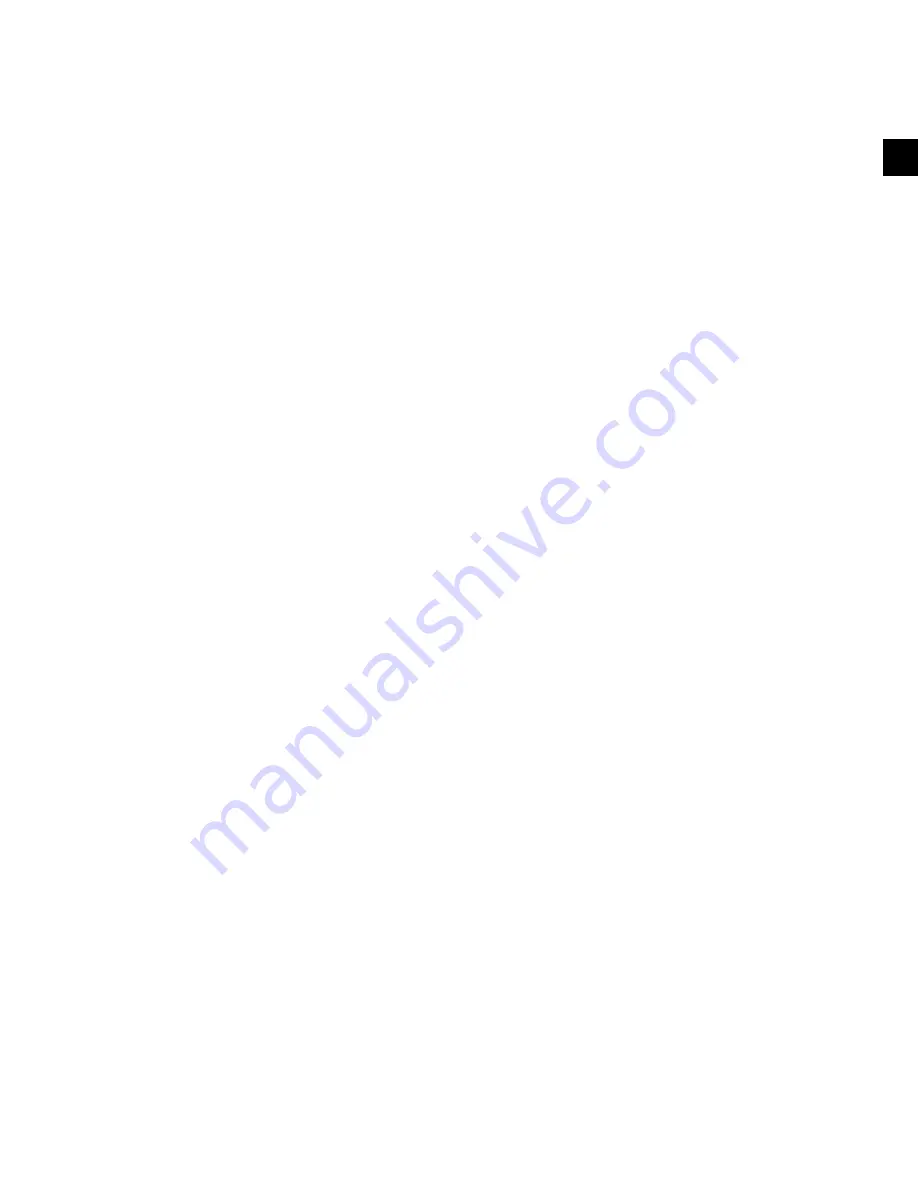
19
JOHNSON CONTROLS
FORM 201.21-NM3 (616)
2
Gate Bipolar Transistor (IGBT) modules mounted to a
liquid cooled heatsink, and a IGBT Gate Driver Board,
which provides the On and Off gating pulses to the
IGBT’s as determined by the VSD Logic board. In
order to minimize the parasitic inductance between the
IGBT’s and the capacitor banks, copper plates, which
electrically connect the capacitors to one another and to
the IGBT’s are connected together using a “laminated
bus” structure.
This “laminated bus” structure is a actually composed of
a pair of copper bus plates with a thin sheet of insulating
material acting as the separator/insulator. The “lami-
nated bus” structure forms a parasitic capacitor, which
acts as a small valued capacitor, effectively canceling
the parasitic inductance of the bus bars themselves. To
further cancel the parasitic inductances, a series of small
film capacitors are connected between the positive and
negative plates of the DC link.
The VSD output suppression
network is composed of
a series of capacitors and resistors connected in a three
phase delta configuration. The parameters of the sup
-
pression network components are chosen to work in
unison with the parasitic inductance of the DC to AC
inverter sections in order to simultaneously limit both the
rate of change of voltage and the peak voltage applied to
the motor windings. By limiting the peak voltage to the
motor windings, as well as the rate-of-change of motor
voltage, we can avoid problems
commonly associated
with PWM motor drives, such as stator-winding end-turn
failures and electrical fluting of motor bearings.
