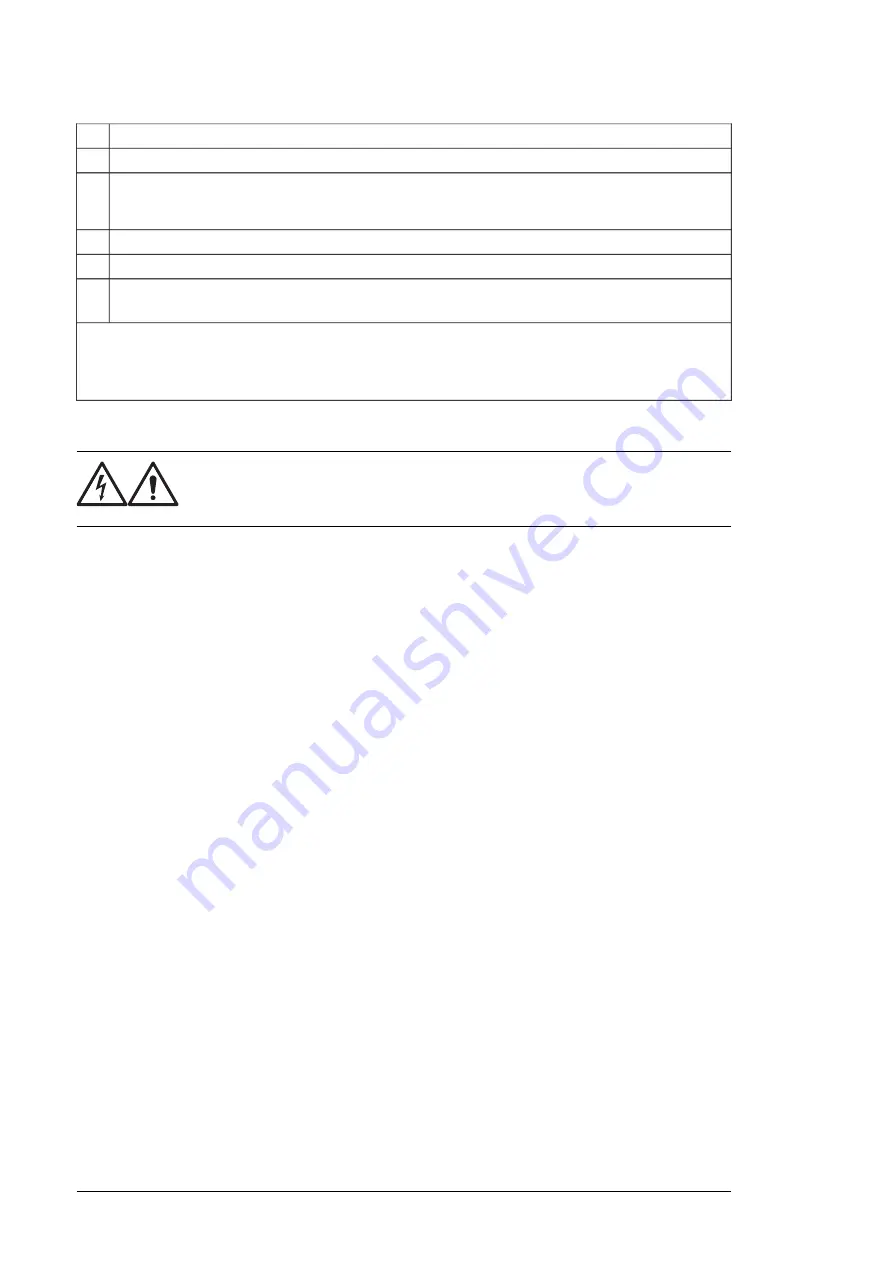
Input and output power cabling panels (H381)
4
ABB recommends 360-degree grounding at the enclosure entry
5
Use a separate grounding cable if the conductivity of the cable shield is < 50% of the conductivity of the
phase conductor and there is no symmetrically constructed grounding conductor in the cable (see section
6
Common mode filter (option)
7
d
u
/d
t
filter (option)
8
The drive module frame must be connected to the enclosure frame. See
and section
Grounding the drive module and the LCL filter module (page 73)
.
9
Note:
If there is a symmetrically constructed grounding conductor in the motor cable in addition to the conductive
shield, connect the grounding conductor to the grounding terminal at the drive and motor ends.
Do not use an asymmetrically constructed motor cable. Connecting its fourth conductor at the motor end in-
creases bearing currents and causes extra wear.
■
Power cable connection procedure
WARNING!
Obey the safety instructions of the drive. If you ignore them, injury or death,
or damage to the equipment can occur.
1. Run the motor cables from the motor to the enclosure. Ground the cable shields 360°
at the entry plate.
2. Twist the cable shields of the motor cables into bundles and connect them and any
separate ground conductors or cables to the ground busbar of the output power cabling
panel.
3. Connect the phase conductors of the motor cables to terminals T1/U2, T2/V2 and T3/W2
of the output cabling panel. For the tightening torques, see Technical data.
4. Make sure that all power is disconnected and reconnection is not possible. Use proper
safe disconnect procedures according to local codes.
5. Twist the cable shields of the input cables into bundles and connect them and any
separate ground conductors or cables to grounding busbar of the input cabling panel.
6. Connect the phase conductors of the input cables to terminals L1/U1, L2/V1 and L3/W1
of the input cabling panel. For the tightening torques, see Technical data.
144 Installation example with full cabling panels (H381)
Summary of Contents for ACS880-14
Page 1: ...ABB INDUSTRIAL DRIVES ACS880 14 drive modules 132 400 kW 200 400 hp Hardware manual...
Page 2: ......
Page 4: ......
Page 14: ...14...
Page 24: ...24...
Page 30: ...30...
Page 54: ...54...
Page 64: ...64...
Page 98: ...98...
Page 114: ...With twin connectors in the control panel holder 1 2 3 1 114 Electrical installation...
Page 115: ...With FDPI 02 modules OPEN TERMIN ATED 1 1 2 2 OPEN TERMINATED 3 Electrical installation 115 11...
Page 142: ...4 5 6 3 3 1 1 1 1 2 142 Installation example with full cabling panels option H381...
Page 150: ...150 Installation example with full cabling panels option H381...
Page 156: ...156...
Page 204: ...Standard configuration 204 Dimension drawings...
Page 206: ...Drive module with options 0B051 H356 0H371 206 Dimension drawings...
Page 207: ...Configuration with option H381 3AXD50000323210 Dimension drawings 207...
Page 208: ...LCL filter module 208 Dimension drawings...
Page 212: ...External control unit 3AXD50000011687 212 Dimension drawings...
Page 230: ...Declaration of conformity 230 The Safe torque off function...
Page 241: ...241...
Page 246: ...246...