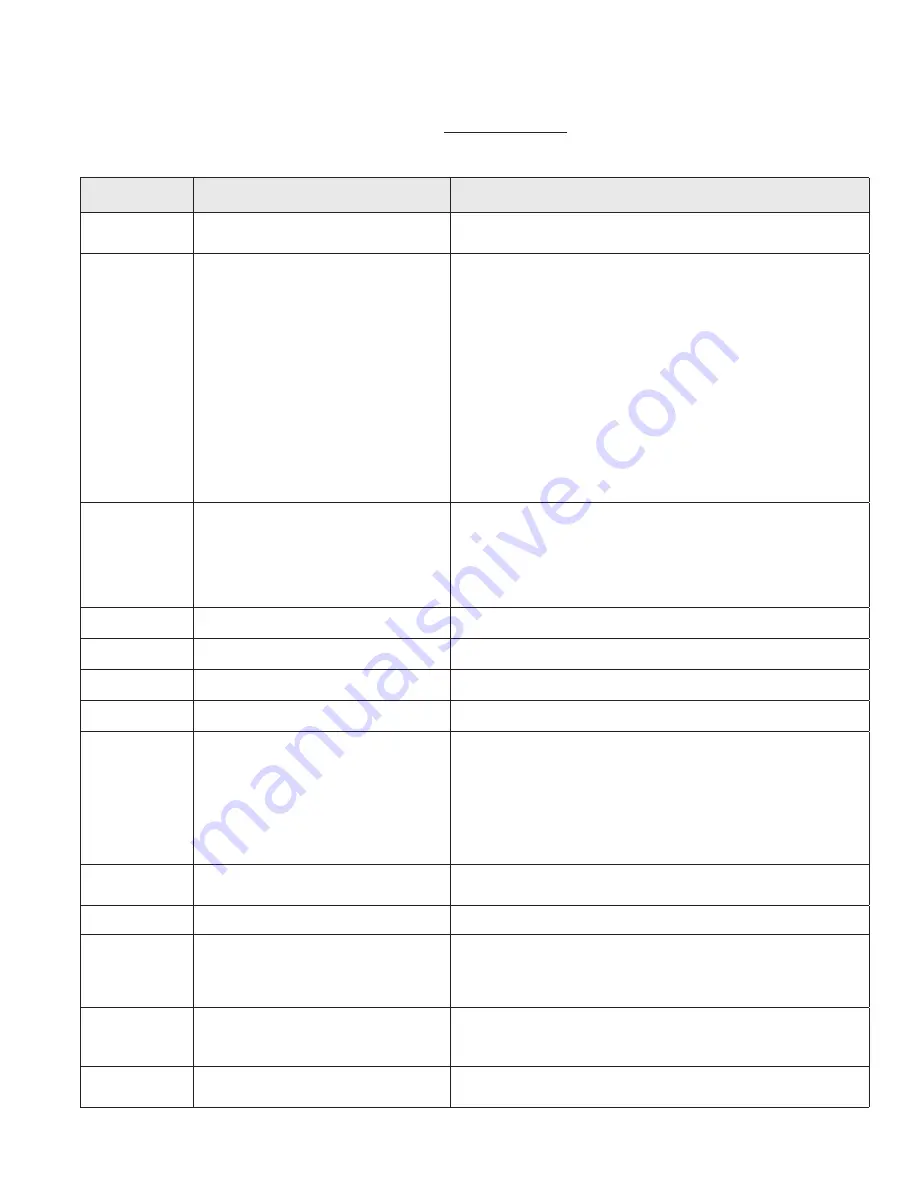
103
XII. Troubleshooting
(continued)
F. Troubleshooting problems where a Soft Lockout Code is displayed.
When a soft lockout occurs, the
boiler will shut down, the display will turn red and the “Help” button will “blink”. Select the “blinking” “Help” button to
determine the cause of the soft lockout. The boiler will automatically restart once the condition that caused the lockout is
corrected.
Soft Lockout Codes Displayed
Lockout
Number
Condition
Possible Cause
1
Anti Short Cycle
Minimum time between starts has not been reached.
Normal delay used to avoid excessive cycles.
2
Boiler Safety Limit
Open
Boiler Safety Limit wired to terminals J6-1, 2 or 3
OPEN:
• Condensate Trap Float Switch
contact open.
• Thermal Link Switch contact open.
• Burner Door Thermostat with manual reset
contact open.
• Air Pressure Switch contact open.
• Auto Reset High Limit contact open.
