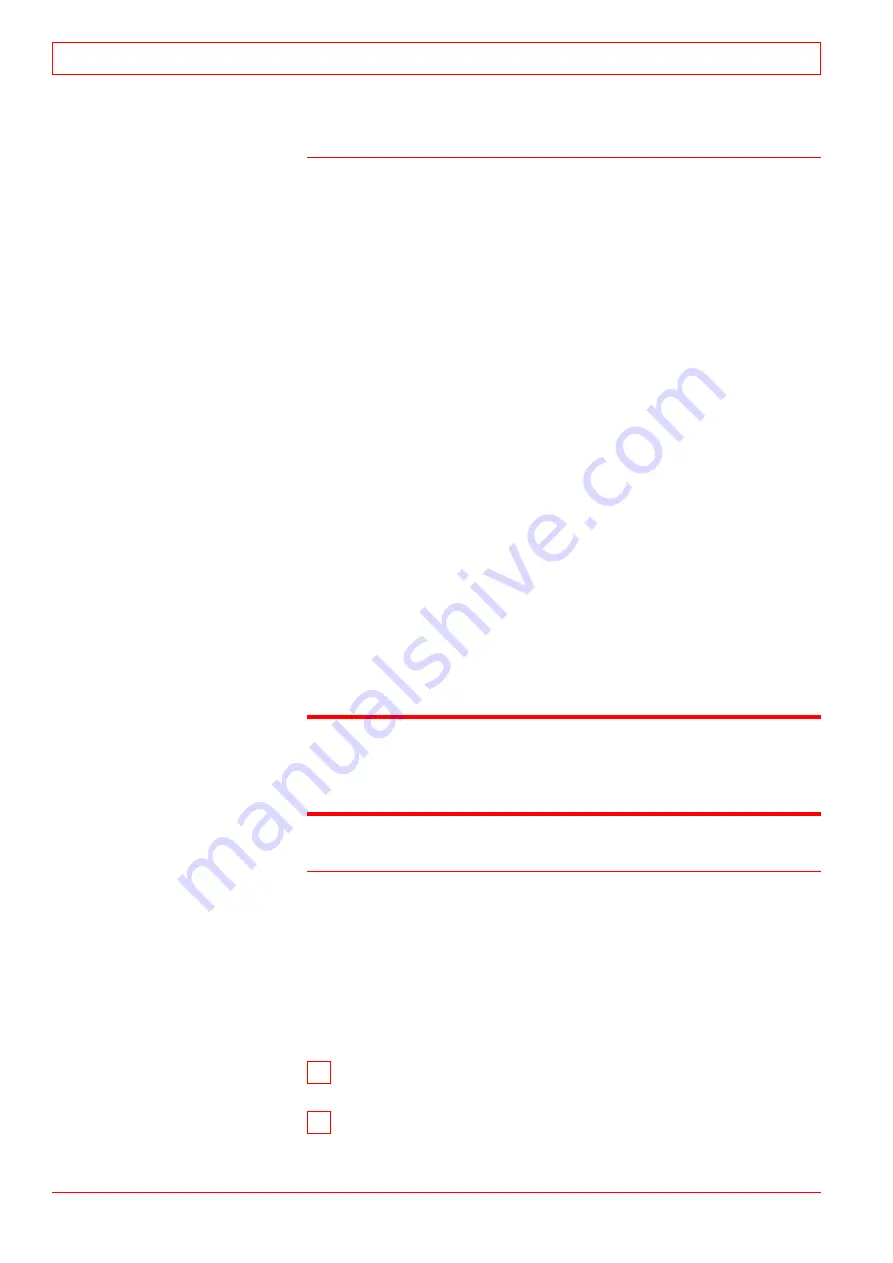
14.1.2 Function
The movement of the valve tappets (9) is governed by the cam
profile on the camshaft. The valve tappets transfer the movement
through push rods (6) to the rocker arms (2). The rocker arms
operate the inlet and exhaust valves through a yoke (4).
