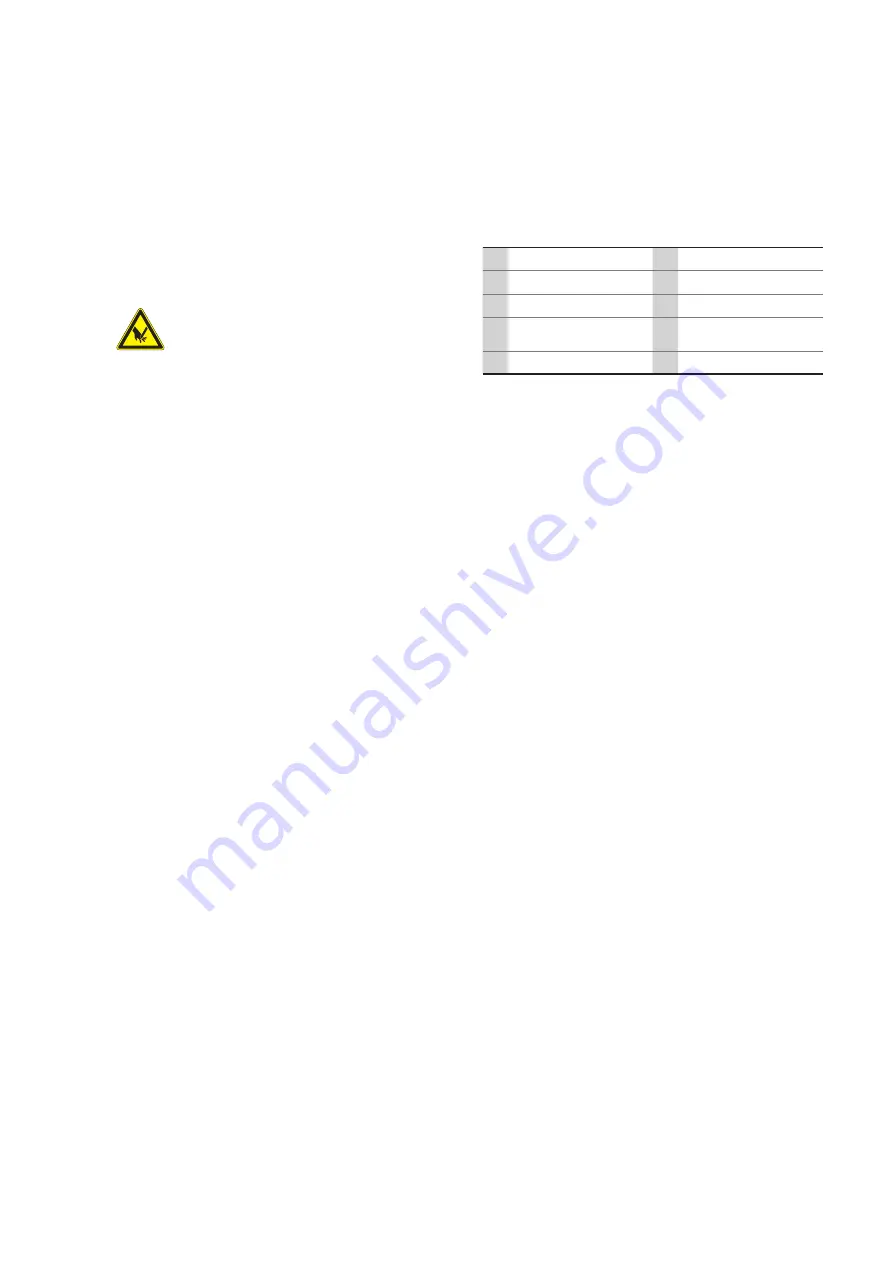
Installation and operating instructions Wilo-RexaBloc RE/Rexa BLOC 41
INSTALLATION English
5.3.2. Maintenance work
After a storage period of more than 6 months, the following
maintenance work must be carried out before installation:
• Rotate impeller
• Check oil in the sealing chamber
Rotate impeller
1.
Place the hydraulics horizontally on a firm surface.
Make sure that the hydraulics cannot fall over and/or slip!
2. Carefully and slowly reach into the hydraulics housing
through the suction port and rotate the impeller.
