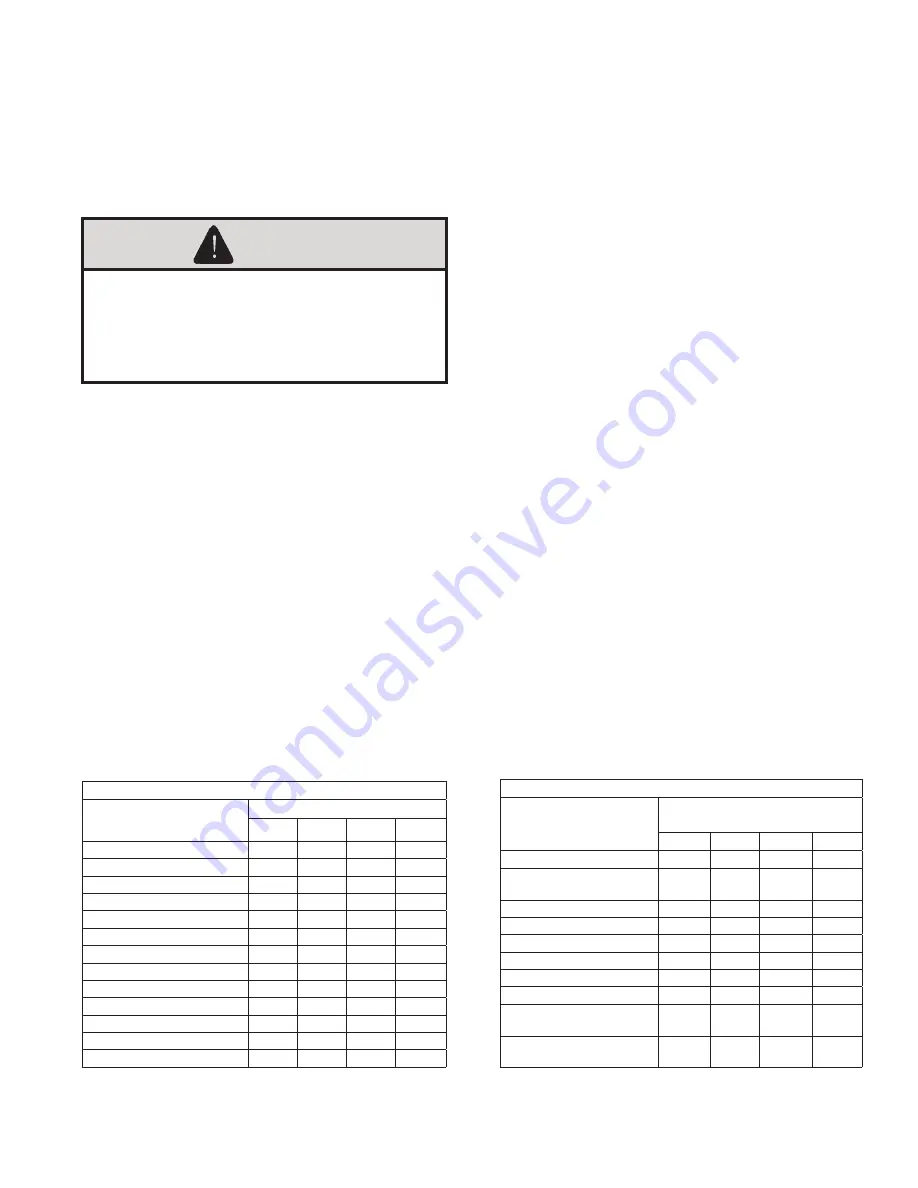
43
VI. Water Piping and Trim
C. Standard Installation Requirements (continued)
The end of the discharge pipe must terminate in an
unthreaded pipe. If the safety relief valve is not
piped to a drain, it must terminate at least 6 in. (150
mm) above the floor. Do not run safety relief valve
discharge piping through an area prone to freezing.
The termination of discharge piping must be in an
area where it will not become plugged by debris.
CAUTION
Burn Hazard. Safety relief valve discharge
piping must be piped such that the potential of
severe burns is eliminated. DO NOT pipe in any
area where freezing could occur. DO NOT install
any shut-off valves, plugs or caps. Consult local
codes for proper discharge piping arrangement.
2. Flow Switch (Required)
– A flow switch is
required in lieu of manual reset low water cutoff
(LWCO) for forced circulation coil-type water
boilers to prevent overheating and heat exchanger
failure in accordance with requirements of ASME
Boiler and Pressure Vessel Code, Section IV, and
ANSI/ASME CSD-1 – latest edition, “Controls and
Safety Devices for Automatically Fired Boilers”.
