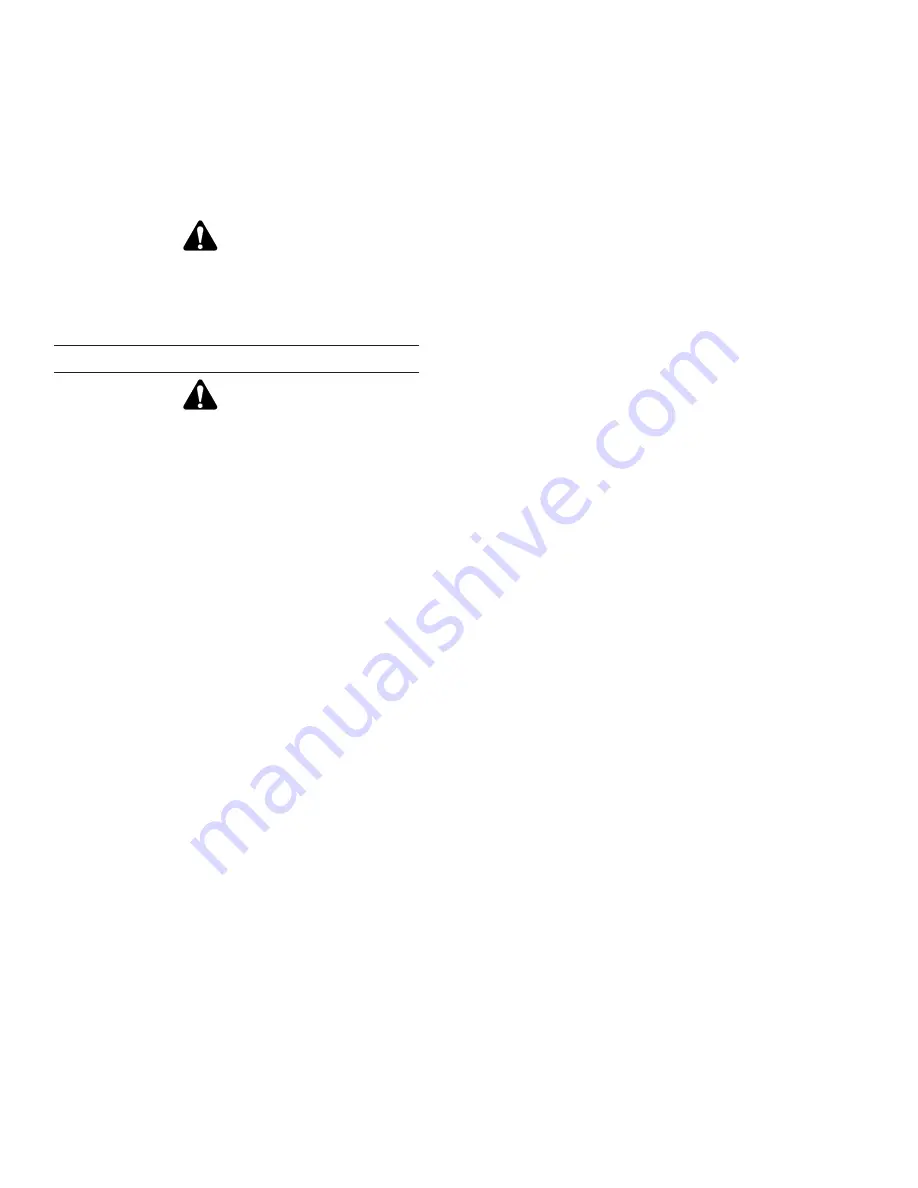
32 • Section 5 — Clearing Feed System and Discharge Chute
9. Reconnect battery cable.
10. Restart engine.
11. Return upper feed roll to the normal operating posi-
tion.
Warning
Death or serious injury can result if the upper feed
roller is not returned to the proper position. Do not
feed material into the chipper with the upper feed
roller in the locked open position.
Discharge Chute
Warning
Death or serious injury can result if proper discharge
chute clearing procedures are not followed. Only
personnel properly trained and authorized may per-
form this operation.
Never operate the chipper with the discharge chute
removed or material jammed in the chute.
Never attempt to clear the discharge chute while the
chipper is in operation.
