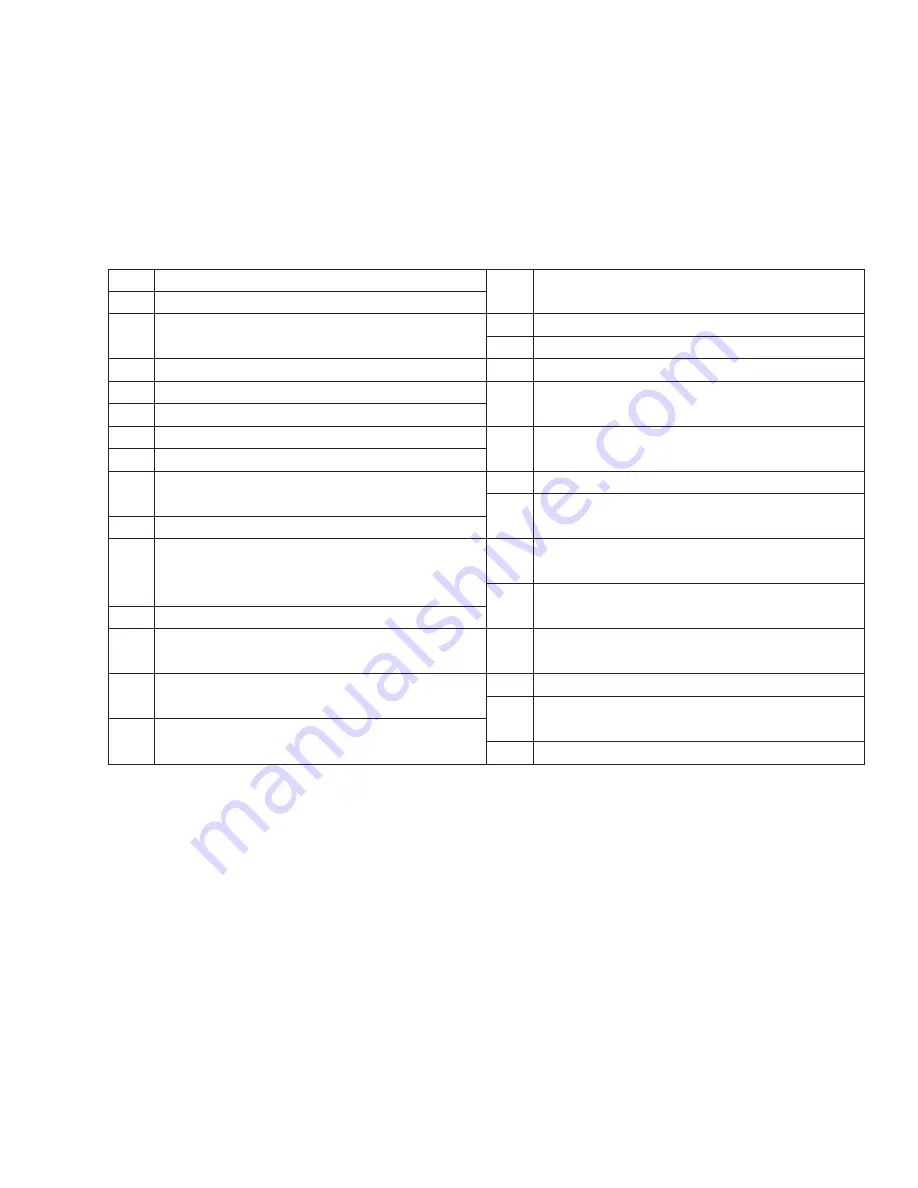
Appendix — Daily Preoperational Checklist
Daily Preoperational Checklist
VIN No. _________________________ Location ___________________________ Date __________________
Model Number ___________________________ Date of Manufacture __________________________________
Hours Meter _________________________ Inspector _______________________________________________
Symbols
/O = Okay or completed
C = Corrected by inspector
R = Repair or replacement required
U = Unsafe to operate
N/A = Not applicable
Chip curtain is properly fastened and in good repair
Rotation indicator is clear of debris and fully visible
Disc/drum cover padlock is in place and key is in
responsible party’s possession
Disc/drum hood switch is working properly
Inspect safety tow chains for wear or damage
Check engine fuel, coolant, and oil levels (refer to EOM)
Check the engine air filter (refer to EOM)
Check clutch handle free play
Check radiator fins and ensure free passage of air
through the radiator
All cap screws and nuts are tight and secure
Inspect anvil to make sure all attachment and
adjustment cap screws are secure and anvil edge
is in good condition
Check all controls for free and proper operation
Inspect the chipper frame and structure for any bent,
broken, cracked, missing, or loose parts
Check all guards to make sure they are undamaged,
in place, and properly secured
All decals must be in place and legible prior to
operating the chipper
Hydraulic fluid level must be within 2” to 3” (5.08 to
7.62 cm) of top of the tank when the fluid is cold
Lubricate cutter and feed roll bearings
Inspect and operate panic bar
Inspect for hydraulic leaks
Check cutting blades to make sure all attachment cap
screws are tight and blades are in good condition
Inspect discharge chute to determine if it is clear,
properly positioned, and secure
Check feed roller for debris
Check the transition area for debris that could lock
the drum or disc during start up
Make sure the safety devices are properly installed
