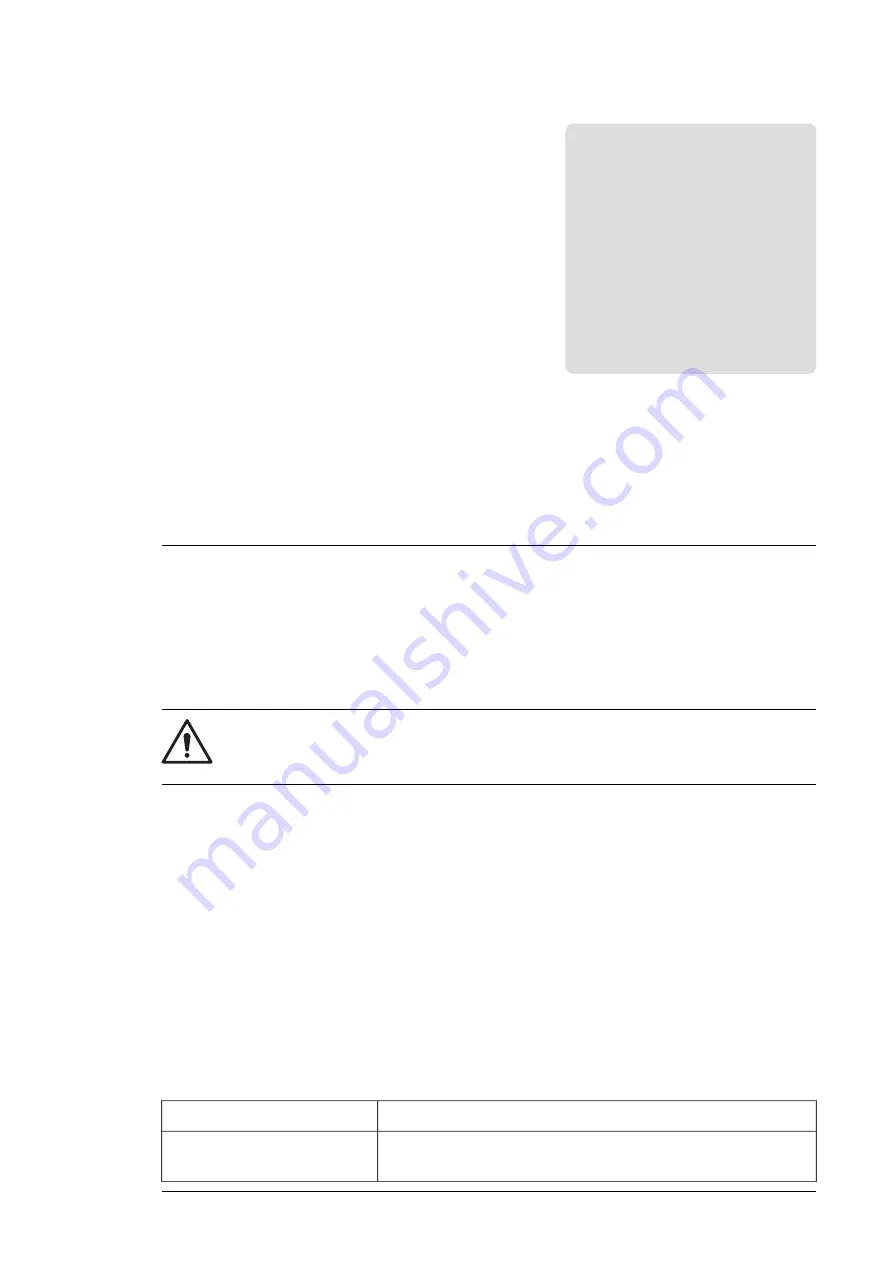
The Safe torque off function
Contents of this chapter
This chapter describes the Safe torque off (STO) function of the drive and gives instructions
for its use.
Description
WARNING!
In case of parallel-connected drives or dual-winding motors, the STO must be
activated on each drive to remove the torque from the motor.
The Safe torque off function can be used, for example, as the final actuator device of safety
circuits that stop the drive in case of danger (such as an emergency stop circuit). Another
typical application is a prevention of unexpected start-up function that enables short-time
maintenance operations like cleaning or work on non-electrical parts of the machinery without
switching off the power supply to the drive.
When activated, the Safe torque off function disables the control voltage of the power
semiconductors of the drive output stage (A, see the diagrams below), thus preventing the
drive from generating the torque required to rotate the motor. If the motor is running when
Safe torque off is activated, it coasts to a stop.
The Safe torque off function has a redundant architecture, that is, both channels must be
used in the safety function implementation. The safety data given in this manual is calculated
for redundant use, and does not apply if both channels are not used.
The Safe torque off function complies with these standards:
Name
Standard
Safety of machinery – Electrical equipment of machines – Part 1: General
requirements
IEC 60204-1:2016
EN 60204-1:2018
20
The Safe torque off function 215
Summary of Contents for ACS880-14
Page 1: ...ABB INDUSTRIAL DRIVES ACS880 14 drive modules 132 400 kW 200 400 hp Hardware manual...
Page 2: ......
Page 4: ......
Page 14: ...14...
Page 24: ...24...
Page 30: ...30...
Page 54: ...54...
Page 64: ...64...
Page 98: ...98...
Page 114: ...With twin connectors in the control panel holder 1 2 3 1 114 Electrical installation...
Page 115: ...With FDPI 02 modules OPEN TERMIN ATED 1 1 2 2 OPEN TERMINATED 3 Electrical installation 115 11...
Page 142: ...4 5 6 3 3 1 1 1 1 2 142 Installation example with full cabling panels option H381...
Page 150: ...150 Installation example with full cabling panels option H381...
Page 156: ...156...
Page 204: ...Standard configuration 204 Dimension drawings...
Page 206: ...Drive module with options 0B051 H356 0H371 206 Dimension drawings...
Page 207: ...Configuration with option H381 3AXD50000323210 Dimension drawings 207...
Page 208: ...LCL filter module 208 Dimension drawings...
Page 212: ...External control unit 3AXD50000011687 212 Dimension drawings...
Page 230: ...Declaration of conformity 230 The Safe torque off function...
Page 241: ...241...
Page 246: ...246...