The VSD is cooled by a propylene glycol cooling
loop. The loop utilizes a glycol pump, which pumps
glycol through the VSD heatsinks to cool the power
components. The glycol is then circulated through the
condenser to reject the heat from the VSD. The cooled
glycol is then circulated back through the loop.
Various ancillary sensors and boards are used to send
information back to the VSD Logic board. Each IGBT
Power Module within the DC to AC inverter section con-
tains a thermistor heatsink temperature sensor to provide
temperature information to the VSD logic board. The
Bus Isolator board utilizes three resistors on the board
to provide a “safe” impedance (resistance) between the
DC link filter capacitors located on the output phase
bank assemblies and the VSD logic board. It provides
the means to sense the positive, midpoint and negative
connection points of the VSD’s DC link without apply-
ing high voltage to the VSD Logic Board. A Current
Transformer is included on each output phase assembly
to provide motor current information to the VSD logic
board.
ACCESSORIES AND OPTIONS
Single Point Circuit Breaker
A single-point supply circuit with factory provided
circuit breaker protection with lockable external handle
located in the panel.
Building Automation System (BAS) Interface
Provides a means to reset the leaving chilled liquid
temperature or percent full load amps (current limiting)
from a BAS Interface.
The chiller microprocessor board will accept a 4 to
20mA or 0 to 10VDC input from an ISN or BAS.
The chiller is also capable of accepting an RS-485 com-
munications link through the Microgateway.
Condenser Coil Protection
The standard condenser coils have aluminum fins, cop
-
per tubes, and galvanized steel supports for generally
adequate corrosion resistance. However, these materials
are not adequate for all environments.
The following options provide added protection:
Black fin condenser coils –
Condenser coils con-
structed using black epoxy-coated aluminum fin stock
for corrosion-resistance for typical seashore locations
(not directly exposed to salt spray).
Copper fin condenser coils –
Coils constructed with
corrosion-resistant copper fins. Not recommended in
areas where units may be exposed to acid rain.
Epoxy Coated Condenser Coils –
Completed
condenser coil assemblies are covered with a cured
epoxy coating. Probably the most suitable selection
for seashore locations where salt spray may come into
contact with the fins, and other corrosive applications
except: strong alkalis, oxidizers, and wet bromine,
chlorine, and fluorine in concentrations greater than
100 PPM.
Содержание YCAV0267E
Страница 61: ...61 JOHNSON CONTROLS FORM 201 21 NM3 616 This intentionally left blank 6 ...
Страница 63: ...63 JOHNSON CONTROLS FORM 201 21 NM3 616 ELEMENTARY CONTROL WIRING DIAGRAM 3 COMPRESSOR CON T LD12552 ...
Страница 67: ...67 JOHNSON CONTROLS FORM 201 21 NM3 616 LD12556 POWER ELEMENTARY DIAGRAM 3 COMPRESSOR YCAV CHILLER CON T 6 ...
Страница 72: ...72 JOHNSON CONTROLS FORM 201 21 NM3 616 035 20326 006 REV TECHNICAL DATA LD11125 LOCATION LABEL ...
Страница 73: ...73 JOHNSON CONTROLS FORM 201 21 NM3 616 This page intentionally left blank 6 ...
Страница 88: ...88 JOHNSON CONTROLS FORM 201 21 NM3 616 LOCATION LABEL TECHNICAL DATA 035 20890 008 REV LD11140 ...
Страница 89: ...89 JOHNSON CONTROLS FORM 201 21 NM3 616 6 035 20890 009 REV LOCATION LABEL CON T LD11141 ...
Страница 146: ...146 JOHNSON CONTROLS FORM 201 21 NM3 616 TECHNICAL DATA This page intentionally left blank ...
Страница 147: ...147 JOHNSON CONTROLS FORM 201 21 NM3 616 6 This page intentionally left blank ...
Страница 247: ...247 JOHNSON CONTROLS FORM 201 21 NM3 616 This page intentionally left blank ...
Страница 269: ...269 JOHNSON CONTROLS FORM 201 21 NM3 616 This page intentionally left blank 8 ...
Страница 289: ...289 JOHNSON CONTROLS FORM 201 21 NM3 616 8 This page intentionally left blank ...
Страница 317: ...317 JOHNSON CONTROLS FORM 201 21 NM3 616 8 This page intentionally left blank ...
Страница 348: ...348 JOHNSON CONTROLS FORM 201 21 NM3 616 MAINTENANCE NOTES ...
Страница 349: ...349 JOHNSON CONTROLS FORM 201 21 NM3 616 9 NOTES ...