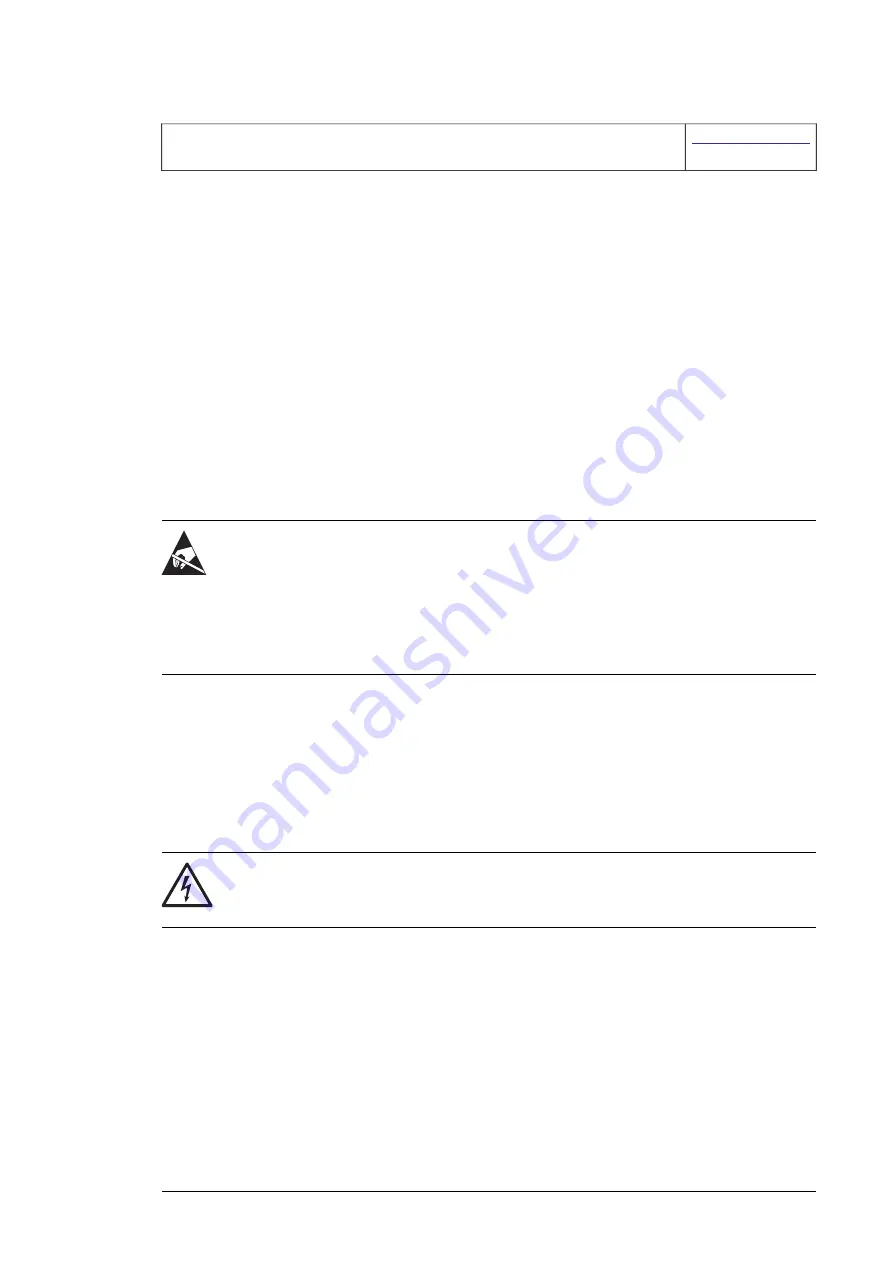
FPTC-02 ATEX-certified thermistor protection module, Ex II (2) GD (L537+Q971)
for ACS880 drives user's manual
Controlling a contactor between drive and motor
The control of the output contactor depends on how you use the drive, that is, which motor
control mode and which motor stop mode you select.
If you have the DTC motor control mode and the motor ramp stop mode selected, use this
operation sequence to open the contactor:
1. Give a stop command to the drive.
2. Wait until the drive decelerates the motor to zero speed.
3. Open the contactor.
If you have the DTC motor control mode and the motor coast stop, or scalar control mode
selected, open the contactor as follows:
1. Give a stop command to the drive.
2. Open the contactor.
WARNING!
When the DTC motor control mode is in use, never open the output contactor while
the drive controls the motor. The DTC motor control operates extremely fast, much
faster than it takes for the contactor to open its contacts. When the contactor starts
opening while the drive controls the motor, the DTC control will try to maintain the
load current by immediately increasing the drive output voltage to the maximum.
This will damage, or even burn the contactor completely.
Implementing a bypass connection
If bypassing is required, employ mechanically or electrically interlocked contactors between
the motor and the drive and between the motor and the power line. Make sure with
interlocking that the contactors cannot be closed simultaneously. The installation must be
clearly marked as defined in IEC/EN 61800-5-1, subclause 6.5.3, for example, “THIS
MACHINE STARTS AUTOMATICALLY”.
WARNING!
Never connect the drive output to the electrical power network. The connection
may damage the drive.
Guidelines for planning the electrical installation 95
Summary of Contents for ACS880-14
Page 1: ...ABB INDUSTRIAL DRIVES ACS880 14 drive modules 132 400 kW 200 400 hp Hardware manual...
Page 2: ......
Page 4: ......
Page 14: ...14...
Page 24: ...24...
Page 30: ...30...
Page 54: ...54...
Page 64: ...64...
Page 98: ...98...
Page 114: ...With twin connectors in the control panel holder 1 2 3 1 114 Electrical installation...
Page 115: ...With FDPI 02 modules OPEN TERMIN ATED 1 1 2 2 OPEN TERMINATED 3 Electrical installation 115 11...
Page 142: ...4 5 6 3 3 1 1 1 1 2 142 Installation example with full cabling panels option H381...
Page 150: ...150 Installation example with full cabling panels option H381...
Page 156: ...156...
Page 204: ...Standard configuration 204 Dimension drawings...
Page 206: ...Drive module with options 0B051 H356 0H371 206 Dimension drawings...
Page 207: ...Configuration with option H381 3AXD50000323210 Dimension drawings 207...
Page 208: ...LCL filter module 208 Dimension drawings...
Page 212: ...External control unit 3AXD50000011687 212 Dimension drawings...
Page 230: ...Declaration of conformity 230 The Safe torque off function...
Page 241: ...241...
Page 246: ...246...