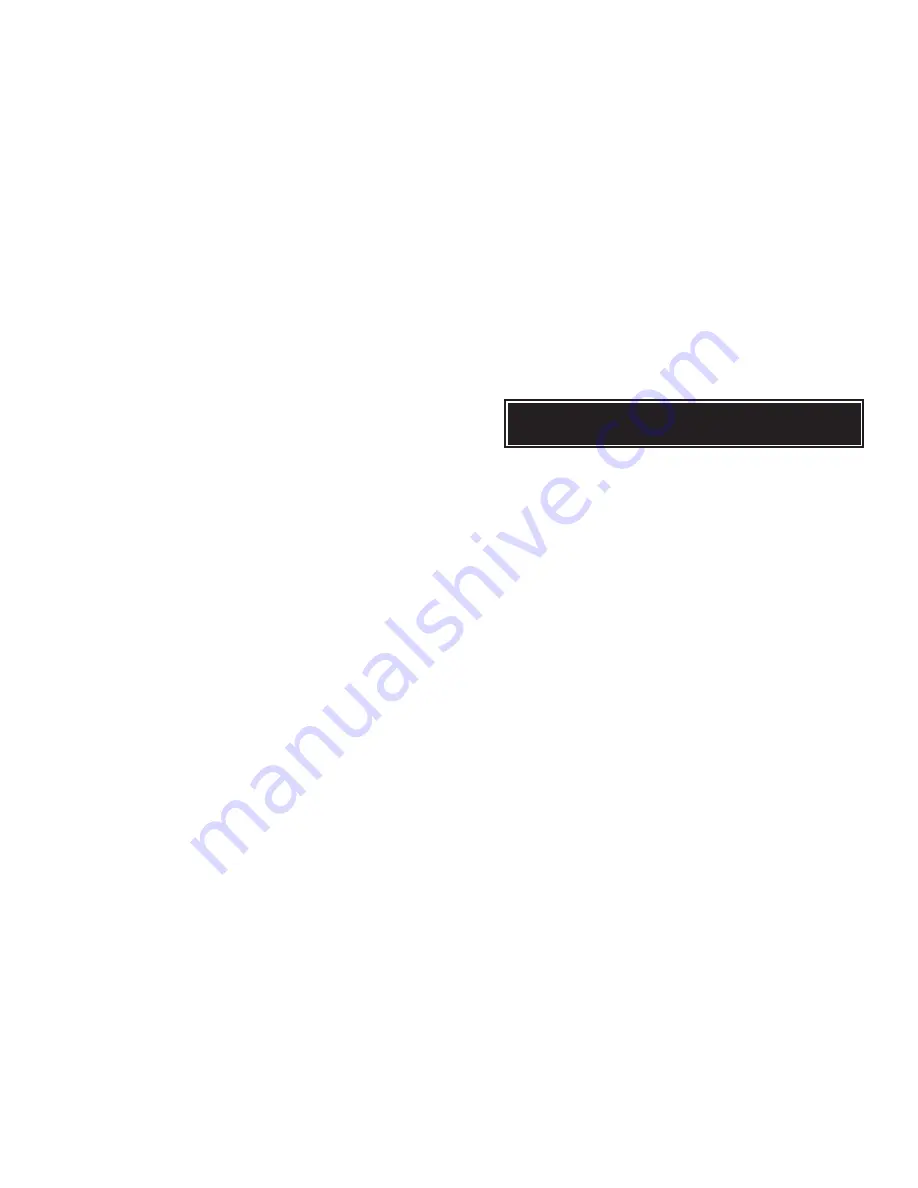
FORM 150.75-NM2
57
YORK INTERNATIONAL
There are three types of System Safeties: The Manual
Reset type, the Automatic Reset type, and Anticipation
Safety Controls. These safeties protect the chiller from
damage anytime a safety threshold is exceeded by ei-
ther shutting the system(s) down or by altering system
loading. Continuous monitoring by the microprocessor
assures that instantaneous reactions result. A status
display message will indicate when a system(s) or the
entire chiller is shut down due to a fault or when Antici-
pation safeties are operating.
An explanation of these safeties will follow.
