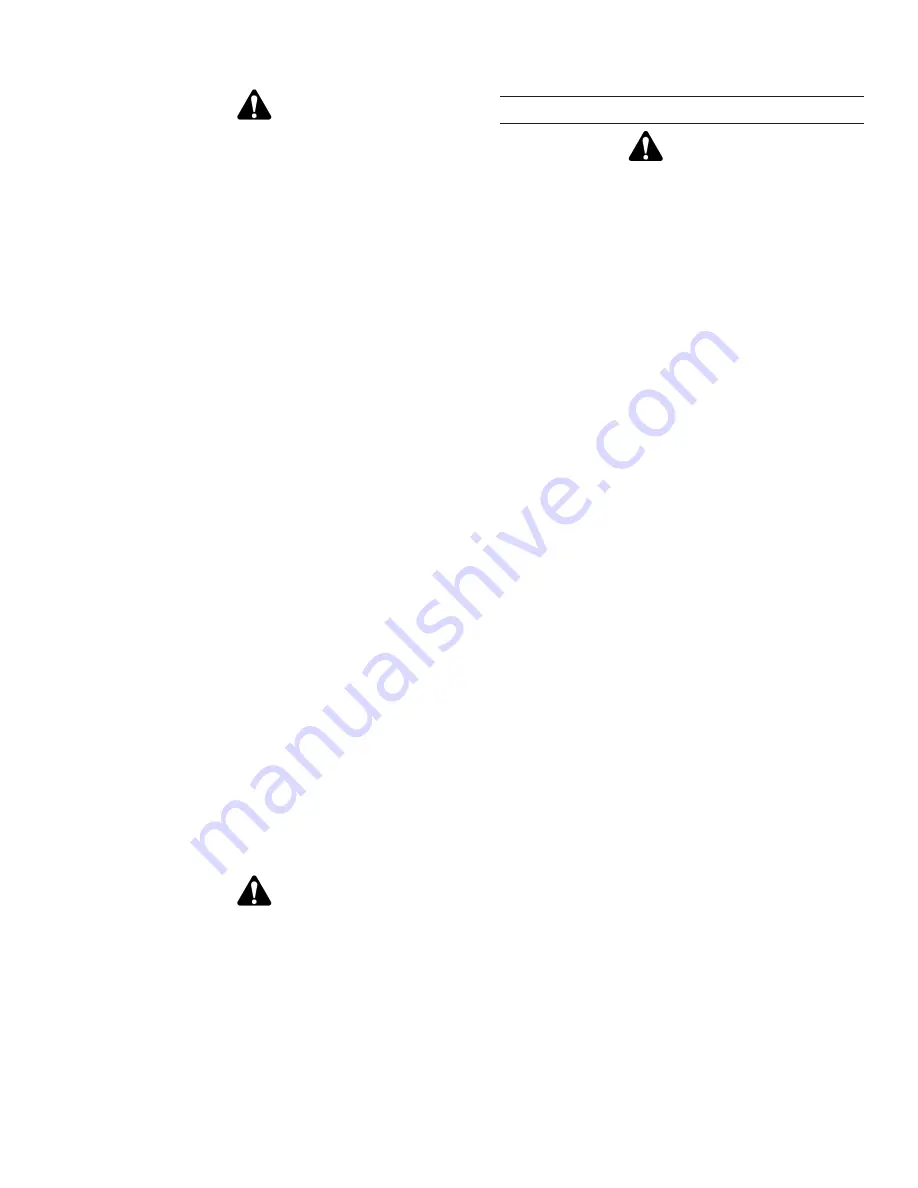
Section 4 — Before You Operate… • 23
Warning
Death or serious injury can result from airborne
materials. Make sure no personnel are in the path of
material that might be discharged from chipper.
2. Verify discharge chute is properly directed and se-
cured. Materials left in cutter housing or discharge
chute may discharge during clutch engagement and
rpm run-up.
3. Engine rpm should be at approximately 1,000 rpm or
the engagement setting on fixed position throttles.
4. Slowly engage the clutch. Stop if any unusual sounds
are heard. Investigate prior to proceeding.
5. After engine has stabilized at the engagement rpm,
slowly increase engine rpm to the preset operating
speed.
Notice
Equipment damage can result when attempting a
clutch engagement with a plugged cutter housing or
discharge chute. Never attempt to unplug a chipper
using rapid or repeated clutch engagements.
FeedSense
®
(Electronic Feed Control)
Maintaining proper operating rpm is a critical part of ef-
ficient chipper operation. If rpm is allowed to fall below
design parameters the velocity of discharging chipped
material will fall, resulting in discharge chute clogging.
