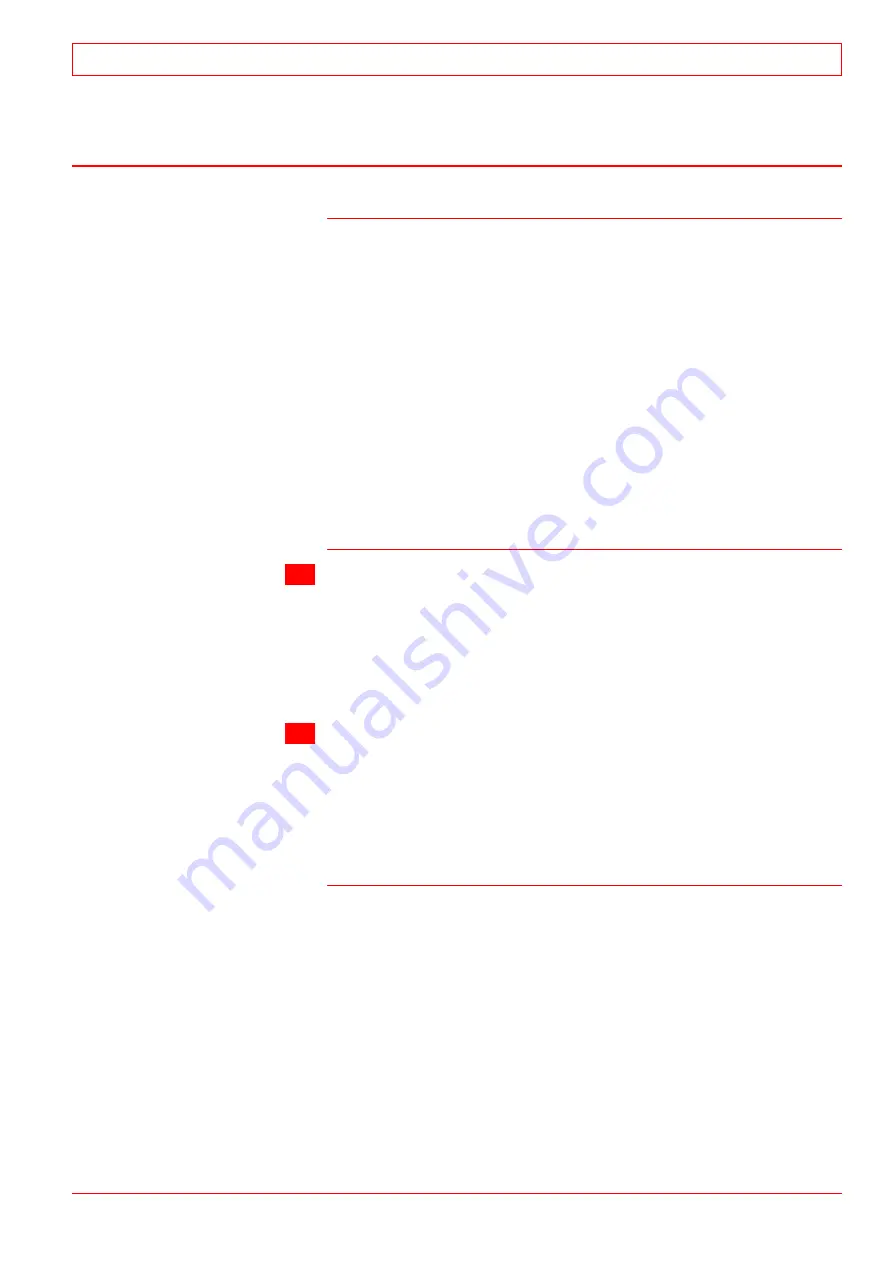
22.5
Electro-pneumatic overspeed trip device
22.5.1 Description (Fig 22-2)
The overspeed trip device is electronically controlled. Air of max.
30 bar is used as operating medium. The tripping speed is 15 %
above the nominal speed.
The three-way solenoid valve (44), Fig 21-4, gets the stop signal
for overspeed from the engine automation system.
When the solenoid valve opens, air is fed to the three-way valve,
which conveys pressure air to the cylinders (42, Fig 21-4), one for
each injection pump. The piston of the air cylinder actuates on
the fuel rack moving it to stop position.
The stop signal is energized long enough to stop the engine
completely. When de-energized, the air is evacuated through the
three-way valve.
The solenoid valve (44) can also be operated manually.
22.5.2 Check and adjustment of stop position
a)
Check of stop position
·
Set the stop lever in the work position and the terminal shaft
lever in the max. fuel position.
·
Press the STOP-button on the engine. (Stop sequence is
activated approximately 1 min.)
Note! The starting air
supply should be open.
·
Check that the fuel rack positions is less than 5 mm.
b)
Adjustment of stop position
·
The electro-pneumatic overspeed trip device requires no adjust-
ment.
·
If a fuel rack position of less than 5 mm cannot be obtained,
check for wear.
22.5.3 Check of tripping speed
The tripping speed can be checked in two different methods,
simulating the engine speed signal by using a signal generator or
by running the engine and increasing the engine speed. The
recommended method is to use a signal generator, see chapter
23., section 23.3.
Increasing engine speed
Check the tripping speed at idle by increasing the engine speed
above the nominal speed by slowly bending the lever (12) with a
suitable wrench in direction from the engine. When the nominal
speed is reached and exceeded, the governor begins to decrease
the fuel setting, i.e. the control shaft must be bended against the
governor force.
32-200636-01
Control Mechanism
22
WÄRTSILÄ 32
22 - 7
Содержание PAAE051728
Страница 4: ......
Страница 18: ...Appendix B Welding Precautions 200640 00 6...
Страница 26: ...01 Main Data Operating Data and General Design 32 200634 01 01 8 W RTSIL 32...
Страница 60: ...Appendix A Environmental Hazards 200507 02A 10...
Страница 68: ...Page 7 7 Document No 4V92A0645 Rev j...
Страница 84: ...03 Start Stop and Operation 32 200402 04 03 12 W RTSIL 32...
Страница 98: ...04 Maintenance Schedule 32 200623 01 04 14 W RTSIL 32...
Страница 154: ...07 Tightening Torques and Use of Hydraulic Tools 32 200643 01 07 30 W RTSIL 32...
Страница 162: ...08 Operating Troubles Emergency Operation 32 200402 01 08 8 W RTSIL 32...
Страница 164: ...Specific Installation Data 2005 01 09 2...
Страница 178: ...10 Engine Block with Bearings Oil Sump and Cylinder Liner 32 200150 10 14 W RTSIL 32 34SG...
Страница 216: ...Appendix A Testing of cylinder tightness 32 200142 A 4 W rtsil 20 32 34...
Страница 226: ...13 Camshaft Driving Gear 32 200546 02 13 10 W RTSIL 32...
Страница 253: ...U tube manometer Fig 15 12 401508200050 32 200549 10 Turbocharging and Air Cooling 15 W RTSIL 32 15 19...
Страница 254: ...15 Turbocharging and Air Cooling 32 200549 10 15 20 W RTSIL 32...
Страница 274: ...16 Injection System 32 200627 01 16 20 W RTSIL 32...
Страница 280: ...Fuel System 32 200508 07 17 6 W RTSIL 32...
Страница 314: ...19 Cooling Water System 32 200050 19 14 W RTSIL 32...
Страница 394: ...23 Instrumentation and Automation 32 200115 II 23 60 W RTSIL 32...