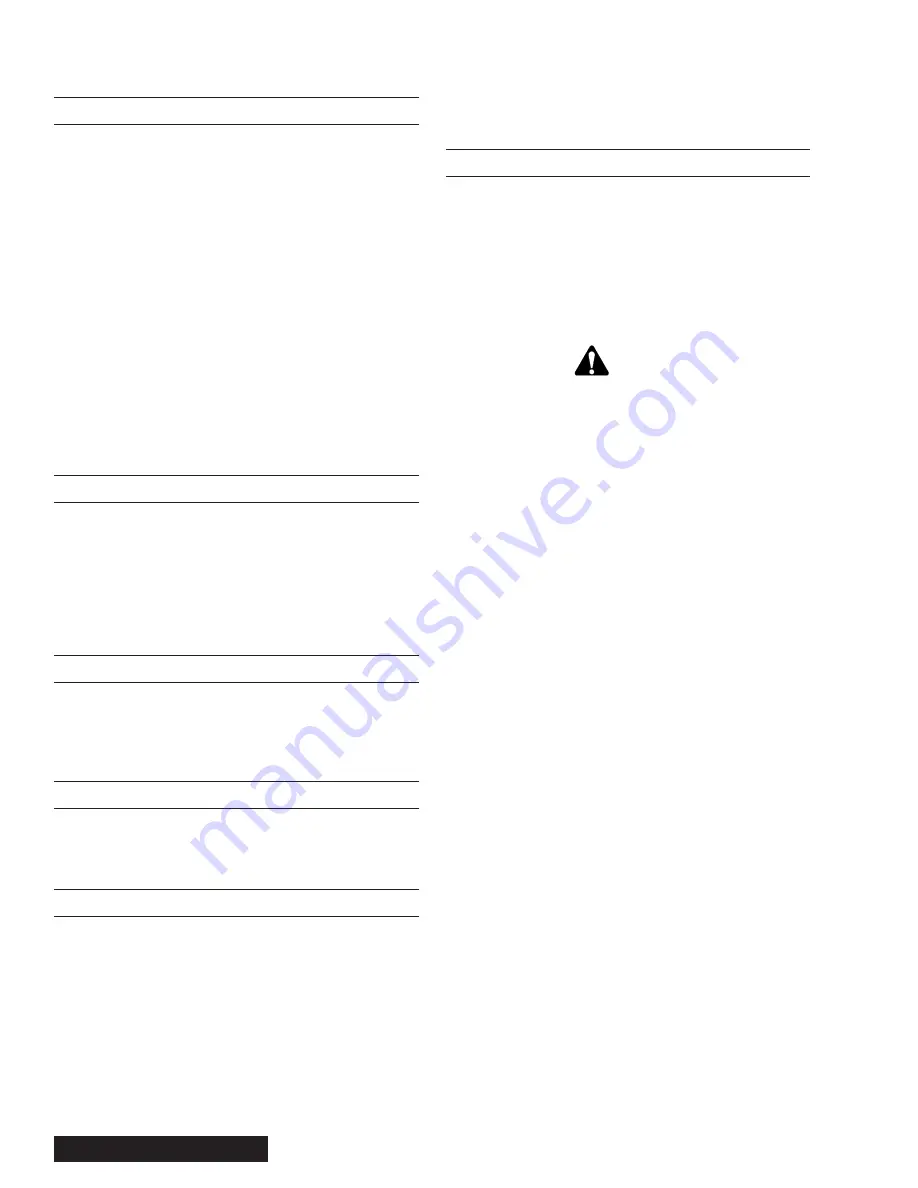
46 • Section 7 — Maintenance
System Operation
The chipper operates as an open center hydraulic system.
There is limited pressure in the system until the actuators
demand additional pressure. The system then responds
with a maximum of 2,900 psi (200 bar). Standard flow rate
is approximately 6.5 gpm (24.6 l/m). This may vary with
engine selection and customer drive speed specifications.
The normal flow of hydraulic fluid is from the pump to the
main control valve. The second spool from the right on
the main control valve routes the fluid through into the
two motors in either the forward or reverse direction. Fluid
then flows through the return filter and returns to the tank.
The first spool in the main control valve is for the panic
bar. This spool when activated routes all fluid directly
back to the return filter bypassing the directional valve.
It is used to stop feed roll motion in an emergency mode
of operation.
Oil Reservoir
The reservoir will hold 12 gallons (45.4 l). A 100 micron
suction filter is located at the outlet of the reservoir. A
breather is located on the side of the fill on the reser
-
voir. The breather contains a filter that cleans the air as
it enters the reservoir. The return filter is located under
the fill cap. When filling the reservoir remove the return
filter cartridge.
