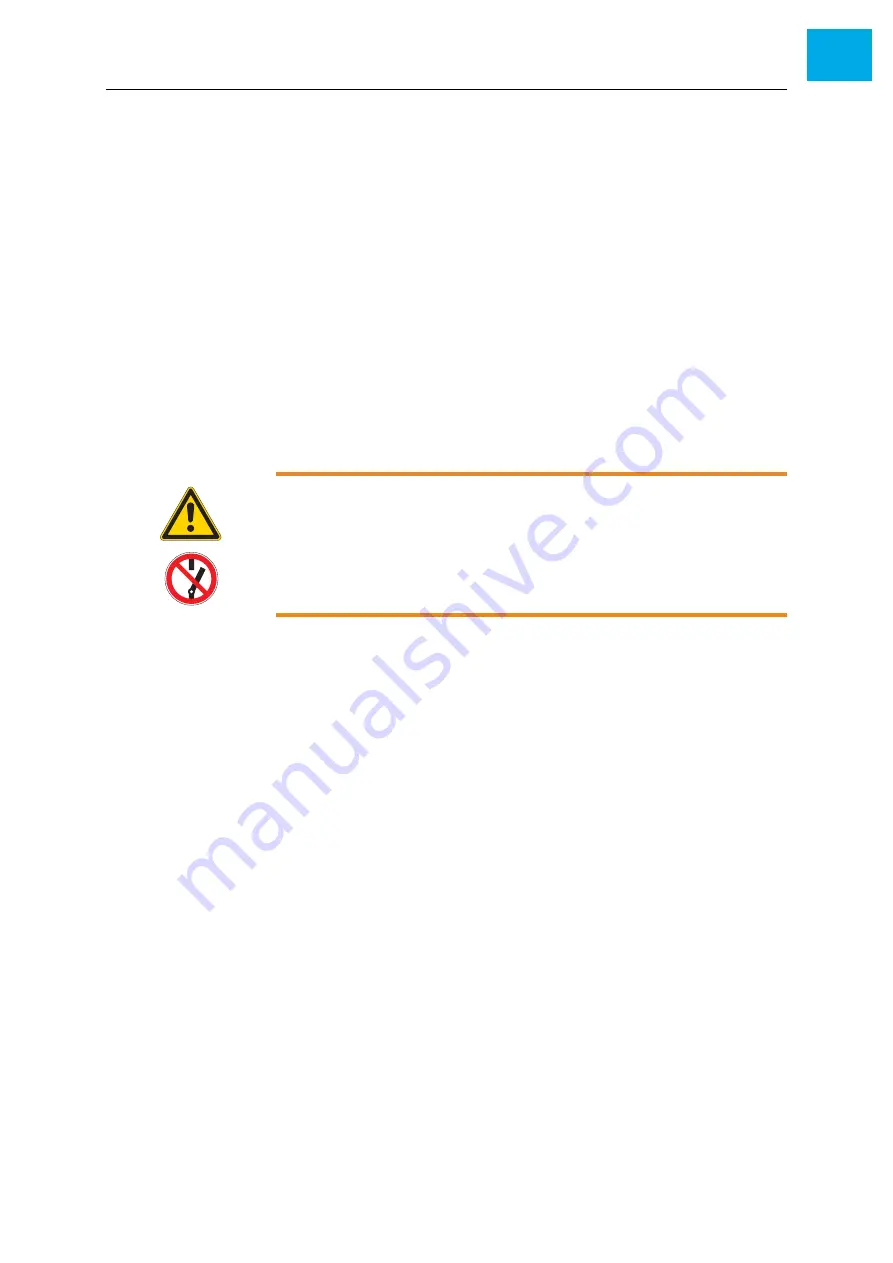
AIXTRON
- Dokumentation
CONFIDENTIAL
41
2
cr
ius_I
I_e
n_
00,
Ed
it
io
n
06/
201
0
System Manual
Safety
CRIUS II
Lockout/tagout procedure
2.7.2
What to do if a device cannot be locked
Sometimes an energy-isolating device cannot be locked with a padlock. In this
case, you may apply a lockable plastic cover which encloses the energy-iso-
lating device and renders it inoperative. A wide range of these lockout devices
is available commercially, such as:
•
Circuit breaker lockouts
•
Electrical plug lockouts
•
Ball valve lockouts
•
Gate valve lockouts
Instead of locking a particular switch or valve inside of a cabinet, you may lock
and tag the entire cabinet instead. If you have any questions concerning lock-
out/tagout, refer to the safety department of your company.
2.7.3
Removing lockout/tagout devices
Proceed as follows to remove lockout/tagout devices:
1
Inspect the component to ensure that it is operationally intact and that
nonessential items are removed from the area
2
Make sure that everyone is positioned safely and away from the com-
ponent
3
Remove the lockout/tagout devices
4
Make sure that all employees who work with the system know that the
lockout/tagout devices have been removed and that the component will
be energized
5
Energize the component
WARNING!
Lockouts and tagouts.
Personnel who work on de-energized components may be seriously
injured or killed if someone removes lockout/tagout devices and re-ener-
gizes the component without their knowledge.
Respect lockout and tagout devices! Locks and tags must not be
removed by anyone except the person who attached them.