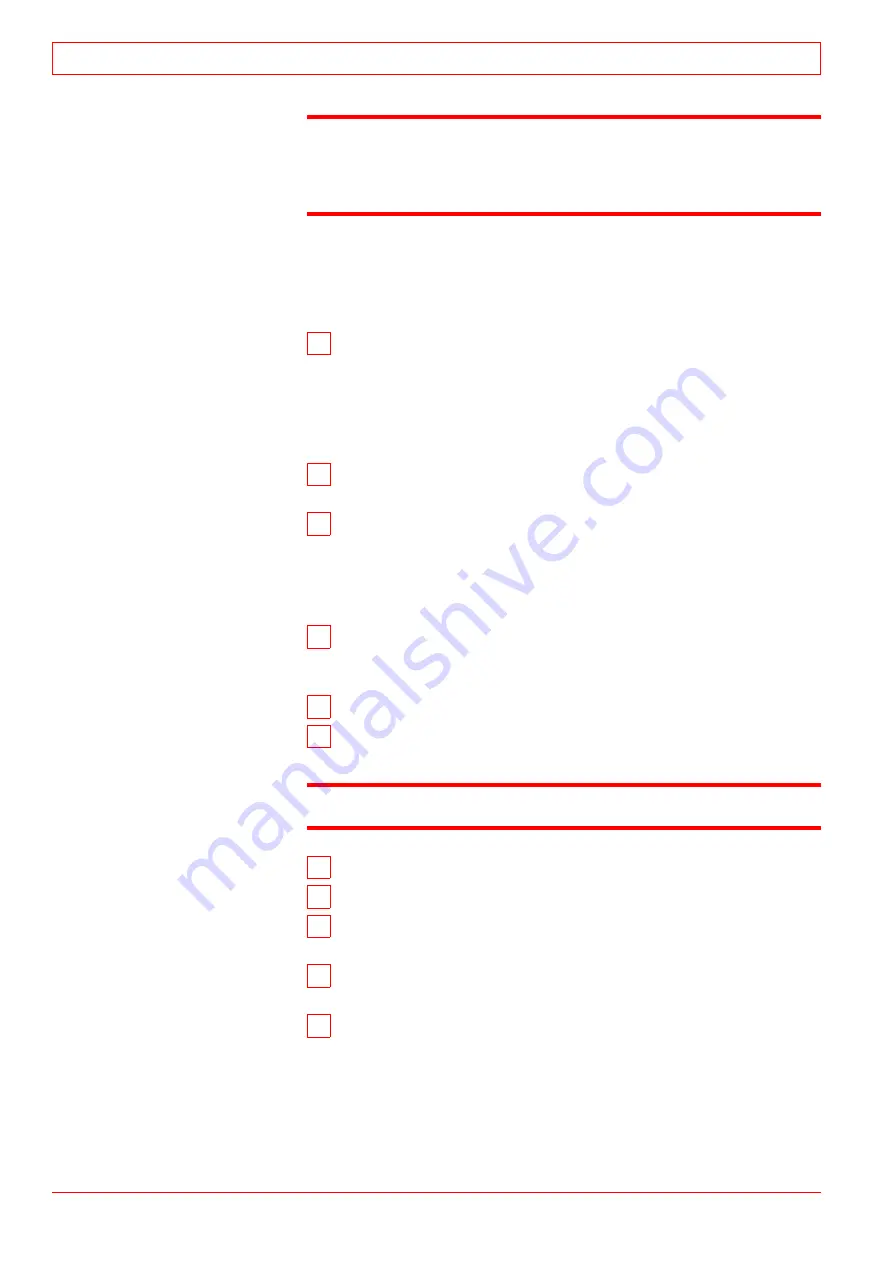
Note!
Should a higher differential pressure occur beforehand, all the
filter candles (13) and the protective filter (2) must be checked
and, if necessary, cleaned or the candles are to be replaced
by new ones.
A highly contaminated protective filter is a sign of prolonged
operation with defective or clogged filter candles and thus (from
a differential pressure of 2 bar upwards) opened overflow valves.
It is imperative to check these components.
3 Check the ease of movement
of the worm gear unit (6),
the turbine (9) including gear (10) with flushing arm (4) see
Fig 18-6.
To this end the cover (5) or the screw plug must be removed. Now
check the ease of movement with a suitable spanner (on the
hexagon of the worm gear unit).
4 It is recommended to replace
the filter candles after 2
years.
5 Replace the O-rings.
It is advisable to replace all O-rings
and seals during an overhaul and when opened.
18.7.2.1 Filter candle inspection and cleaning
1 Drain the filter,
open the plug (16) then open the plug (14),
thereafter discharge oil. Do not refill the system with
drained oil because it is very dirty.
2 Remove the cover (17)
by opening the nuts, see Fig 18-6.
3 Pull the entire filter element
including flushing arm (4)
and gear (10) out of the housing with a suitable tool.
Note!
Make sure that the exposed gear (10) is not damaged.
4 Remove the cover plate (1).
5 Remove the end plate (18)
by opening the screws.
6 The filter candles (13)
and protective filter (2) can now be
removed.
7 Place the filter candles
and the protective filter in a suit-
able cleaner or diesel oil, max. soaking time 24 hours.
8 After immersing
clean them from the outside inwards us-
ing high pressure.
It must be ensured that the filter candles are cleaned at a pressure
of max. 60 bar and at a minimum distance of cleaning nozzle of
20 cm. Otherwise, damage to the mesh is possible.
To get a optimal cleaning effect it is recommended to use special
18
Lubricating Oil System
32-200052
18 - 14
WÄRTSILÄ 32
Содержание PAAE051728
Страница 4: ......
Страница 18: ...Appendix B Welding Precautions 200640 00 6...
Страница 26: ...01 Main Data Operating Data and General Design 32 200634 01 01 8 W RTSIL 32...
Страница 60: ...Appendix A Environmental Hazards 200507 02A 10...
Страница 68: ...Page 7 7 Document No 4V92A0645 Rev j...
Страница 84: ...03 Start Stop and Operation 32 200402 04 03 12 W RTSIL 32...
Страница 98: ...04 Maintenance Schedule 32 200623 01 04 14 W RTSIL 32...
Страница 154: ...07 Tightening Torques and Use of Hydraulic Tools 32 200643 01 07 30 W RTSIL 32...
Страница 162: ...08 Operating Troubles Emergency Operation 32 200402 01 08 8 W RTSIL 32...
Страница 164: ...Specific Installation Data 2005 01 09 2...
Страница 178: ...10 Engine Block with Bearings Oil Sump and Cylinder Liner 32 200150 10 14 W RTSIL 32 34SG...
Страница 216: ...Appendix A Testing of cylinder tightness 32 200142 A 4 W rtsil 20 32 34...
Страница 226: ...13 Camshaft Driving Gear 32 200546 02 13 10 W RTSIL 32...
Страница 253: ...U tube manometer Fig 15 12 401508200050 32 200549 10 Turbocharging and Air Cooling 15 W RTSIL 32 15 19...
Страница 254: ...15 Turbocharging and Air Cooling 32 200549 10 15 20 W RTSIL 32...
Страница 274: ...16 Injection System 32 200627 01 16 20 W RTSIL 32...
Страница 280: ...Fuel System 32 200508 07 17 6 W RTSIL 32...
Страница 314: ...19 Cooling Water System 32 200050 19 14 W RTSIL 32...
Страница 394: ...23 Instrumentation and Automation 32 200115 II 23 60 W RTSIL 32...