• Loose wiring to limit device.
• Auto Reset Supply high limit sensor detected temperature in excess of 200°F.
• Defective Auto Reset Supply High Limit Switch.
• Plugged Condensate Trap - also check to ensure boiler is level.
•
Thermal Link Switch blown due to temperature rise above 604°F (318°C).
•
Burner Door Thermostat with manual reset contact open due to temperature rise
above 500°F (260°C) - check the cause of overheating (burner door insulation, loose
mounting, etc.).
• Air Pressure Switch contact open - check for blocked vent.
• See possible causes for “Hard Lockout 4”.
NOTE
Block Vent Special Note
Before a call for heat the air pressure switch is closed. When there is a call for heat
with a blocked vent the air pressure switch will open (due to excessive pressure of the
blower against a blocked flue pipe) after the blower starts. The control stops the start
sequence and stops the blower. After the blower stops the pressure switch re-closes
and the cycle continues. The displays shows the cause of trip for only the time the
pressure switch is open.
3
Boiler Safety Limit
Open
Boiler Safety Limit, or External Limit wired to
terminals J5-1 OPEN:
• Jumper for External Limit wired to terminals 11
and 12 or device connected to it open.
• Jumper for Flow Switch or device connected to
it open.
• Jumper for Low Gas Pressure Switch or device
connected to it open.
•
See possible causes for “Hard Lockout 4”.
•
Loose wiring to limit device.
•
External Limit defective or jumper not installed.
•
Low Gas Pressure Switch contact open (if installed).
•
Flow switch not installed and jumper missing.
•
No flow or insufficient flow through boiler loop or flow switch defective.
•
If neither yellow or green light is on, check LWCO harness.
7
Return sensor fault
Shorted or open return temperature sensor.
•
Shorted or mis-wired return sensor wiring.
•
Defective return sensor.
8
Supply sensor fault
Shorted or open supply temperature sensor.
•
Shorted or mis-wired supply sensor wiring.
•
Defective supply sensor.
9
DHW sensor fault
Shorted or open Domestic Hot Water (DHW)
temperature sensor.
•
Shorted or mis-wired DHW sensor wiring.
•
Defective DHW sensor.
10
Stack sensor fault
Shorted or open flue gas (stack) temperature sensor.
•
Shorted or mis-wired stack sensor wiring.
•
Defective stack sensor.
11
Ignition failure
Model APX425 flame failure after 5 tries to restart.
•
No gas pressure.
•
Gas pressure under minimum value shown on rating plate.
•
Gas line not completely purged of air.
•
Defective Electrode.
•
Loose burner ground connection.
•
Defective Ignition Cable.
•
Defective gas valve (check for 24 Vac at harness during trial for ignition before
replacing valve).
•
Air-fuel mixture out of adjustment - consult factory.
13
Flame rod
shorted to ground
Flame rod shorted to ground
•
Shorted or mis-wired flame rode wiring.
•
Defective flame rod.
14
ΔT
inlet/outlet high
Temperature rise between supply and return is too
high.
•
Inadequate boiler water flow. Verify that circulator is operating and that circulator
and piping are sized per Section VI of this manual.
15
Return temp higher
than supply
The Control is reading a return sensor temperature
higher than the supply sensor temperature. Condition
must be present for at least 75 seconds for this error
code to appear.
•
Flow through boiler reversed. Verify correct piping and circulator orientation.
•
No boiler water flow. Verify that system is purged of air and that appropriate valves
are open.
•
Sensor wiring reversed.
•
Supply or return sensor defective.
16
Supply temp has risen
too quickly
Supply water temperature has risen too quickly.
•
See possible causes for “Hard Lockout 4”.
•
Inadequate boiler water flow.
•
Verify that circulator is operating and that circulator and piping are sized per
Section VI of this manual.
17
Blower speed not
proved
Normal waiting for blower speed to match purge and
light-off setpoint.
Summary of Contents for APEX
Page 57: ...57 VIII Electrical continued Figure 26 Ladder Diagram ...
Page 58: ...58 VIII Electrical continued ...
Page 59: ...59 Figure 27 Wiring Connections Diagram VIII Electrical continued ...
Page 105: ...105 ...
Page 109: ...109 XIII Repair Parts continued APX625 APX725 and APX825 APX825 shown ...
Page 112: ...112 XIII Repair Parts continued APX425 and APX525 ...
Page 114: ...114 XIII Repair Parts continued APX625 APX725 and APX825 ...
Page 122: ...122 ...
Page 123: ...123 ...