubrication
Proper lubrication will extend the life of the equipment
and reduce maintenance problems. The frequency of
lubrication required will depend on the amount of use
and the conditions the unit is operated in. Operation in
extremely dusty, sandy, or rainy environments will require
more frequent lubrication. Lubricate the unit as recom-
mended by the Preventive Maintenance and Inspection
Checklist in the Appendix.
The Lubrication Chart identifies each component, type of
lubricant, and method of application. Any brand of lubricant
that meets or exceeds the specifications of the products
listed is acceptable. Select the appropriate interval and
lubricate the components as identified in the chart.
Always wipe grease fittings clean before and after greasing
to keep contaminants from entering the points of lubrica-
tion. To avoid bearing damage, use manually operated
grease guns. Air-driven grease guns may have enough
force to cause bearing damage.
If the unit is not used, or is stored for any length of time,
apply fresh lubricant at all points indicated on the Lubri-
cation Chart. This will help prevent corrosion during the
idle period.
Summary of Contents for DRM 12
Page 3: ......
Page 7: ...2 Section 1 Introduction...
Page 17: ...12 Section 3 Safety Rear View Top View Bottom View 12 5 22 19 10 23 10 17 30 20 3 2 30...
Page 18: ...Section 3 Safety 13 4 8 7 2 3 970116658 1 6 5...
Page 19: ...14 Section 3 Safety 970116649 970116652 12 14 13 10 11 9...
Page 21: ...16 Section 3 Safety D G G D 25 26 24 27 23 22...
Page 22: ...Section 3 Safety 17 970137595 3X 30 31 28 29...
Page 23: ...18 Section 3 Safety...
Page 41: ...36 Section 6 Care of the Unit...
Page 62: ...Appendix...
Page 63: ......
Page 79: ...16 Appendix Glossary...
Page 83: ...Appendix Daily Preoperational Checklist...
Page 85: ...Appendix Preventive Maintenance and Inspection Checklist...
Page 88: ......
Page 89: ......
Page 91: ......
Page 93: ......
Page 96: ...07 13 970413443 A 2A PAGE 1 OF 2 ASSEMBLY FEED SYSTEM HYDRAULIC LIFT DRM 12...
Page 99: ...07 13 970413407 A 3A PAGE 1 OF 4 ASSEMBLY FEED CONTROL HYDRAULIC LIFT DRM 12...
Page 103: ...08 13 970485929 A 4A PAGE 1 OF 3 ASSEMBLY HAND CRANK CHUTE ROTATION DRUM CHIPPER...
Page 108: ...07 13 970413409 A 5A PAGE 1 OF 3 ASSEMBLY POWER SYSTEM KUBOTA 67 HP 74 HP 99 HP DIESEL DRM 12...
Page 113: ...07 13 970413438 A 6A PAGE 1 OF 4 FINAL ASSEMBLY DRM 12...
Page 117: ......
Page 118: ......
Page 119: ......
Page 120: ......
Page 121: ......
Page 122: ......
Page 123: ......
Page 124: ......
Page 125: ......
Page 127: ......
Page 128: ......
Page 129: ......
Page 138: ...79A PAGE 1 OF 3 05 13 970457633 A ASSEMBLY FUEL SYSTEM DRM12 CFD1217...