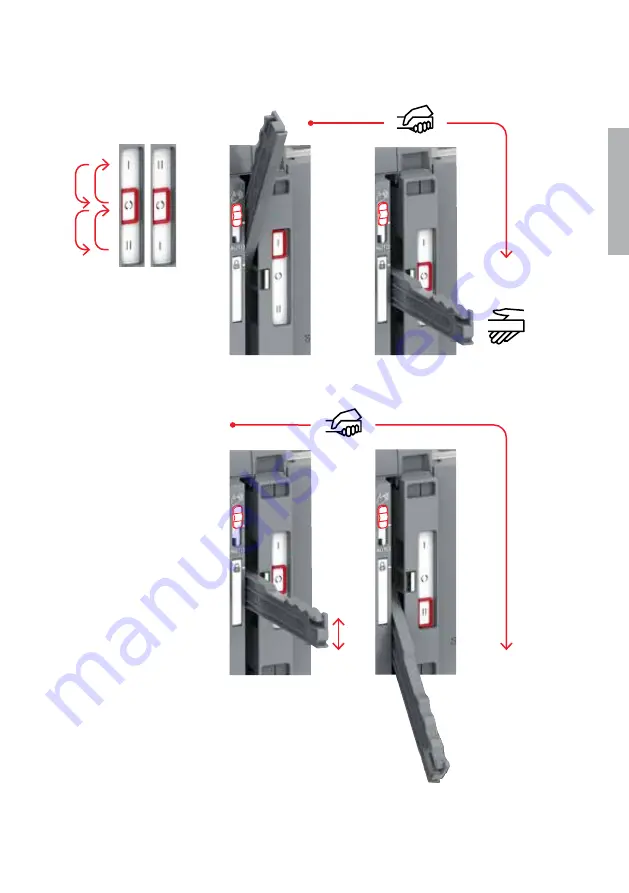
33
3 4 OX _ 3 0 -16 0 0 rev. B / 1 S CC 3 0 3 01 1 M 0 2 01
1
—
Fig. 3.4 Manual mode, operating by handle,
delayed transition I - O - II or II - O - I. To move
from position I to II (or II to I), move handle to
O position and release hand from handle.
I-position
O-position
OXB_B: I - O - II
OXB_T: II - O - I
O-position
II-position
Summary of Contents for TruONE ATS
Page 2: ......
Page 6: ...6 TruONE ATS INSTALL ATION AND OPER ATING INSTRUCTION 1 ...
Page 151: ... Notes ...
Page 152: ... Notes ...
Page 153: ... Notes ...
Page 154: ... Notes ...
Page 155: ... Notes ...
Page 156: ... Notes ...
Page 157: ... Notes ...
Page 159: ......