MANUAL RESET SAFETIES
A Manual Reset Safety will shut the affected system
down whenever the safety threshold is exceeded. Au-
tomatic restart will occur after the first 2 shutdowns when
the anti-recycle timer times out, if temperature demand
exists. After any combination of 3 Manual Reset Safety
in a 90 minute time period, the affected system will shut
down and lock out on a FAULT.
After a system has shut down 3 times and locked out, a
fault display indicating the last system fault will appear
on the STATUS display message. This is accessible by
pressing the STATUS key.
To reset a locked out system, turn the affected system
switch on the Microprocessor Board (Page 78) to the
OFF position.
CAUTION: Before returning a locked out system to ser-
vice, a thorough investigation of the cause
of the fault should be made. Failure to re-
pair the cause of the fault while manually
allowing repetitive restarts may cause fur-
ther expensive damage to the system.
Each of the Manual Reset Safeties will be discussed in
detail below.
Motor Current Safety
The Motor Current Safety assures that the motor life is
not compromised due to low or high motor current. Low
motor current may result from running with low or no
refrigerant. The micro looks at motor current to protect
against this until the Low pressure bypass is de-acti-
vated. High motor current may result from power prob-
lems, too much refrigerant, very warm water, or other
high pressure situations.
The micro begins monitoring motor current after 3 sec-
onds of operation. If motor current is exceeding 120%
FLA at the 3 second point, the compressor will shut
down. After 4 seconds of operation, motor current must
be greater than 15% FLA but less than 115% FLA as
long as the compressor continues to run.
NOTE: Do not confuse FLA and RLA. FLA (full load
amps) is approximately 1.2 x RLA. RLA (run-
ning load amps) specified on the motor name-
plate, is typical current demand under rated
operating conditions in a fully loaded system.
Therefore, do not expect to see 100% FLA when
the system is fully loaded. In this condition, cur-
rents may run approximately 65-85% FLA.
An example of a motor current fault display message is
shown below:
NOTE: The Motor Protector and the mechanical High
Pressure Cut-out will also cause the MOTOR
CURRENT SAFETY to activate. The reason for
this is that both devices cause the motor con-
tractor to de-energize. Details of the operation
of these devices are provided on page 58.
Suction Pressure Safety
The Suction Pressure Safety assures that the system
is not run under low refrigerant conditions or due to a
problem which will not allow proper refrigerant flow.
For the first 30 seconds of operation, the low suction
pressure bypass is in operation. After 30 seconds of
operation, the micro begins monitoring suction pressure
and continues to do so as long as the compressor runs.
For operation periods of 30 seconds to 240 seconds,
suction pressure must be greater than 50% of the Suc-
tion Pressure Cut-out. After 240 seconds, suction pres-
sure must be greater than the cut-out.
NOTE: A transient timer is built into software to assure
that short term fluctuations in suction pressure
due to fan cycling, loading, etc. do not cause
nuisance trips on low suction pressure.
After the system has pumped down and suc-
tion pressure reaches cut-out plus 5 PSIG, the
transient timer is readied for action. If suction
pressure drops below the cut-out point, the 120
second transient timer begins timing. As long
as suction pressure doesnt drop below 50% of
cut-out during the 120 second period and rises
above cut-out before the timer times out, the
system will continue to run.
SYSTEM SAFETIES
S Y S # 1
M O T O R
C U R R E N T
S Y S # 2
M O T O R
C U R R E N T
Содержание YDAJ87HU7
Страница 4: ...YORK INTERNATIONAL 4 FIG 1 UNIT COMPONENTS Typical on each of the two modules 00023TG 00024TG...
Страница 5: ...FORM 150 75 NM2 5 YORK INTERNATIONAL FIG 1 UNIT COMPONENTS Cont d LD01910 00025TG...
Страница 24: ...YORK INTERNATIONAL 24 MASTER MODULE WIRING DIAGRAM LD01933 FIG 17 MASTER MODULE CONNECTION DIAGRAM...
Страница 30: ...YORK INTERNATIONAL 30 SLAVE MODULE WIRING DIAGRAM FIG 20 SLAVE MODULE CONNECTION DIAGRAM LD01941...
Страница 99: ...FORM 150 75 NM2 99 YORK INTERNATIONAL...