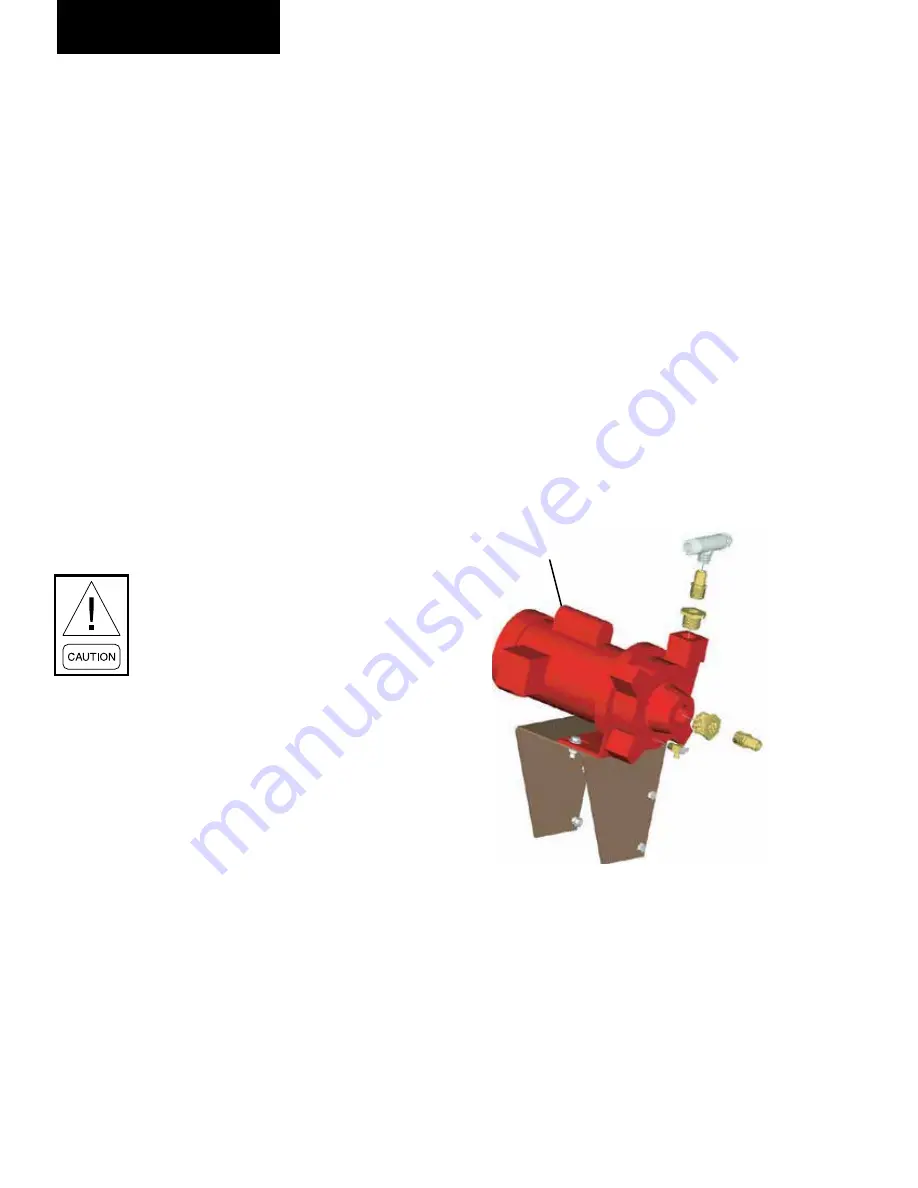
236
JOHNSON CONTROLS
FORM 201.21-NM3 (616)
VSD OPERATION AND CONTROLS (CON'T)
VSD COOLING AND COOLING LOOP
The VSD generates heat in the IGBT power modules
and the SCR/Diode assemblies, which must be removed.
The heat not only heats the modules but also the Mi-
cro/VSD cabinet.