The flow switch is factory provided. Follow Section
VI, Paragraph A and Section VIII ‘Electrical’ of
these instructions to install and wire the flow switch.
3. Circulator (Required)
– Usually at least two
circulators will be required to properly install an
Apex boiler. See Paragraph B above for information
on sizing the circulators.
4. Expansion Tank (Required)
– If this boiler is
replacing an existing boiler with no other changes
in the system, the old expansion tank can generally
Table 14: Fitting and Valve Equivalent Length
Copper Fitting and Sweat Valve Equivalent Length (Ft)
Fitting or Valve
Description
Copper Pipe or Valve Size
1
1¼
1½
2
90° Elbow
2.5
3.0
4.0
5.5
45° Elbow
1.0
1.2
1.5
2.0
Tee (through flow)
0.5
0.6
0.8
1.0
Tee (Branch flow)
4.5
5.5
7.0
9.0
Diverter Tee (typical)
23.5
25.0
23.0
23.0
Gate Valve
0.3
0.4
0.5
0.7
Globe Valve
25.0
36.0
46.0
56.0
Angle Valve
5.3
7.8
9.4
12.5
Ball Valve (standard port)
4.3
7.0
6.6
14.0
Ball Valve (full port)
1.9
1.4
2.2
1.3
Swing Check Valve
4.5
5.5
6.5
9.0
Flow-Check Valve (typical)
54.0
74.0
57.0
177.0
Butterfly Valve
2.7
2.0
2.7
4.5
Threaded Fitting and Valve Equivalent Length (Ft)
Fitting or Valve
Description
Black Threaded Pipe or
Valve Size
1
1¼
1½
2
90° Elbow
2.6
3.5
4.0
5.2
Long Radius
Elbow (45° or 90°)
1.4
1.8
2.2
2.8
Tee (through flow)
1.8
2.3
2.7
3.5
Tee (Branch flow)
5.3
6.9
8.1
10.0
Close Return Bend
4.4
5.8
6.7
8.6
Gate Valve (full open)
0.7
0.9
1.1
1.4
Globe Valve (full open)
30.0
39.0
46.0
59.0
Angle Valve (full open)
13.0
17.0
20.0
26.0
Swing Check Valve
(full open)
8.7
12.0
13.0
17.0
Flow-Check Valve
(typical)
42.0
60.0
63.0
83.0
Table 14: Fitting and Valve Equivalent Length
(cont’d)
NOTE: Table 14 is provided as reference to assist in piping design and specifies equivalent length of typical piping
fittings and valves.
be reused. If the expansion tank must be replaced,
consult the expansion tank manufacturer’s literature
for proper sizing.
5. Fill Valve (Required)
– Either manual
(recommended) or automatic fill valve may be used.
However, if automatic refill is employed, a water
meter must be added to evaluate the makeup water
volume taken after initial fill and eliminate any
water leakage as early as possible.
6. Automatic Air Vent (Required)
–At least one
automatic air vent is required. Manual vents will
usually be required in other parts of the system to
remove air during initial fill.
7. Manual Reset High Limit (Required by some
Codes)
- This control is required by ASME CSD-1
and some other codes. Install the high limit in the
boiler supply piping just above the boiler with no
intervening valves. Set the manual reset high limit
to 210°F. Follow Section VIII “Electrical” to wire
the high limit.
8. Y-strainer (Recommended)
– A Y-strainer
or equivalent strainer removes heating system
debris from hydronic systems and protects boiler
heat exchanger from fouling. Install the strainer
downstream of full port isolation valve at the inlet
side of the circulator for easy service.
9. Flow Control Valve (Strongly
Recommended)
– The flow control valve prevents
flow through the system unless the circulator is
operating. Flow control valves are used to prevent
gravity circulation or “ghost flows” in circulator
zone systems through zones that are not calling for
heat.
Summary of Contents for APEX
Page 57: ...57 VIII Electrical continued Figure 26 Ladder Diagram ...
Page 58: ...58 VIII Electrical continued ...
Page 59: ...59 Figure 27 Wiring Connections Diagram VIII Electrical continued ...
Page 105: ...105 ...
Page 109: ...109 XIII Repair Parts continued APX625 APX725 and APX825 APX825 shown ...
Page 112: ...112 XIII Repair Parts continued APX425 and APX525 ...
Page 114: ...114 XIII Repair Parts continued APX625 APX725 and APX825 ...
Page 122: ...122 ...
Page 123: ...123 ...