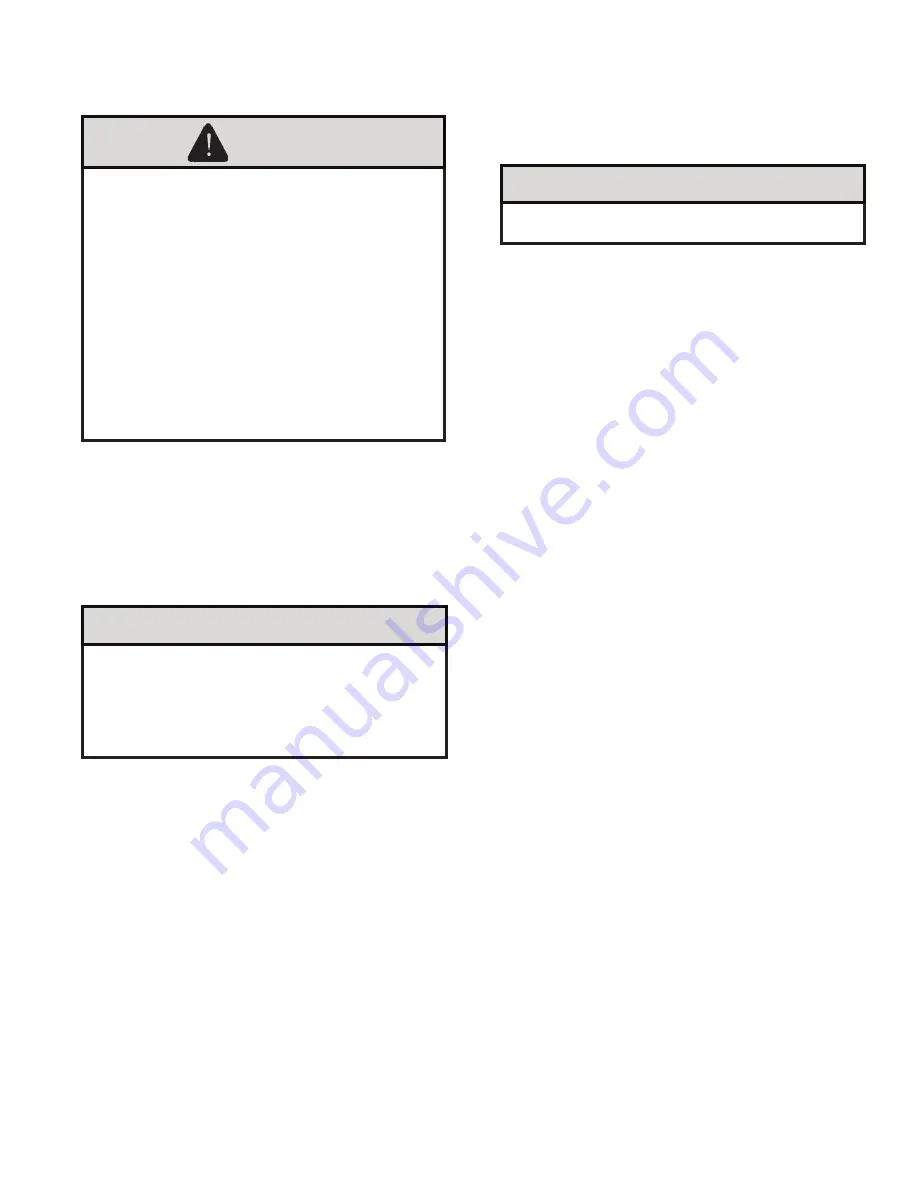
31
IV. Venting
D. Stainless Steel Venting (continued)
3. System Assembly
WARNING
Asphyxiation Hazard. Vent systems made
by Heat Fab, M&G / DuraVent and Z-Flex rely
on gaskets for proper sealing. When these
vent systems are used, take the following
precautions:
• Make sure that gasket is in position and
undamaged in the female end of the pipe.
• Make sure that both the male and female
pipes are free of damage prior to assembly.
• Only cut vent pipe as permitted by the
vent manufacturer in accordance with their
Instructions. When pipe is cut, cut end must
be square and carefully de-burred prior to
assembly.
a. Plan venting system to avoid possible contact
with plumbing or electrical wires. Start at
vent connector at boiler and work towards vent
termination.
b. Follow all manufacturer instructions and
warnings when preparing pipe ends for joining
and when assembling the vent/combustion air
system.
NOTICE
The venting system must be free to expand
and contract and supported in accordance
with installation instructions included by the
original stainless steel venting component
manufacturers, Heat Fab, M&G / DuraVent or
Z-Flex, whichever applicable.
c. On horizontal pipe sections, orient all welded
seams at the 12:00 position. Do not place
longitudinal welded seams at the bottom of
horizontal sections of vent pipe.
d. Assemble the combustion air system using either
galvanized or PVC pipe.
i.
If PVC piping is used, use PVC cement
to assemble the PVC intake system
components. See “B. CPVC/PVC Venting”
for combustion air pipe installation
instructions.
ii.
If galvanized piping is used, use at least two
sheet metal screws per joint. Seal outside of
all joints
4. Horizontal Sidewall Vent Termination
a. Standard Two-Pipe Termination
See Figures 5A and 5B.
i.
Vent Termination
• Use a stainless steel tee in the upright
position.
NOTICE
The joint between the terminal and the last piece
of pipe must be outside of the building.
• Male end of terminal will fit into female
end of any of the listed stainless vent
systems.
• Apply a heavy bead of silicone to the
male end of the terminal before inserting
it into the last piece of pipe. Orient the
terminal so that the seam in the terminal
is at 12:00.
• Smooth the silicone over the seam
between the terminal and the last piece
of pipe, applying additional silicone if
necessary to ensure a tight seal.
• Allow the silicone to cure per the silicone
manufacturer’s instructions before
operating the boiler.
ii.
Combustion Air Termination
• Use a tee in the upright position. Tee
should protrude the same distance from
the wall as the exhaust terminal as shown
in Figure 5A.
• Install a rodent screen (not supplied) in
the inlet terminal. Use a screen having
1/2 in. x 1/2 in. (13 mm x 13 mm) mesh.
b. Optional Two-Pipe Snorkel Termination
See Figures 6A and 6B.
This installation will allow a maximum of
7 ft. (2.1 m) vertical exterior run of the vent/
combustion air piping to be installed on the
approved AL29-4C stainless steel horizontal
venting application.
i.
Vent Termination
• After penetrating wall, install the
appropriate manufacturer’s 90° elbow so
that the elbow leg is in the up direction.
• Install maximum vertical run of 7 ft.
(2.1 m) of appropriate manufacturer’s
vent pipe as shown in Figure 6A.
• At top of vent pipe length install another
appropriate manufacturer’s 90° elbow
so that the elbow leg is opposite the
building’s exterior surface.
• Install horizontal vent terminal.
• Brace exterior piping if required.
Summary of Contents for APEX
Page 57: ...57 VIII Electrical continued Figure 26 Ladder Diagram ...
Page 58: ...58 VIII Electrical continued ...
Page 59: ...59 Figure 27 Wiring Connections Diagram VIII Electrical continued ...
Page 105: ...105 ...
Page 109: ...109 XIII Repair Parts continued APX625 APX725 and APX825 APX825 shown ...
Page 112: ...112 XIII Repair Parts continued APX425 and APX525 ...
Page 114: ...114 XIII Repair Parts continued APX625 APX725 and APX825 ...
Page 122: ...122 ...
Page 123: ...123 ...