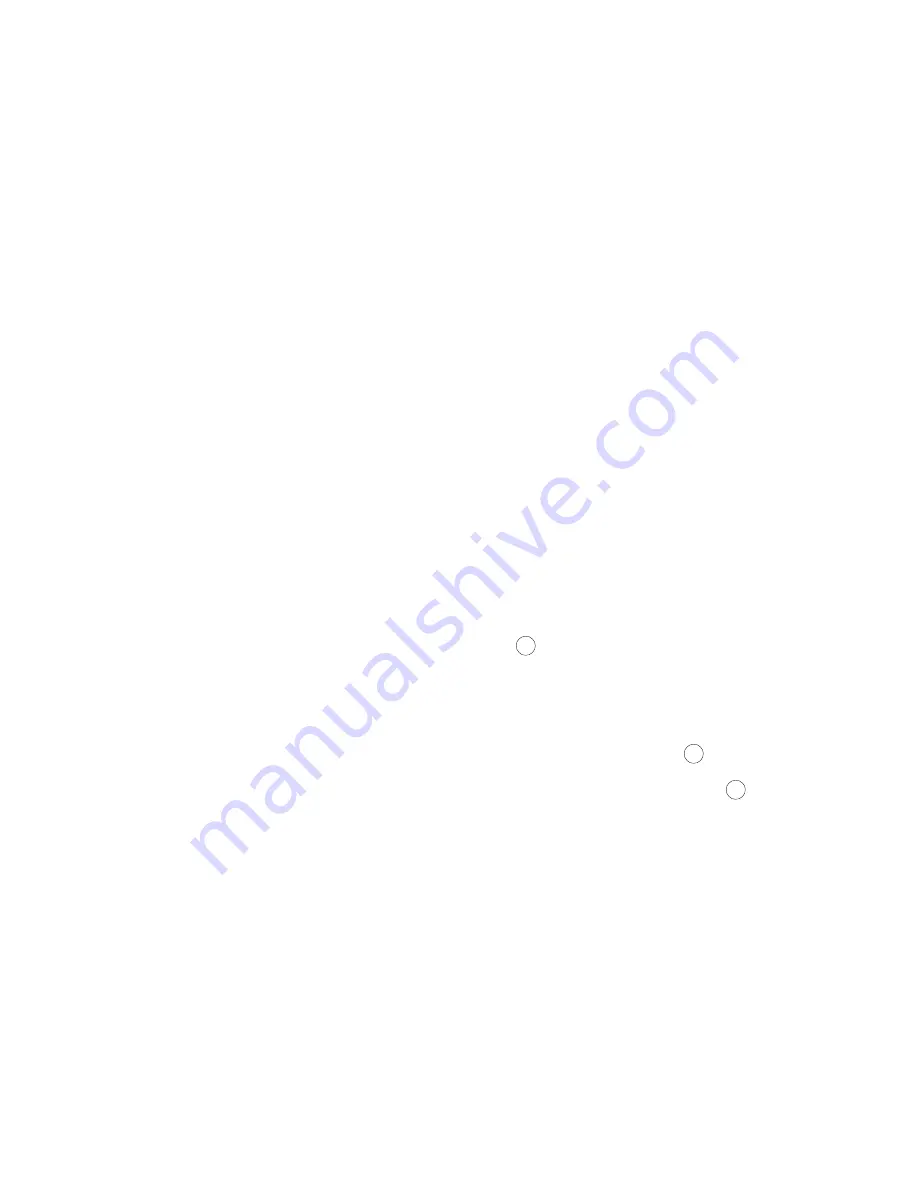
FORM 150.75-NM2
87
YORK INTERNATIONAL
HOT GAS BYPASS (LOADMINDER) OPTION
General
A factory Hot Gas Bypass Option is available as a fac-
tory installed option to prevent compressor cycling and
water temperature fluctuation at low load. This is ac-
complished by providing further capacity reduction be-
low the last step of compressor cylinder unloading by
introducing an artificial load to the cooler, which keeps
the compressor on the line. The option will provide hot
gas bypass on both compressors of the Master Module
enabling hot gas to be active regardless of which com-
pressor is in the lead.
