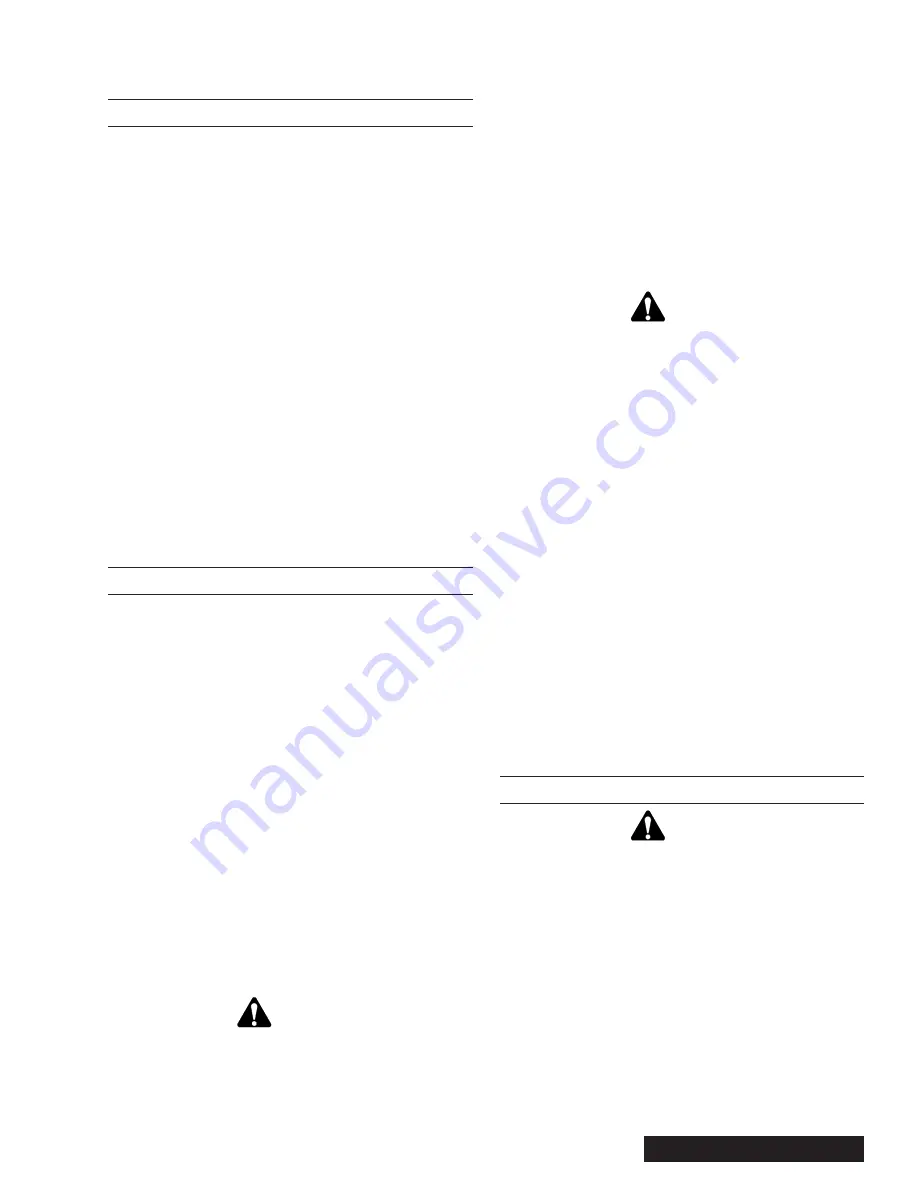
Section 7 — Maintenance • 47
Heat Generation
Heat is the result of pressurized fluid escaping to the
reservoir. Most hydraulic components have a small inter-
nal leak due to machining tolerances. This type of leak
generates a very small amount of heat that is taken into
account when the component is designed.
Internal leaks in the system may be caused by internal
housing cracks, bad relief valves, or leaking seals. This
type of leak allows a large volume of pressurized oil to
return to the reservoir, creating excessive heat in the
hydraulic system. Continuous operation with excessive
heat will damage the hydraulic oil, seals, and O-rings
throughout the system.
The following conditions cause heat generation.
• Excessive pump speed
• Worn or defective pump
• Defective or improperly adjusted relief
valve cartridges
• Low hydraulic oil level
• Improper hydraulic oil
• Internal component leakage
Hydraulic Lines
Hydraulic lines provide a passageway for fluid flow
between components in the hydraulic system. Fluid is
transmitted through the lines from the pump to the actua-
tor to operate the unit. A variety of lines may be used on
the unit depending on the specific application.
