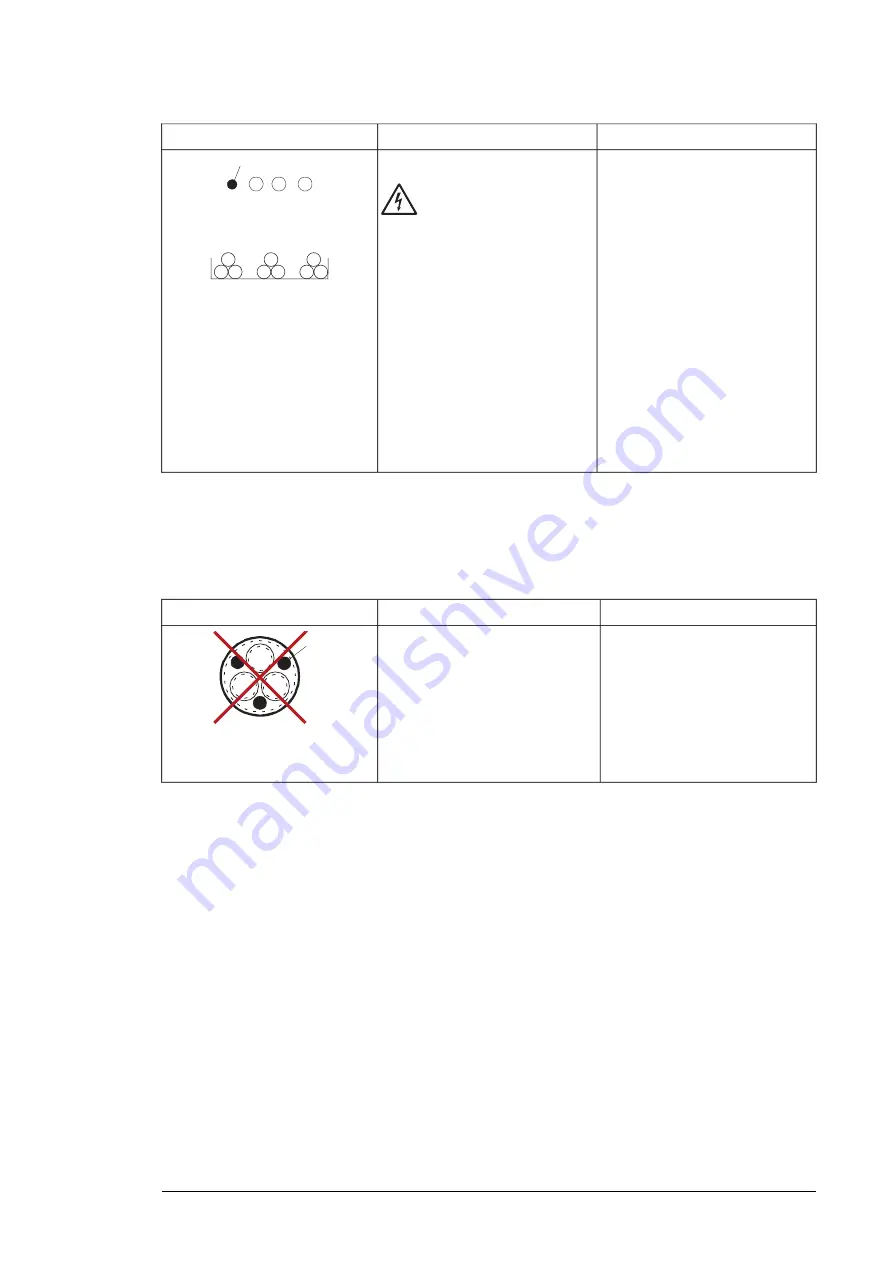
Use as motor cabling
Use as input power cabling
Cable type
No
Yes
PE
WARNING!
If you use unshielded
single-core cables in an IT
network, make sure that the
non-conductive outer
sheath (jacket) of the cables
have good contact with a
properly grounded conduct-
ive surface. For example,
install the cables on a prop-
erly grounded cable tray.
Otherwise voltage may be-
come present on the non-
conductive outer sheath of
the cables, and there is
even a risk of an electric
shock.
A single-core cable system: three
phase conductors and PE conductor
on cable tray
L1
L3
L2
L2
L1
L3
L3
L2
L1
Preferable cable arrangement to
avoid voltage or current unbalance
between the phases
1) Armor may act as an EMC shield, as long as it provides the same performance than a concentric EMC shield of a shielded
cable. To be effective at high frequencies, the shield conductivity must be at least 1/10 of the phase conductor conductivity.
The effectiveness of the shield can be evaluated based on the shield inductance, which must be low and only slightly
dependent on frequency. The requirements are easily met with a copper or aluminum shield/armor. Cross-section of a
steel shield has to be ample and the shield helix low gradient. Galvanizing increases the high-frequency conductivity.
Not allowed power cable types
Use as motor cabling
Use as input power cabling
Cable type
No
No
PE
Symmetrical shielded cable with in-
dividual shields for each phase
conductor
■
Additional guidelines, North America
ABB recommends the use of conduit for power wiring to the drive and between the drive
and the motor(s). Due to the variety of application needs, metallic and non-metallic conduit
can be used. ABB recommends the use of metallic conduit.
The following table shows examples of various materials and methods for wiring the drive
in the intended application. See NEC 70 along with state and local codes for the appropriate
materials for your application.
In all applications, ABB prefers the use of symmetrical shielded VFD cable between drive
and motor(s).
Guidelines for planning the electrical installation 85
Summary of Contents for ACS880-14
Page 1: ...ABB INDUSTRIAL DRIVES ACS880 14 drive modules 132 400 kW 200 400 hp Hardware manual...
Page 2: ......
Page 4: ......
Page 14: ...14...
Page 24: ...24...
Page 30: ...30...
Page 54: ...54...
Page 64: ...64...
Page 98: ...98...
Page 114: ...With twin connectors in the control panel holder 1 2 3 1 114 Electrical installation...
Page 115: ...With FDPI 02 modules OPEN TERMIN ATED 1 1 2 2 OPEN TERMINATED 3 Electrical installation 115 11...
Page 142: ...4 5 6 3 3 1 1 1 1 2 142 Installation example with full cabling panels option H381...
Page 150: ...150 Installation example with full cabling panels option H381...
Page 156: ...156...
Page 204: ...Standard configuration 204 Dimension drawings...
Page 206: ...Drive module with options 0B051 H356 0H371 206 Dimension drawings...
Page 207: ...Configuration with option H381 3AXD50000323210 Dimension drawings 207...
Page 208: ...LCL filter module 208 Dimension drawings...
Page 212: ...External control unit 3AXD50000011687 212 Dimension drawings...
Page 230: ...Declaration of conformity 230 The Safe torque off function...
Page 241: ...241...
Page 246: ...246...