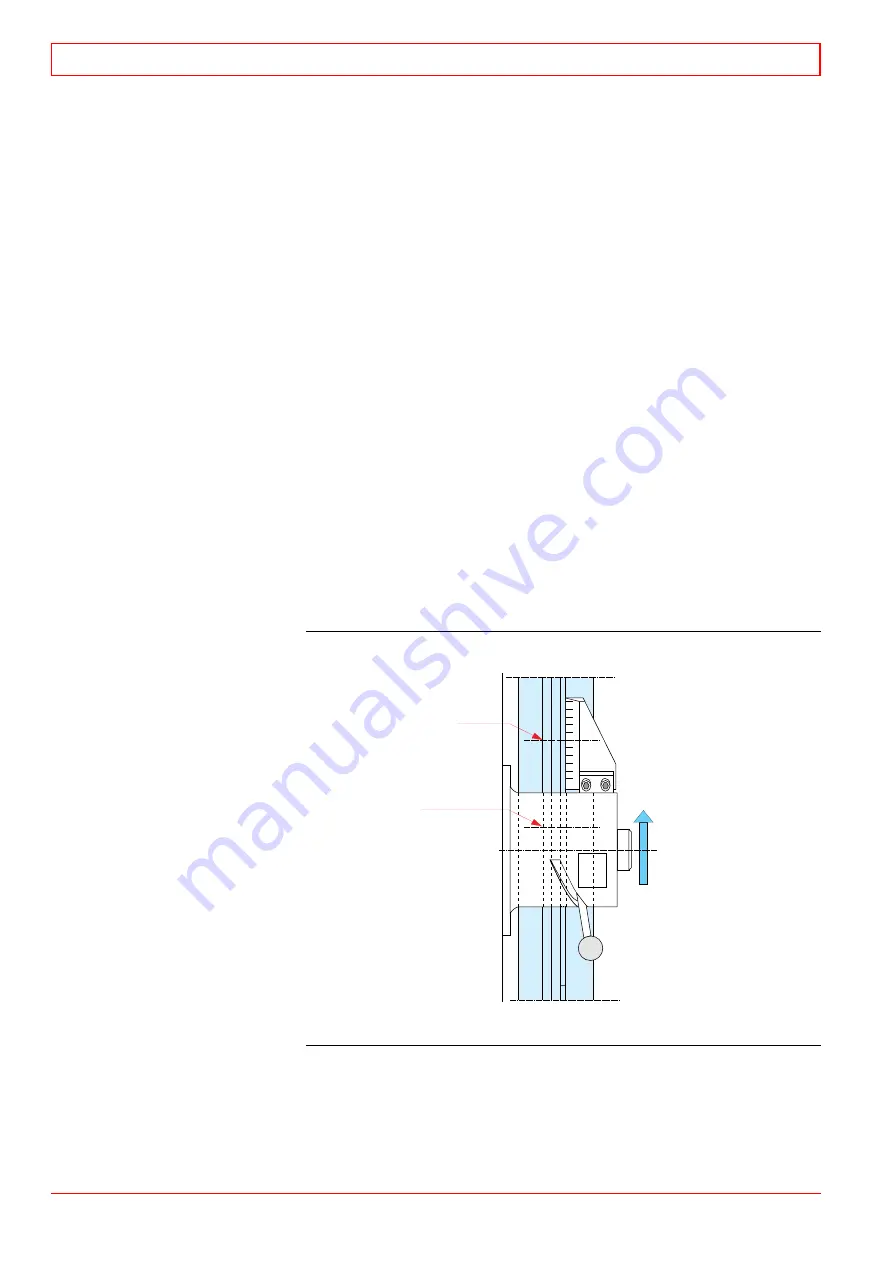
a)
For the first time when the exhaust stroke of the previous
working cycle ends and the suction stroke of the following one
begins. Exhaust valves as well as inlet valves are then somewhat
open and scavenging takes place. If the crankshaft is turned to
and fro near this TDC, both exhaust and inlet valves will move,
a fact that indicates that the crankshaft is near the position which
can be named
TDC at scavenging.
b)
The second time is after the compression stroke and before the
working stroke. Slightly before this TDC the fuel injection takes
place (on an engine in operation) and this TDC can therefore be
defined
TDC at firing.
Characteristic is that all valves are closed
and do not move if the crankshaft is turned. When watching the
camshaft and the injection pump it is possible to note that the
pump tappet roller is on the lifting side of the fuel cam.
Marking of the flywheel.
The flywheel is divided in 360°, starting
from
TDC at firing
for cylinder 1. TDC at firing for every cylinder
is marked on the flywheel. There is a common marking for the
cylinders in engines with even cylinder numbers, one cylinder is
at TDC at firing and the other is at TDC at scavenging. There are
separate scales for A- and B-bank in a V-engine. See also the firing
order in chapter 01. Firing interval, in crank angles, can be
determined by dividing 720° with the number of cylinder.
Example of reading the flywheel
Example:
On a 12V32 engine, the fuel timing is read to 10° for
cylinder A2 when the flywheel is in the position shown in the above
figure.
55
4
43
3
2
21
1
0
60
110
Clockwise rotating engine
130
80
120 CYL A2, 5 TDC
70
10˚
Cyl A2 TDC
140
90
Fig 00-3
4000029706
00
Contents, Instructions, Terminology
32-200328-03
00 - 4
WÄRTSILÄ 32
Содержание PAAE051728
Страница 4: ......
Страница 18: ...Appendix B Welding Precautions 200640 00 6...
Страница 26: ...01 Main Data Operating Data and General Design 32 200634 01 01 8 W RTSIL 32...
Страница 60: ...Appendix A Environmental Hazards 200507 02A 10...
Страница 68: ...Page 7 7 Document No 4V92A0645 Rev j...
Страница 84: ...03 Start Stop and Operation 32 200402 04 03 12 W RTSIL 32...
Страница 98: ...04 Maintenance Schedule 32 200623 01 04 14 W RTSIL 32...
Страница 154: ...07 Tightening Torques and Use of Hydraulic Tools 32 200643 01 07 30 W RTSIL 32...
Страница 162: ...08 Operating Troubles Emergency Operation 32 200402 01 08 8 W RTSIL 32...
Страница 164: ...Specific Installation Data 2005 01 09 2...
Страница 178: ...10 Engine Block with Bearings Oil Sump and Cylinder Liner 32 200150 10 14 W RTSIL 32 34SG...
Страница 216: ...Appendix A Testing of cylinder tightness 32 200142 A 4 W rtsil 20 32 34...
Страница 226: ...13 Camshaft Driving Gear 32 200546 02 13 10 W RTSIL 32...
Страница 253: ...U tube manometer Fig 15 12 401508200050 32 200549 10 Turbocharging and Air Cooling 15 W RTSIL 32 15 19...
Страница 254: ...15 Turbocharging and Air Cooling 32 200549 10 15 20 W RTSIL 32...
Страница 274: ...16 Injection System 32 200627 01 16 20 W RTSIL 32...
Страница 280: ...Fuel System 32 200508 07 17 6 W RTSIL 32...
Страница 314: ...19 Cooling Water System 32 200050 19 14 W RTSIL 32...
Страница 394: ...23 Instrumentation and Automation 32 200115 II 23 60 W RTSIL 32...