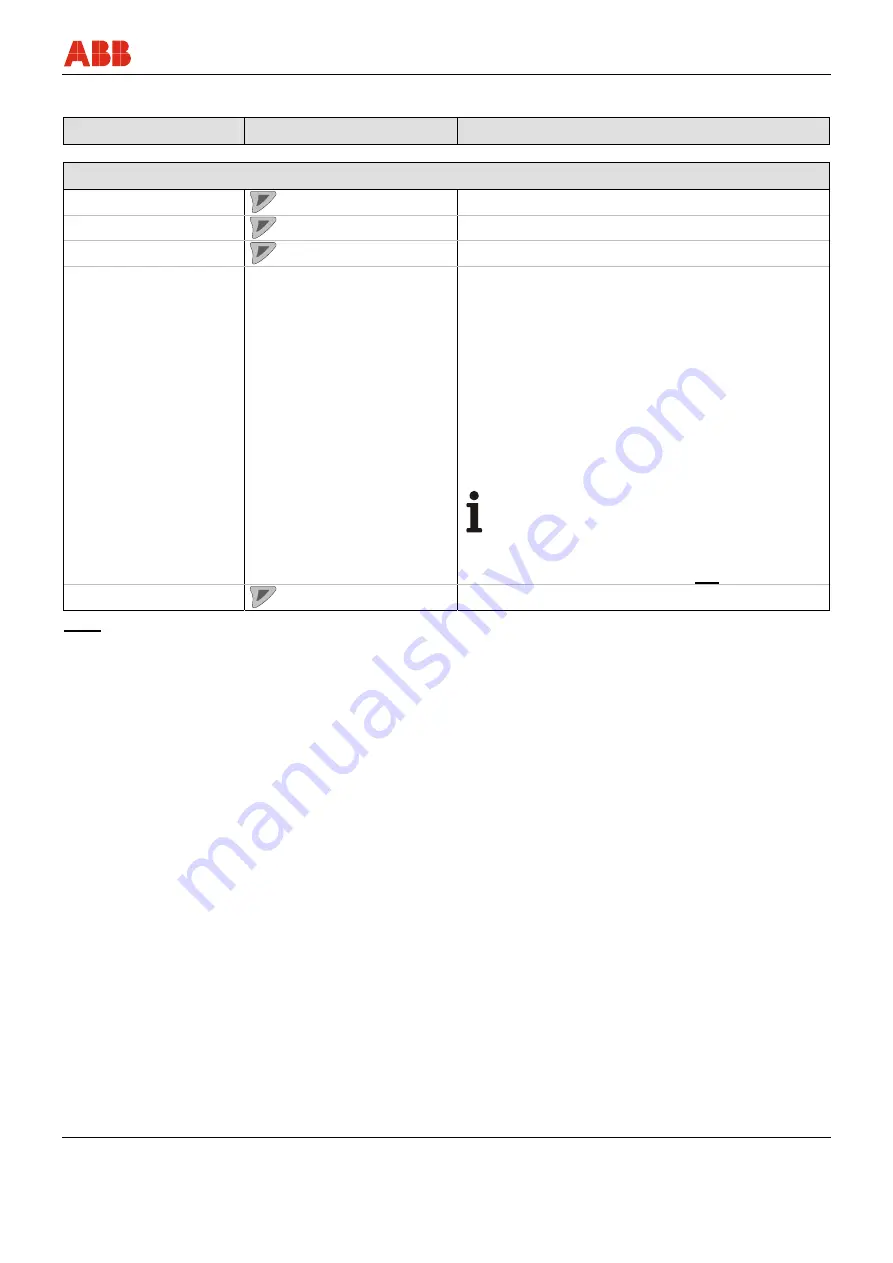
Parameterization
OI/FEX300/FEX500-EN FEX300,
FEX500
103
7.4.5 Menu: Input / Output
Menu / Parameter
Value range
Description
Input/Output
Digital Out Mode
Select the "Digital Output Mode" submenu.
Logic Setup
Select the "Logic Setup" submenu.
Pulse Setup
Select the "Pulse Setup" submenu.
Digital Input Setup
No Function, Totalizer
Reset(All), Flowrate to Zero,
System Zero Adjust, Totalizer
Stop(All), Dual Range,
Start/Stop Batching 1)
Select the operating mode for the digital output. There
are four operating modes available:
• Totalizer reset for all totalizers (forward, reverse
and differential totalizers)
• Ext. zero return
• External adjustment of zero point
• External totalizer stop for all totalizers (forward,
reverse and differential totalizers).
• Switchover between flow ranges 1 and 2 (Qmax
and Qmax 2)
• Start / stop of the fill function (batch)
1)
.
Default setting: external switch-off
Important (Notice)
If the fill operation is stopped before the
configured fill quantity is reached, the fill totalizer
is set to zero. When the fill function is restarted,
the interrupted fill operation is
not
continued.
Current Output
Select the "Current Output" submenu.
italics
= Parameter can only be viewed at the "Advanced" password level.
1) Parameter / menu only available for FEP500 / FEH500.
Summary of Contents for FEX300
Page 169: ...Appendix OI FEX300 FEX500 EN FEX300 FEX500 169...
Page 170: ...Appendix 170 FEX300 FEX500 OI FEX300 FEX500 EN...
Page 175: ......