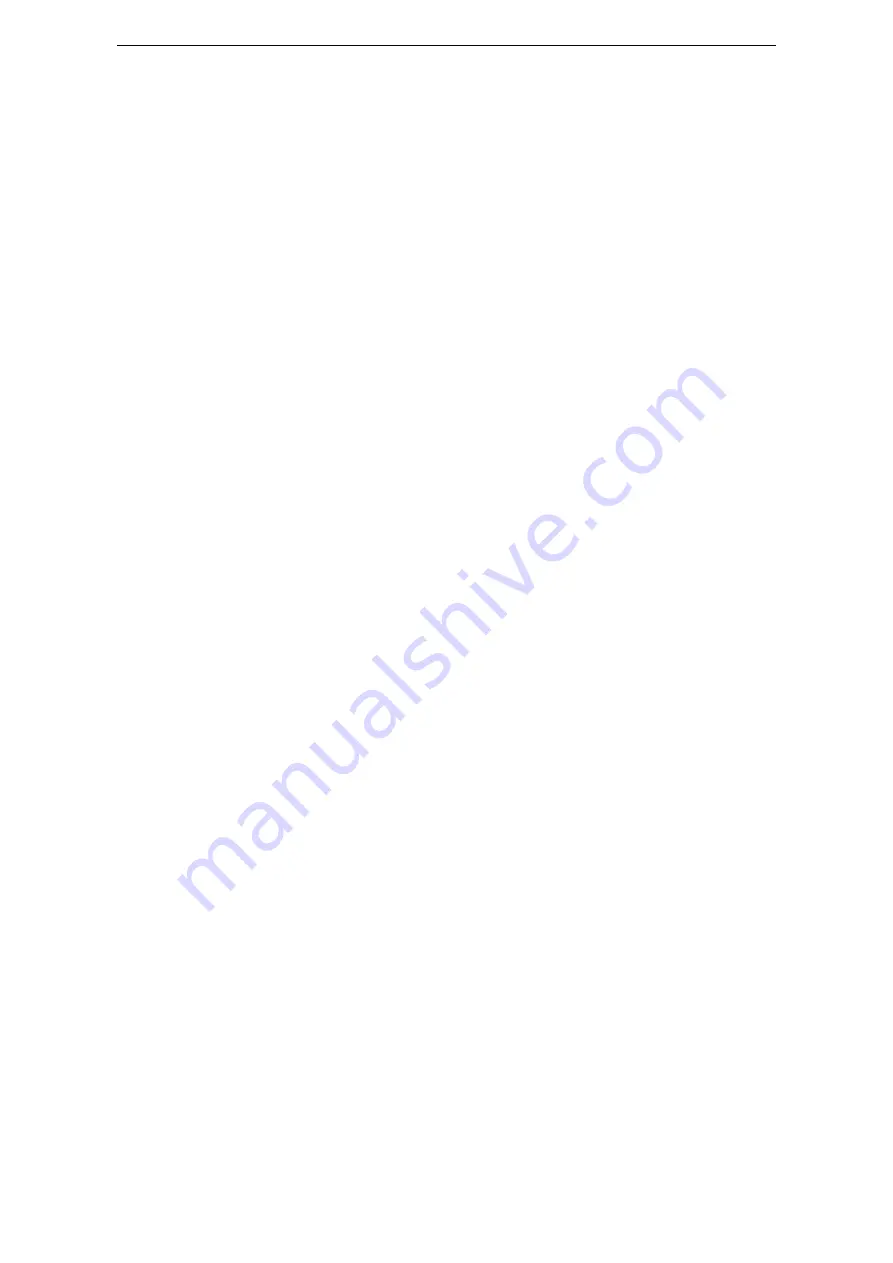
127
6.3.4 Notes
The gain parameters corresponding to the rigidity level can be independently fine-tuned in
the fast adjustment mode.
In order to ensure stability, the gain of model loops is small at low rigidity level, which can
be added separately when there is high response requirement.
When vibration occurs in fast adjustment, the torque instruction filter P2-35 can be modified.
If it is ineffective, the mechanical characteristic analysis can be used and the relevant notch
parameters can be set (refer to chapter 6.7 vibration suppression).
Fast adjustment mode defaults to set a rigidity level. If the gain does not meet the mechanical
requirements, please gradually increase or decrease the settings.
At present, gain switching function is not supported, that is, the second gain parameters such
as P1-05, P1-06, P1-07 are invalid.
6.4 Auto-tuning
6.4.1 Overview
Auto-tuning is divided into internal instruction auto-tuning and external instruction auto-tuning.
Auto-tuning (internal instruction) refers to the function of automatic operation (forward and reverse
reciprocating motion) of servo unit without instructions from the upper device and adjusting according
to the mechanical characteristics in operation.
Auto-tuning (external instruction) is the function of automatically optimizing the operation according
to the instructions from the upper device.
The automatic adjustments are as follows:
Load moment of inertia
Gain parameters (speed loop, position loop, model loop gain)
Filter (notch filter, torque instruction filter)
6.4.2 Notes
Untunable occasions
Mechanical systems can only operate in one direction.
Setting occasions that are prone to failure
Excessive load moment of inertia;
The moment of inertia varies greatly during operation.
Low mechanical rigidity, vibration during operation and failure of detection positioning;
The running distance is less than 0.5 circles.
Preparations before auto-tuning
Use position mode;
Driver in BB state;
Driver without alarm;
The matching of the number of pulses per rotation and the width of positioning completion
should be reasonable.
Содержание DS5F Series
Страница 1: ...DS5F series servo driver User manual WUXI XINJE ELECTRIC CO LTD Data No SC5 02 20200217 2 3 ...
Страница 2: ......
Страница 41: ...39 3 2 5 Encoder feedback output signal Servo driver differential to collector upper device ...
Страница 124: ...122 2 select jog setting or manual setting to configure the inertia estimation trip 3 Set the auto tuning interface ...
Страница 202: ...200 Appendix 9 Torque speed characteristic curve ...
Страница 203: ...201 ...
Страница 204: ...202 ...