WARNING! Sharp edges!
Sharp edges can form on the impeller and the
opening on the suction port. There is a risk of
injury! Wear the necessary protective cloth-
ing, such as protective gloves.
5.3.3.
Check oil in the sealing chamber (“Fig. 4.: Screw
plugs”)
The sealing chamber has a separate opening for draining and
filling the sealing chamber.
1.
Place the hydraulics horizontally on a firm surface.
Make sure that the hydraulics cannot fall over and/or slip!
2. Unscrew screw plug (D+).
3. Place a suitable tank under the screw plug (D-) to collect
the operating fluid.
4.
Unscrew screw plug (D-) and allow the operating fluid to
drain out. If the oil is clear, does not contain any water,
and the quantity matches the specification, it can be
reused. If the oil is contaminated, it must be disposed of
in accordance with the requirements in the “Disposal”
Section.
5. Clean the screw plug (D-), renew the seal ring and screw
it back in.
6.
Pour the operating fluid in through the opening (D+).
Note the recommended operating fluids and filling
quantities, see Section 8!
7. Clean the screw plug (D+), renew the seal ring and screw
it back in.
5.3.4. Stationary dry well installation
In this installation type, the operating space is divided:
collector tank and machine room. The fluid is collected in the
collector tank and the hydraulics is installed in the machine
room. The operating space must be blocked out as per the
manufacturer’s configuration or consulting aid. The hydrau
-
lics is connected to the pipeline system on the suction and
discharge side at the specified point in the machine room.
The hydraulics is not immersed in the fluid.
The pipeline system on the suction and discharge side
must be self-supporting, i.e. it may not be supported by
the hydraulics. In addition, the hydraulics connection to the
pipeline system must be free of stress and vibrations. We
therefore recommend using elastic connection pieces (com-
pensators).
The following operating parameters must be complied with:
• The
maximum fluid temperature
is
70 °C
.
•
Motor cooling
– To ensure sufficient motor cooling by
the motor fan, the minimum distance to the rear wall
must be complied with. See the operating and mainte-
nance manual of the motor manufacturer!
•
Max. ambient temperature
– See the operating and
maintenance manual of the motor manufacturer.
The hydraulics is not self-priming so that hydraulics hous-
ing must be completely filled with the fluid. Ensure that
there is an appropriate inlet pressure. Air pockets are to be
avoided at all costs. Appropriate ventilation systems must
be provided!
Fig. 3.: Stationary dry well installation
1 Collector tank
6 Compensator
2 Machine room
7 Hydraulics
3 Gate valve inlet
8 Standard motor
4 Gate valve discharge
pipeline
9 Attachment points for
floor fixation
5 Non-return valve
10 Flange foot arch
Work steps
1.
Installing the hydraulics: about 3–5 h
•
Check that the pipeline system is secured firmly.
• Fasten lifting equipment to the corresponding
attachment points and position the hydraulics in the
planned location.
• For horizontal installation, the hydraulics is attached
to the foundation. (6x fixation points: 4x hydraulics,
2x supports). We recommend using anchor bolts for
this fixation.
• Vertical installation; set up the hydraulics vertically.
• For vertical installation, the hydraulics is screwed to
the piping (flange foot bend).
Notice: The hydraulics is constructed in a “back pull-out”
design. In other words, the motor, bearing housing and
impeller can be removed as a unit without dismantling the
hydraulics housing from the piping. For horizontal installa-
tion, a minimum distance of 500 mm must be ensured here
between the motor fan and the rear wall.
• Loosen the lifting gear and remove the transport
shackle from the discharge port.
Keep the transport shackle for later transport!
• Connect the pipeline system on the suction and
discharge side. To ensure that the pipeline system is
connected free of stress and vibrations, we recom-
mend using elastic connection pieces (compensators)
• Route the power supply cables (
must
be provided by
the customer) in accordance with local requirements.
•
Have the electrical connections made by a qualified
electrician.
2. Install optional accessories, such as alarm switchgear for
detecting moisture.
3.
Commissioning the hydraulics: about 2–4 h
• As described in the “Commissioning” section
• Open the slide valves on suction and discharge sides.
• Vent the hydraulics and pipeline system.