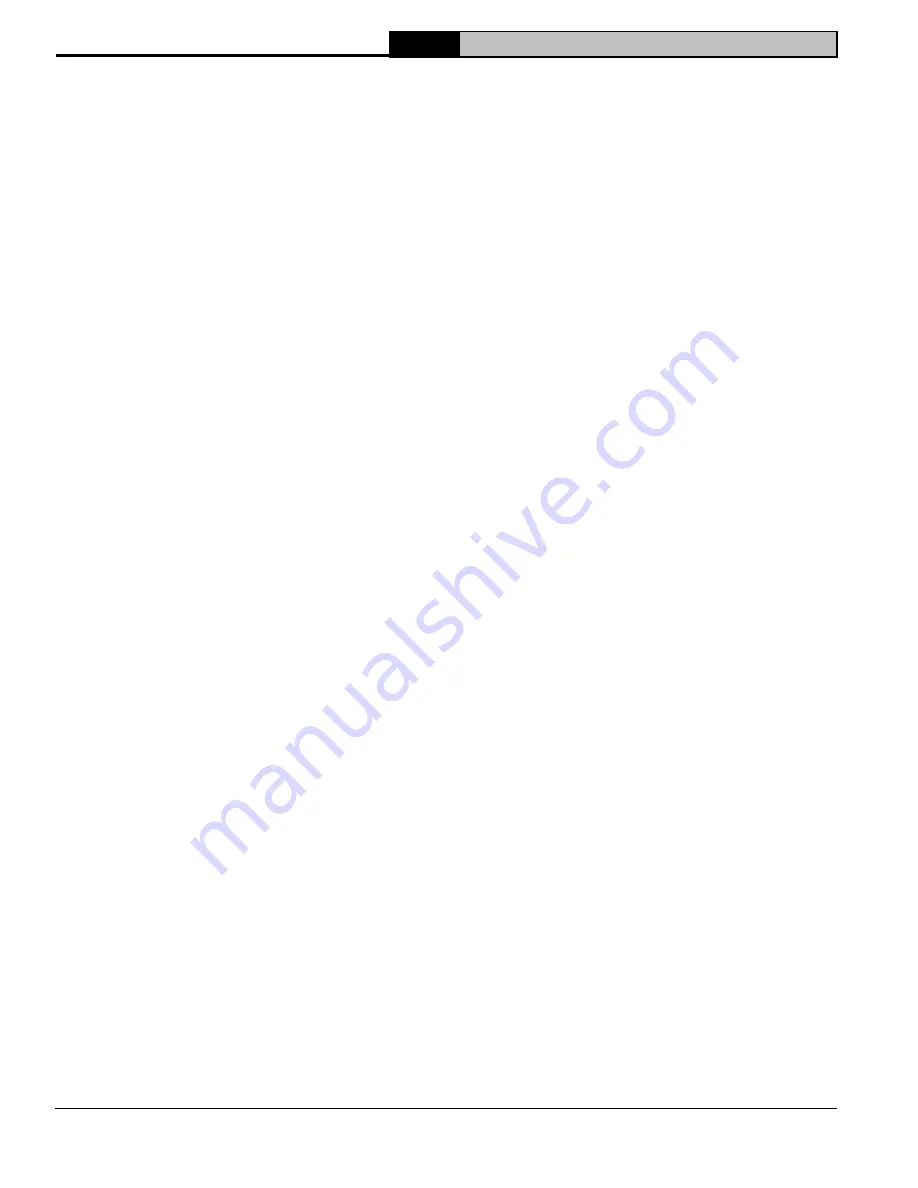
38
110332-04 - 2/23
PHTM II
Installation, Operating & Service Instructions
10
Heating System Piping
(continued)
5. Automatic air vent (required)
Manual air vents are required to remove air during
initial fill.
6. Manual reset high limit (required by some codes
i.e. ASME CSD-1)
A. Install high limit in boiler supply piping just
above boiler with no intervening valves.
B. Set manual reset high limit to 200°F. Wire
limit to "external limit" terminal on low voltage
connection board per Section 12 Field Wiring.
7. Isolation valves are useful when boiler must be
drained, as they will eliminate having to drain and
refill entire system.
8. Dirt and magnetic filter (strongly recommended)
A. Install a dirt/magnetic filter to prevent any
system debris from entering boiler and
fouling of water passages.
B. Note that some filters have a significant
pressure drop, which may impact ability of
system pump to obtain required flow.
9. Drain valve (required)
Install drain valve as shown in Figures 10-3
and 10-4.
10. Low water cut-off (LWCO) (may be required by
local jurisdiction)
A. Protection of this boiler against low water and/
or inadequate flow is provided by UL353
listed flow switch built into boiler.
B. This is a water tube boiler and this flow switch
is therefore only effective way to provide
such protection.
C. Section HG614(c) of ASME Boiler and
Pressure Vessel Code recognizes use of a
listed flow switch in lieu of LWCO on water
tube boilers.
D. In event a local jurisdiction insists upon
installation of LWCO with this boiler, refer
to Section 12 Field Wiring and LWCO
manufacturer's instructions for proper wiring.
•
Auto reset LWCO: 105591-01
•
Manual reset LWCO: 108182-01
E. Install LWCO in supply piping at point
prescribed by the local jurisdiction (generally
at a point above boiler, in common header
piping).
F. If probe type LWCO is used, be certain that it
is located at a point in piping from which air
can escape to an automatic air vent.
G. Generally, this means there should be no
down-turns in piping between LWCO
and point where automatic air vent is
installed.
H. Failure to do this may result in nuisance boiler
shut-downs due to small amounts of air
trapped around probe.
11. Primary-secondary piping is required for this
boiler.
12. Near boiler piping supplied with boiler. See Figure
10-5 for more details.
3. Fill valve (required)
A. Either a manual or automatic fill valve may
be used, but a manual valve is preferred
because it eliminates unmonitored additions
of make-up water to the system.
B. Ideal location for fill valve is at expansion
tank.
C. If using antifreeze with automatic fill valve,
it is recommended to install a water meter
to monitor make-up water. Antifreeze
concentration will decrease as make-up water
is added. If using antifreeze, local codes often
require a backflow preventer or disconnect
from city water.
4. Expansion tank (required)
A. If this boiler is replacing an existing boiler with
no other changes in system, old expansion
tank can generally be reused.
B. If expansion tank must be replaced, consult
expansion tank manufacturer's literature for
proper sizing.
C. If using antifreeze, account for additional
expansion of glycol solution when sizing
an expansion tank. In a typical residential
heating system, a glycol mixture has an
expansion rate of 1.2 times that of water
alone, therefore a tank for an anti-freeze
system should be at least 1.2 times
greater in size. Antifreeze should be stainless
steel compatible.
Содержание PHTM2080H
Страница 101: ...101 110332 04 2 23 PHTM II Installation Operating Service Instructions SERVICE RECORD SERVICE PERFORMED DATE...
Страница 102: ...102 110332 04 2 23 PHTM II Installation Operating Service Instructions SERVICE RECORD SERVICE PERFORMED DATE...
Страница 103: ...103 110332 04 2 23 PHTM II Installation Operating Service Instructions SERVICE RECORD SERVICE PERFORMED DATE...