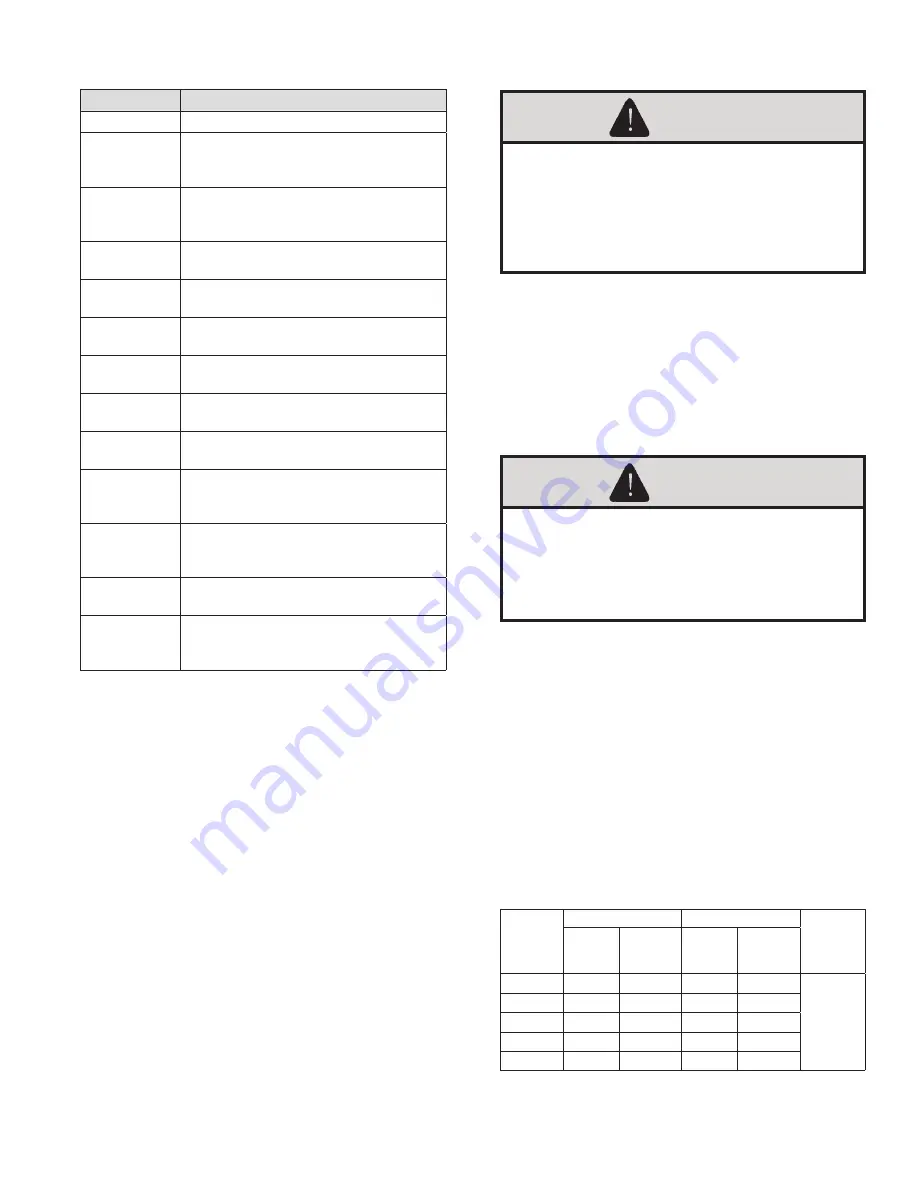
69
it may take several tries for ignition before a flame is
established. If more than 2 tries for ignition are needed,
it will be necessary to press the reset button to restart
the boiler. Once a flame has been established for the
first time, subsequent calls for burner operation should
result in a flame on the first try.
I. Check Burner Flame
Inspect the flame visible through the window. On high
fire the flame should be stable and mostly blue (Figure
35). No yellow tipping should be present; however,
intermittent flecks of yellow and orange in the flame are
normal.