Most hoses have a lay line on them. The lay line contains
the following information.
• Manufacturer’s name
• Manufacturer’s part number
• SAE rating
• Burst pressure (sometimes)
• “Nonconductive” appears on nonconductive hoses
When replacing a hose, use one the same size, length,
and pressure rating. If hose size is doubled, four times
the amount of oil will flow at the same pressure. If hose
size is decreased, the flow in the circuit will decrease and
back pressure will increase. The increase in back pres-
sure will cause heat to build up and system malfunction.
Warning
Death or serious injury can result from hydraulic
oil being injected into the flesh when loosening or
disconnecting hydraulic components. Remove the
pressure before loosening or disconnecting hydraulic
components.
Seek immediate medical attention if injured by escap-
ing hydraulic oil. Serious infection or reaction can
result if medical treatment is not given immediately.
Spilled hydraulic oil creates slick surfaces and can
cause personnel to slip and/or fall. Keep the unit and
work areas clean.
Caution
Injury can result from airborne particles entering the
eyes and lungs. Wear appropriate safety equipment.
Injury can result from being pinched or trapped be-
tween moving components. Keep hands clear.
Use caution when access covers have been removed
to service the unit. Pinch points and shear points may
exist between moving parts. Replace the access covers
immediately after servicing.
Remove all fluid pressure from a hydraulic circuit before
disconnecting lines or fittings.
Mark all hydraulic line fittings before disconnecting them
to ease installation later. Place a container under the
hoses to catch the hydraulic oil. Cap or plug all open
ports, hoses, and fittings to prevent contamination.
Warranty will be denied on components returned to Altec if
ports are not plugged and cylinder rods are not retracted.
After completing a procedure, check the oil level in the
hydraulic oil reservoir and add oil if necessary.
Drive Belt/Pulleys
Caution
Injury can result from being pinched or trapped be-
tween moving components. Keep hands and body
parts clear.
Never place any part of the body in a potential pinch
point. This not only applies to the heads and chutes, but
also drum and engine sheave/belt contacts.
Disengage clutch and the hydraulic feed system. Remove
keys from the ignition switch and place in pocket. Lock
out chipper.
Drum and drive system continue to move after the clutch
has been disengaged and the engine has been cut off.
Summary of Contents for DRM 12
Page 3: ......
Page 7: ...2 Section 1 Introduction...
Page 17: ...12 Section 3 Safety Rear View Top View Bottom View 12 5 22 19 10 23 10 17 30 20 3 2 30...
Page 18: ...Section 3 Safety 13 4 8 7 2 3 970116658 1 6 5...
Page 19: ...14 Section 3 Safety 970116649 970116652 12 14 13 10 11 9...
Page 21: ...16 Section 3 Safety D G G D 25 26 24 27 23 22...
Page 22: ...Section 3 Safety 17 970137595 3X 30 31 28 29...
Page 23: ...18 Section 3 Safety...
Page 41: ...36 Section 6 Care of the Unit...
Page 62: ...Appendix...
Page 63: ......
Page 79: ...16 Appendix Glossary...
Page 83: ...Appendix Daily Preoperational Checklist...
Page 85: ...Appendix Preventive Maintenance and Inspection Checklist...
Page 88: ......
Page 89: ......
Page 91: ......
Page 93: ......
Page 96: ...07 13 970413443 A 2A PAGE 1 OF 2 ASSEMBLY FEED SYSTEM HYDRAULIC LIFT DRM 12...
Page 99: ...07 13 970413407 A 3A PAGE 1 OF 4 ASSEMBLY FEED CONTROL HYDRAULIC LIFT DRM 12...
Page 103: ...08 13 970485929 A 4A PAGE 1 OF 3 ASSEMBLY HAND CRANK CHUTE ROTATION DRUM CHIPPER...
Page 108: ...07 13 970413409 A 5A PAGE 1 OF 3 ASSEMBLY POWER SYSTEM KUBOTA 67 HP 74 HP 99 HP DIESEL DRM 12...
Page 113: ...07 13 970413438 A 6A PAGE 1 OF 4 FINAL ASSEMBLY DRM 12...
Page 117: ......
Page 118: ......
Page 119: ......
Page 120: ......
Page 121: ......
Page 122: ......
Page 123: ......
Page 124: ......
Page 125: ......
Page 127: ......
Page 128: ......
Page 129: ......
Page 138: ...79A PAGE 1 OF 3 05 13 970457633 A ASSEMBLY FUEL SYSTEM DRM12 CFD1217...