Always make sure the engine is shut off and all drive and
cutter components have come to a complete stop.
Complete LOTO procedures.
Always use proper hoisting equipment.
The plugged discharge chute can weigh more than 200
pounds (90.7 kg). Use appropriate hoisting equipment
when removing the chute.
1. Attach hoisting equipment to chute.
2. Unbolt the split ring attachment bolts. Remove the
split ring.
3. Using the hoisting equipment remove the chute.
4. Use appropriate tools to unplug the chute.
5. Check drum housing/chute transition and clean out
if necessary.
6. Reinstall discharge chute.
Notice
PTO or drive train may be damaged from chute plug-
ging or attempting to start the chipper with obstruc-
tions in the drum housing or discharge chute. This
damage is not covered under the chippers warranty
policy.
There are many factors contributing to discharge chute
clogging. Most of these factors are controllable through
proper maintenance and operator training.
Listed below are the most common problems associ-
ated with chute clogging and the suggested corrective
action.
Stringy Chip Discharge
• Dull or damaged blades. Change blades.
• Dull or damaged anvil. Change anvil.
• Incorrect anvil/blade clearance. Adjust to proper
gap.
• Improperly sharpened blades.
Poor Chip Discharge Velocity
Engine must operate at the maximum factory preset gov-
ernor speeds. During operation the engine speed must
not be permitted to drop more than 200 to 300 rpm. For
chippers not equipped with FeedSense®, engine speed
is controlled by using the control bar and through proper
brush preparation and feeding techniques.
A clogged, or partially clogged, discharge chute may also
cause poor chip discharge velocity. Make sure the chute
is clear of all obstructions.
Chipping Leafy or Wet Materials
Feed chipper slower than dry material and mix large
heavier limbs with leafy wet material to purge the drum
housing and discharge chute of smaller wet materials.
Drum Speed Slows But Engine rpm Remains High
• Make sure belts are properly adjusted and belt or
pulleys are not worn.
• Make sure the clutch is properly adjusted.
Summary of Contents for DRM 12
Page 3: ......
Page 7: ...2 Section 1 Introduction...
Page 17: ...12 Section 3 Safety Rear View Top View Bottom View 12 5 22 19 10 23 10 17 30 20 3 2 30...
Page 18: ...Section 3 Safety 13 4 8 7 2 3 970116658 1 6 5...
Page 19: ...14 Section 3 Safety 970116649 970116652 12 14 13 10 11 9...
Page 21: ...16 Section 3 Safety D G G D 25 26 24 27 23 22...
Page 22: ...Section 3 Safety 17 970137595 3X 30 31 28 29...
Page 23: ...18 Section 3 Safety...
Page 41: ...36 Section 6 Care of the Unit...
Page 62: ...Appendix...
Page 63: ......
Page 79: ...16 Appendix Glossary...
Page 83: ...Appendix Daily Preoperational Checklist...
Page 85: ...Appendix Preventive Maintenance and Inspection Checklist...
Page 88: ......
Page 89: ......
Page 91: ......
Page 93: ......
Page 96: ...07 13 970413443 A 2A PAGE 1 OF 2 ASSEMBLY FEED SYSTEM HYDRAULIC LIFT DRM 12...
Page 99: ...07 13 970413407 A 3A PAGE 1 OF 4 ASSEMBLY FEED CONTROL HYDRAULIC LIFT DRM 12...
Page 103: ...08 13 970485929 A 4A PAGE 1 OF 3 ASSEMBLY HAND CRANK CHUTE ROTATION DRUM CHIPPER...
Page 108: ...07 13 970413409 A 5A PAGE 1 OF 3 ASSEMBLY POWER SYSTEM KUBOTA 67 HP 74 HP 99 HP DIESEL DRM 12...
Page 113: ...07 13 970413438 A 6A PAGE 1 OF 4 FINAL ASSEMBLY DRM 12...
Page 117: ......
Page 118: ......
Page 119: ......
Page 120: ......
Page 121: ......
Page 122: ......
Page 123: ......
Page 124: ......
Page 125: ......
Page 127: ......
Page 128: ......
Page 129: ......
Page 138: ...79A PAGE 1 OF 3 05 13 970457633 A ASSEMBLY FUEL SYSTEM DRM12 CFD1217...