J. Check Gas Inlet Pressure
Check the inlet pressure and adjust if necessary. Verify
that the inlet pressure is between the upper and lower
limits shown on the rating plate with all gas appliances
on and off.
WARNING
Asphyxiation Hazard. The outlet pressure for
the gas valve has been factory set and requires
no field adjustment. This setting is satisfactory
for both natural gas and propane. Attempting to
adjust the outlet pressure may result in damage
to the gas valve and cause property damage,
personal injury or loss of life.
K. Models APX425 and APX525 only:
For LP
Gas, perform procedure as described in Paragraph R
“Field Conversion From Natural Gas to LP Gas” before
starting Paragraph L “Checking/Adjusting Gas Input
Rate”.
For natural gas, proceed to Paragraph L “Perform
Combustion Test”.
L. Perform Combustion Test
WARNING
Asphyxiation Hazard. Each Apex Series boiler
is tested at the factory and adjustments to the
air fuel mixture are normally not necessary.
Improper gas valve or mixture adjustments could
result in property damage, personal injury or
loss of life.
1. Remove flue temperature sensor
from vent
connector (see Figure 9 on page 22) and insert
combustion analyzer probe through flue temperature
sensor silicon cap opening. If required, also remove
the flue temperature sensor silicon cap and insert
the analyzer probe directly into flue sensor port.
Reinstall the sensor and the cap upon combustion
testing completion.
2. Verify O
2
(or CO
2
) and CO are within limits
specified in Table 21 (natural gas) or Table 22 (LP
gas) at both high and low fire as described in the
following steps.
IX. System Start-up
(continued)
Status
Control Action
Initiate
Power-up
Standby Delay
This state is entered when a delay is
needed before allowing the burner control
to be available and for sensor errors.
Standby
Boiler is not firing. There is no call for
heat or there is a call for heat and the
temperature is greater than setpoint.
Safe Startup
Tests flame circuit then checks for flame
signal.
Drive Purge
Driving blower to purge rate setting and
waiting for the proper fan feedback.
Prepurge
Purges the combustion chamber for the
10 second purge time.
Drive Light-off Driving blower to light-off rate setting and
waiting for the proper fan feedback.
Pre-ignition
Test
Tests the safety relay and verifies that
downstream contacts are off.
Pre-ignition
Energizes the igniter and checks for
flame.
Direct
Ignition
Opens main fuel valve and attempts
to ignite the main fuel directly from the
ignition source.
Running
Normal boiler operation. Modulation rate
depends on temperature and setpoint
selections and modulating control action.
Postpurge
Purges the combustion chamber for the
30 second purge time.
Lockout
Prevents system from running due to a
detected problem and records fault in
Lockout History.
Boiler
Model
High Fire
Low Fire
CO,
PPM
% CO
2
% O
2
% CO
2
% O
2
APX425 9.9 - 8.2 3.5 - 6.5 9.3 - 7.9 4.5 - 7.0
Less than
100 PPM
APX525 9.3 - 7.9 4.5 - 7.0 9.3 - 7.9 4.5 - 7.0
APX625 9.1 - 8.5 4.9 - 6.0 9.1 - 7.5 4.9 - 7.7
APX725 8.7 - 8.3 5.6 - 6.3 8.7 - 7.5 5.6 - 7.7
APX825 9.3 - 7.9 4.5 - 7.0 9.3 - 7.9 4.5 - 7.0
Table 21: Typical Combustion Settings,
Natural Gas
Summary of Contents for APEX
Page 57: ...57 VIII Electrical continued Figure 26 Ladder Diagram ...
Page 58: ...58 VIII Electrical continued ...
Page 59: ...59 Figure 27 Wiring Connections Diagram VIII Electrical continued ...
Page 105: ...105 ...
Page 109: ...109 XIII Repair Parts continued APX625 APX725 and APX825 APX825 shown ...
Page 112: ...112 XIII Repair Parts continued APX425 and APX525 ...
Page 114: ...114 XIII Repair Parts continued APX625 APX725 and APX825 ...
Page 122: ...122 ...
Page 123: ...123 ...