The FeedSense® system automatically controls rpm
through control of the hydraulically driven feed roller(s).
When the system is on, the controller senses cutter speed.
When the cutter drops to a preset minimum rpm, the feed
roller(s) is temporarily stopped until the engine recovers
to its preset operating rpm. After engine recovery, the
FeedSense® automatically begins the forward feeding
process and continues as long as rpm is maintained
above the low set point.
Warning
Death or serious injury can result from unexpected
movement. Material will advance automatically when
the FeedSense
®
is activated.
After material has been engaged by the chipper always
stay clear of possible entanglement hazards.
Work Site Preparation
Warning
Death or serious injury can result from improper
chipper setup or work site preparation.
When unhitching the chipper from the tow vehicle,
confirm the chipper wheels are blocked. Make sure the
jack stand is undamaged and properly configured to
support the weight of the chipper. Damaged jack stands
should be replaced before supporting the chipper. Do
not operate the chipper without being properly hitched
to the tow vehicle.
The chipper tongue weight is too great for one person to
lift safely. Serious muscle strains can result if attempted
alone. Get help when hitching and unhitching the chip-
per.
Never stand between the tow vehicle and the chipper
while the tow vehicle is backing. Make sure the tow
vehicle is securely parked and the driver notified before
approaching the area between the chipper unit and the
tow vehicle. Coordinate signals with all personnel to
ensure accurate communication.
Make sure the discharge chute is properly directed and
locked in place.
Prior to starting the engine, check the infeed chute to
make sure it is clear of foreign material such as wrenches,
axes, etc.
Organization and preparation of the work site and brush
is a major factor in safe chipper operations.
Operating personnel must observe the following points
to ensure safety.
• Work sites should be clear of vehicle and pedestrian
traffic.
• Signs, cones, ropes, barriers, and/or flagmen may be
required to provide adequate warning and diversion
of automotive and/or pedestrian traffic.
• Do not operate the chipper beneath a potential drop
zone and verify that no one is performing work over
-
head of the chipper or chipper work zone.
• Provide a clear area on the curb side of the chipper
to allow the operator to maneuver while feeding the
chipper.
Summary of Contents for DRM 12
Page 3: ......
Page 7: ...2 Section 1 Introduction...
Page 17: ...12 Section 3 Safety Rear View Top View Bottom View 12 5 22 19 10 23 10 17 30 20 3 2 30...
Page 18: ...Section 3 Safety 13 4 8 7 2 3 970116658 1 6 5...
Page 19: ...14 Section 3 Safety 970116649 970116652 12 14 13 10 11 9...
Page 21: ...16 Section 3 Safety D G G D 25 26 24 27 23 22...
Page 22: ...Section 3 Safety 17 970137595 3X 30 31 28 29...
Page 23: ...18 Section 3 Safety...
Page 41: ...36 Section 6 Care of the Unit...
Page 62: ...Appendix...
Page 63: ......
Page 79: ...16 Appendix Glossary...
Page 83: ...Appendix Daily Preoperational Checklist...
Page 85: ...Appendix Preventive Maintenance and Inspection Checklist...
Page 88: ......
Page 89: ......
Page 91: ......
Page 93: ......
Page 96: ...07 13 970413443 A 2A PAGE 1 OF 2 ASSEMBLY FEED SYSTEM HYDRAULIC LIFT DRM 12...
Page 99: ...07 13 970413407 A 3A PAGE 1 OF 4 ASSEMBLY FEED CONTROL HYDRAULIC LIFT DRM 12...
Page 103: ...08 13 970485929 A 4A PAGE 1 OF 3 ASSEMBLY HAND CRANK CHUTE ROTATION DRUM CHIPPER...
Page 108: ...07 13 970413409 A 5A PAGE 1 OF 3 ASSEMBLY POWER SYSTEM KUBOTA 67 HP 74 HP 99 HP DIESEL DRM 12...
Page 113: ...07 13 970413438 A 6A PAGE 1 OF 4 FINAL ASSEMBLY DRM 12...
Page 117: ......
Page 118: ......
Page 119: ......
Page 120: ......
Page 121: ......
Page 122: ......
Page 123: ......
Page 124: ......
Page 125: ......
Page 127: ......
Page 128: ......
Page 129: ......
Page 138: ...79A PAGE 1 OF 3 05 13 970457633 A ASSEMBLY FUEL SYSTEM DRM12 CFD1217...