The bracket (5) for the rocker arms is fastened to the cylinder
head by three long screws (1). The shaft is positioned by one fixing
screw (1) in the bracket. The positioning of the shaft is essential
for the oil supply.
The adjusting screws in the rocker arms act on the valve yokes,
which are guided by an yoke pin. To compensate for heat expan-
sion a clearance, valve clearance, must exist in the valve mecha-
nism. All adjustments are made on a cold engine, and this
adjusting procedure is explained in chapter 12. Each valve yoke
operates two valves simultaneously, one for inlet and one for
exhaust.
The valve mechanism is lubricated from the main flow through
oil drilling’s. Oil to the valve yokes (4) and to push rod upper bull
joint passes through the rocker arm bracket (5) in an intermittent
flow controlled by the drilling’s in the rocker arm and shaft. The
rocker arm is in position to supply oil only when it is in the “open
valve” position. When the rocker arm is in "valve closed" position
is the surface between rocker arm and shaft lubricated. Oil which
is passed to the yoke is lubricating the yoke guidance and through
the drilling’s also lubricates the valve rotators. Oil is returned to
the crankcase in a free flow through the protecting pipes (7) for
the push rod.
Note!
The intermittent oil flow will cause an optimized oil flow to the
valve mechanism. To completely check the oil flow to a
cylinder head, the engine must be cranked during prelubrica-
tion.
14.1.3 Maintenance of valve mechanism
Normally, the valve mechanism need no maintenance, but inspec-
tion of the components and check for wear should be made at
intervals stated in chapter 04. See chapter 06. for adjustments
and wear limits. If the valve mechanism is dismantled, the
components should be marked and later assembled in the same
position and cylinder as before to avoid unnecessary wear.
14.1.3.1 Dismantling of valve mechanism
1 Open the upper cover for
the cylinder head and remove
the camshaft cover from the cylinder concerned.
2 Turn the crankshaft
to a position where the valve tappet
rollers of the valves are on the base circle of the cam.
14
Valve Mechanism and Camshaft
32-200106
14 - 2
WÄRTSILÄ 32
Содержание PAAE051728
Страница 4: ......
Страница 18: ...Appendix B Welding Precautions 200640 00 6...
Страница 26: ...01 Main Data Operating Data and General Design 32 200634 01 01 8 W RTSIL 32...
Страница 60: ...Appendix A Environmental Hazards 200507 02A 10...
Страница 68: ...Page 7 7 Document No 4V92A0645 Rev j...
Страница 84: ...03 Start Stop and Operation 32 200402 04 03 12 W RTSIL 32...
Страница 98: ...04 Maintenance Schedule 32 200623 01 04 14 W RTSIL 32...
Страница 154: ...07 Tightening Torques and Use of Hydraulic Tools 32 200643 01 07 30 W RTSIL 32...
Страница 162: ...08 Operating Troubles Emergency Operation 32 200402 01 08 8 W RTSIL 32...
Страница 164: ...Specific Installation Data 2005 01 09 2...
Страница 178: ...10 Engine Block with Bearings Oil Sump and Cylinder Liner 32 200150 10 14 W RTSIL 32 34SG...
Страница 216: ...Appendix A Testing of cylinder tightness 32 200142 A 4 W rtsil 20 32 34...
Страница 226: ...13 Camshaft Driving Gear 32 200546 02 13 10 W RTSIL 32...
Страница 253: ...U tube manometer Fig 15 12 401508200050 32 200549 10 Turbocharging and Air Cooling 15 W RTSIL 32 15 19...
Страница 254: ...15 Turbocharging and Air Cooling 32 200549 10 15 20 W RTSIL 32...
Страница 274: ...16 Injection System 32 200627 01 16 20 W RTSIL 32...
Страница 280: ...Fuel System 32 200508 07 17 6 W RTSIL 32...
Страница 314: ...19 Cooling Water System 32 200050 19 14 W RTSIL 32...
Страница 394: ...23 Instrumentation and Automation 32 200115 II 23 60 W RTSIL 32...