and functioning properly
Make sure the feed table is in place and secure for
both operation and travel
No loose tools or materials on the chipper or on the
infeed chute
Wheels and tires are secure and properly inflated
Make sure a complete AEP Operator’s Manual is
available for all operators to review
Comments __________________________________________________________________________________
___________________________________________________________________________________________
Summary of Contents for DRM 12
Page 3: ......
Page 7: ...2 Section 1 Introduction...
Page 17: ...12 Section 3 Safety Rear View Top View Bottom View 12 5 22 19 10 23 10 17 30 20 3 2 30...
Page 18: ...Section 3 Safety 13 4 8 7 2 3 970116658 1 6 5...
Page 19: ...14 Section 3 Safety 970116649 970116652 12 14 13 10 11 9...
Page 21: ...16 Section 3 Safety D G G D 25 26 24 27 23 22...
Page 22: ...Section 3 Safety 17 970137595 3X 30 31 28 29...
Page 23: ...18 Section 3 Safety...
Page 41: ...36 Section 6 Care of the Unit...
Page 62: ...Appendix...
Page 63: ......
Page 79: ...16 Appendix Glossary...
Page 83: ...Appendix Daily Preoperational Checklist...
Page 85: ...Appendix Preventive Maintenance and Inspection Checklist...
Page 88: ......
Page 89: ......
Page 91: ......
Page 93: ......
Page 96: ...07 13 970413443 A 2A PAGE 1 OF 2 ASSEMBLY FEED SYSTEM HYDRAULIC LIFT DRM 12...
Page 99: ...07 13 970413407 A 3A PAGE 1 OF 4 ASSEMBLY FEED CONTROL HYDRAULIC LIFT DRM 12...
Page 103: ...08 13 970485929 A 4A PAGE 1 OF 3 ASSEMBLY HAND CRANK CHUTE ROTATION DRUM CHIPPER...
Page 108: ...07 13 970413409 A 5A PAGE 1 OF 3 ASSEMBLY POWER SYSTEM KUBOTA 67 HP 74 HP 99 HP DIESEL DRM 12...
Page 113: ...07 13 970413438 A 6A PAGE 1 OF 4 FINAL ASSEMBLY DRM 12...
Page 117: ......
Page 118: ......
Page 119: ......
Page 120: ......
Page 121: ......
Page 122: ......
Page 123: ......
Page 124: ......
Page 125: ......
Page 127: ......
Page 128: ......
Page 129: ......
Page 138: ...79A PAGE 1 OF 3 05 13 970457633 A ASSEMBLY FUEL SYSTEM DRM12 CFD1217...