NOTE: The microprocessor will only activate the hot
gas on the lead compressor. Hot Gas Bypass
will not operate and is not available on the Slave
Module.
The hot gas bypass consists of a pilot operated regu-
lating valve with an integral solenoid. The pilot oper-
ated solenoid is controlled by the microprocessor ac-
cording to water temperature. The regulating valve which
becomes activated when the solenoid is energized, is
controlled by suction pressure to modulate the flow of
gas in a bypass connected from the compressor dis-
charge to the cooler inlet. The following text will explain
how the hot gas solenoid is activated by the micropro-
cessor in both return and in leaving water control.
LWT Control Hot Gas Operation
The hot gas solenoid is energized when the leaving wa-
ter temperature falls below the Target water tempera-
ture, if the compressor is on its minimum stage of load-
ing. Hot gas may then be fed according to the suction
pressure and the pressure regulating valve setting. Once
activated, the micro will keep the solenoid energized
until the leaving water temperature rises above the high
limit of the Control Range or until the load becomes so
low that the hot gas can no longer keep temperature
within the control range and the micro turns the com-
pressor off. Details for setting the pressure regulator fol-
low.
RWT Control Hot Gas Operation
The hot gas solenoid is energized if the compressor is
on its minimum stage of loading and the return water
temperature falls below the following point:
ULCR - CR + CR/20
Where: ULCR = Upper Limit of Control Range
CR = Control Range Differential
Example:
In a typical system that requires a 45°F leaving water
temperature, we will have a 10° Control Range (CR)
differential which gives us an Upper Limit of Control
Range (ULCR) of 55°F. Therefore, plugging the num-
bers into the formula:
55 - 10 + (10/20) = 45½°F
The hot gas solenoid will be activated at 45½°F in the
example above and hot gas may then be fed according
to the suction pressure and the pressure regulated valve
setting. Once activated, the micro will keep the sole-
noid energized until the return water temperature rises
above the temperature designated by the formula:
ULCR - CR + CR/10
Where: ULCR = Upper Limit of Control Range
CR = Control Range Differential
Example: 55 - 10 + 10/10 = 46°F
If temperature continues to drop while the Hot Gas is
energized, the Hot Gas will be de-energized when the
compressor cycles off on temperature.
Procedure For Setting The Hot Gas Regulators
(Ref. Fig. 39)
1. If desired, set the control panel data to show suction
pressure.
2. Adjust the pilot power assembly adjustment screw
2 to approximately the middle of the adjustment
range.
3. The chiller must be running and stabilized on the mini-
mum stage capacity. In establishing this condition it
may be necessary to deactivate the regulator by de-
energizing the solenoid 1 .
4. Adjust the adjustment screw 2 in the clockwise
direction to open the valve at a higher pressure
(sooner) or in the counterclockwise direction to open
the valve at a lower pressure (slower response). The
valve is feeding when the valve outlet feels warm to
the touch.
The adjustment is correct when system suction pres-
sure rises to a point nearly equal to normal running
pressure at the midpoint in the Control Zone.
5. Further minor adjustment may be necessary to be
certain that the valve opens fully before the tempera-
ture point at which the compressor stops due to a
fall in Return or Leaving Water Temp.
6. Repeat this procedure on the other system.
Содержание YDAJ87HU7
Страница 4: ...YORK INTERNATIONAL 4 FIG 1 UNIT COMPONENTS Typical on each of the two modules 00023TG 00024TG...
Страница 5: ...FORM 150 75 NM2 5 YORK INTERNATIONAL FIG 1 UNIT COMPONENTS Cont d LD01910 00025TG...
Страница 24: ...YORK INTERNATIONAL 24 MASTER MODULE WIRING DIAGRAM LD01933 FIG 17 MASTER MODULE CONNECTION DIAGRAM...
Страница 30: ...YORK INTERNATIONAL 30 SLAVE MODULE WIRING DIAGRAM FIG 20 SLAVE MODULE CONNECTION DIAGRAM LD01941...
Страница 99: ...FORM 150 75 NM2 99 YORK INTERNATIONAL...