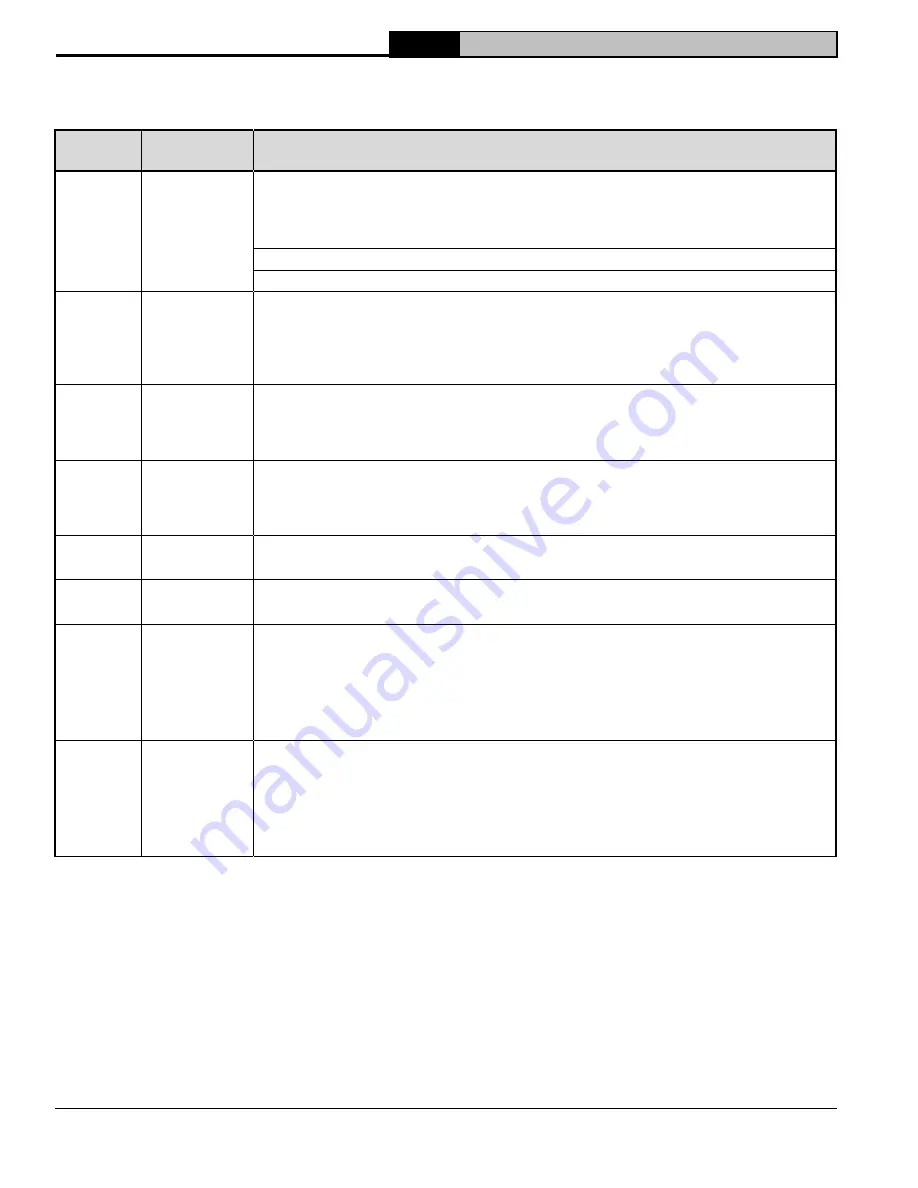
60
110332-04 - 2/23
PHTM II
Installation, Operating & Service Instructions
15
Operation
(continued)
Table 15-12: Menu
FR
FR
, Firing Rate (visible only after password entered)
Default
Range/ Choices
Parameter and Description
Off
On/Off
F01
F01
Manual Modulation Enable
Setting to "On" allows technician to fire at rate specified in
F02
. To return to Auto change
setting to "Off". Note: Boiler will remain in Manual modulation for 15 minutes after last
F02
adjustment. After 15 minutes boiler automatically returns to Auto modulation.
On
Manual
Off
Auto
100%
0-100%
F02
F02
Manual Modulation
Firing rate used when
F01
is set to "On". Note: Manual Modulation will not rise above a specific
priority's max modulation or go below minimum modulation. For example, when set to 0%,
boiler ramps to minimum modulation and when set to 100% with a CH priority, boiler ramps to
CH Max modulation.
100%
0-100%
F03
F03
Central Heat 1 Max Modulation
Defines highest modulation rate during a CH1 demand, Heat T'stat input. If rated input of
installed home radiation is less than maximum output of boiler, change
F03
setting to limit
boiler output accordingly.
100%
0-100%
F04
F04
Central Heat 2 Max Modulation
Defines highest modulation rate during a CH2 demand, Aux T'stat input (when selected). If
rated input of installed home radiation is less than the maximum output of the boiler, change
F04
setting to limit boiler output accordingly.
100%
0 - 100%
F05
F05
DHW Max Modulation
Defines highest modulation rate during a DHW demand.
0%
0 - 30%
F06
F06
Minimum Modulation Capacity
Increases lowest modulation rate during any call for heat , Aux T'stat input (when selected).
0%
120
-9% to +8%
120 (B)
-9% to +8%
150 + 180
-9% to +3%
F07
F07
Gas Valve Ignition Capacity
Increases or decreases gas valve position during burner ignition. For example, increasing this
value causes gas valve to be more open (more fuel) during ignition.
0%
120
-16% to +14%
120 (B)
-16% to +14%
150 + 180
-8% to +14%
F08
F08
Blower Ignition Capacity
Increases or decreases blower speed during burner ignition. For example, increasing this
value causes the blower speed to be higher (more air) during ignition.
Содержание PHTM2080H
Страница 101: ...101 110332 04 2 23 PHTM II Installation Operating Service Instructions SERVICE RECORD SERVICE PERFORMED DATE...
Страница 102: ...102 110332 04 2 23 PHTM II Installation Operating Service Instructions SERVICE RECORD SERVICE PERFORMED DATE...
Страница 103: ...103 110332 04 2 23 PHTM II Installation Operating Service Instructions SERVICE RECORD SERVICE PERFORMED DATE...