The VSD is cooled by a glycol loop and circulating
pump. The glycol cooling loop feeds a liquid cooled
heatsink called a chillplate that cools the IGBT’s and
SCR/Diode modules. The coolant is pumped by a
circulator pump through the heatsink where it absorbs
heat in several passes of tubes on the lower rows of the
inside condenser coils where the condenser fans remove
the heat picked up from the modules. The coolant is
then pumped back to the modules. The glycol loop
also provides cooling for the Micro/VSD cabinet. The
baseplates of the power components are mounted to the
glycol cooled heatsinks in the cooling loop. The cooling
loop also circulates the glycol through a cooling coil in
the cabinet. A fan blows air from the cabinet across the
cooling coil to cool the electronics in the cabinet.
Never run the glycol pump without
coolant! Running the glycol pump
without coolant may damage the pump
seals
Always fill the system with approved
coolant to avoid damage to the pump
seals and other components.
Heat transfer characteristics of the
coolant are very critical. Substituting
coolant or adding water will result in
cooling loop performance loss and
chiller shutdown.
The glycol coolant level in the VSD cooling system
should be maintained 2-6 inches (5-15 cm) from the top
of the fill tube. This check should be performed prior to
running the pump. The pump can be test run by placing
the chiller in Service Mode. It is advisable to fill the
tube to the required level before starting the glycol pump
because it may empty when the pump starts. The level
should be topped off as needed while running. Be sure
to re-install the cap before stopping the glycol pump to
avoid overflowing the fill tube when the glycol pump
is turned off.
Glycol coolant has a defined operating life. System
coolant should be changed 5 years from date of shipment
of the equipment. Mixing other coolants or water with
the special glycol will reduce the life of the coolant, and
cause VSD overheating and damage.
VSD GLYCOL
PUMP
LD10635
MICRO PANEL
Содержание YCAV0267E
Страница 61: ...61 JOHNSON CONTROLS FORM 201 21 NM3 616 This intentionally left blank 6 ...
Страница 63: ...63 JOHNSON CONTROLS FORM 201 21 NM3 616 ELEMENTARY CONTROL WIRING DIAGRAM 3 COMPRESSOR CON T LD12552 ...
Страница 67: ...67 JOHNSON CONTROLS FORM 201 21 NM3 616 LD12556 POWER ELEMENTARY DIAGRAM 3 COMPRESSOR YCAV CHILLER CON T 6 ...
Страница 72: ...72 JOHNSON CONTROLS FORM 201 21 NM3 616 035 20326 006 REV TECHNICAL DATA LD11125 LOCATION LABEL ...
Страница 73: ...73 JOHNSON CONTROLS FORM 201 21 NM3 616 This page intentionally left blank 6 ...
Страница 88: ...88 JOHNSON CONTROLS FORM 201 21 NM3 616 LOCATION LABEL TECHNICAL DATA 035 20890 008 REV LD11140 ...
Страница 89: ...89 JOHNSON CONTROLS FORM 201 21 NM3 616 6 035 20890 009 REV LOCATION LABEL CON T LD11141 ...
Страница 146: ...146 JOHNSON CONTROLS FORM 201 21 NM3 616 TECHNICAL DATA This page intentionally left blank ...
Страница 147: ...147 JOHNSON CONTROLS FORM 201 21 NM3 616 6 This page intentionally left blank ...
Страница 247: ...247 JOHNSON CONTROLS FORM 201 21 NM3 616 This page intentionally left blank ...
Страница 269: ...269 JOHNSON CONTROLS FORM 201 21 NM3 616 This page intentionally left blank 8 ...
Страница 289: ...289 JOHNSON CONTROLS FORM 201 21 NM3 616 8 This page intentionally left blank ...
Страница 317: ...317 JOHNSON CONTROLS FORM 201 21 NM3 616 8 This page intentionally left blank ...
Страница 348: ...348 JOHNSON CONTROLS FORM 201 21 NM3 616 MAINTENANCE NOTES ...
Страница 349: ...349 JOHNSON CONTROLS FORM 201 21 NM3 616 9 NOTES ...