Oil Pump
The standard hydraulic pump used on DRM 12 is a 0.5
cubic inch (8.2 cc) per revolution displacement gear
pump. The pump is normally directly coupled to the
engine auxiliary drive.
Hydraulic Motors
Two motors drive and control the brush feeding rate to
the cutter. The motor tapered shafts are directly coupled
to the feed rolls.
Valves
When describing hydraulic valves, “position” identifies
the number of operating positions of the valve spool. A
two-position blocking valve has two operating positions,
open and closed.
The word “way” identifies the number of ports in a valve
section. A four-way control valve has four ports. One port
is for a pressure connection, one is for a return line con-
nection, and the other two ports are the working ports.
Leakage
If components and connections are installed properly,
leakage can be kept to a minimum. Small external leaks
are usually easy to find because dust will collect on the
hydraulic oil film.
External leakage is the escape of hydraulic oil outside
the hydraulic system. Improperly tightened fittings are a
primary cause of external leakage.
Warning
Death or serious injury can result from hydraulic
oil being injected into the flesh. Do not use hands
or other body parts to check hydraulic lines and fit
-
tings for leaks.
Seek immediate medical attention if injured by escap-
ing hydraulic oil. Serious infection or reaction can
result if medical treatment is not given immediately.
Spilled hydraulic oil creates slick surfaces and can
cause personnel to slip and/or fall. Keep the unit and
work areas clean.
If a connection is properly tightened but continues to
leak, disassemble the connection. Seal the necessary
parts and/or replace the defective part.
Worn or damaged parts such as scratched cylinder rods
can cause leaks. A worn or scratched output shaft on a
hydraulic motor can also cause a leak. Such conditions
must be repaired or replaced. A new seal should also
be installed.
Internal leaks allow pressurized hydraulic oil to escape
to tank or another hydraulic circuit. Most hydraulic com-
ponents have a small internal leak due to machining
tolerances.
An internal leak can cause a variety of problems in a
hydraulic system. An internal leak in a cylinder can cause
drifting or malfunction of a cylinder.
After extended hours of operation, hydraulic motors will
increase the internal leakage until a noticeable loss of
power is apparent. At this time, you must replace the
motor. To minimize motor wear it is essential to maintain
clean filtered oil in the system.
Summary of Contents for DRM 12
Page 3: ......
Page 7: ...2 Section 1 Introduction...
Page 17: ...12 Section 3 Safety Rear View Top View Bottom View 12 5 22 19 10 23 10 17 30 20 3 2 30...
Page 18: ...Section 3 Safety 13 4 8 7 2 3 970116658 1 6 5...
Page 19: ...14 Section 3 Safety 970116649 970116652 12 14 13 10 11 9...
Page 21: ...16 Section 3 Safety D G G D 25 26 24 27 23 22...
Page 22: ...Section 3 Safety 17 970137595 3X 30 31 28 29...
Page 23: ...18 Section 3 Safety...
Page 41: ...36 Section 6 Care of the Unit...
Page 62: ...Appendix...
Page 63: ......
Page 79: ...16 Appendix Glossary...
Page 83: ...Appendix Daily Preoperational Checklist...
Page 85: ...Appendix Preventive Maintenance and Inspection Checklist...
Page 88: ......
Page 89: ......
Page 91: ......
Page 93: ......
Page 96: ...07 13 970413443 A 2A PAGE 1 OF 2 ASSEMBLY FEED SYSTEM HYDRAULIC LIFT DRM 12...
Page 99: ...07 13 970413407 A 3A PAGE 1 OF 4 ASSEMBLY FEED CONTROL HYDRAULIC LIFT DRM 12...
Page 103: ...08 13 970485929 A 4A PAGE 1 OF 3 ASSEMBLY HAND CRANK CHUTE ROTATION DRUM CHIPPER...
Page 108: ...07 13 970413409 A 5A PAGE 1 OF 3 ASSEMBLY POWER SYSTEM KUBOTA 67 HP 74 HP 99 HP DIESEL DRM 12...
Page 113: ...07 13 970413438 A 6A PAGE 1 OF 4 FINAL ASSEMBLY DRM 12...
Page 117: ......
Page 118: ......
Page 119: ......
Page 120: ......
Page 121: ......
Page 122: ......
Page 123: ......
Page 124: ......
Page 125: ......
Page 127: ......
Page 128: ......
Page 129: ......
Page 138: ...79A PAGE 1 OF 3 05 13 970457633 A ASSEMBLY FUEL SYSTEM DRM12 CFD1217...