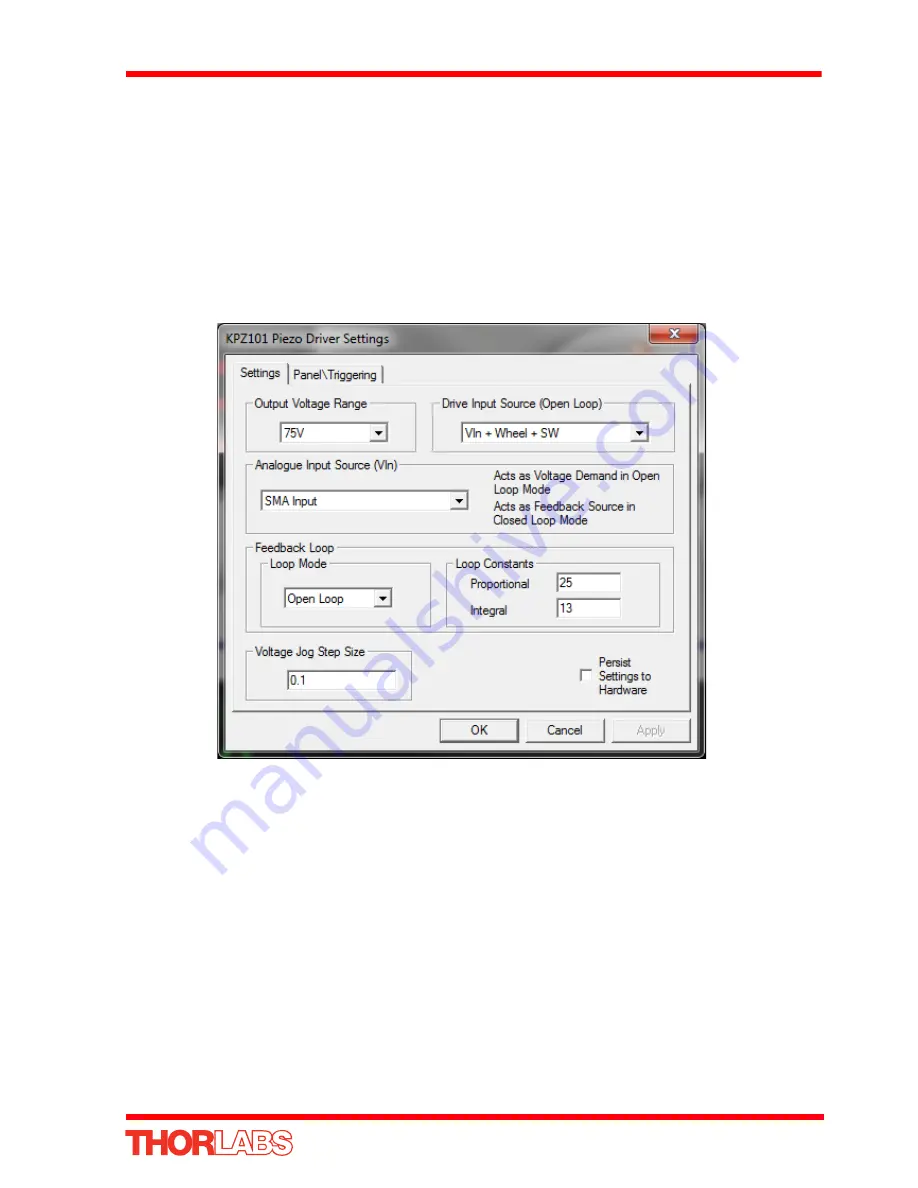
57
K-Cube Piezo Driver
6.2 Settings Panel
When the 'Settings' button on th e GUI pan el is clicked, the 'Settings' window is
displayed. This panel allows data such as jog step size and input sources to be
entered. Note that all of these parameters have programmable equivalents accessible
through the ActiveX methods and properties on this Control (refer to the
Programming
Guide
in the
APTServer helpfile
(accessed via the Windows ‘Start’ menu) for further
details and to Section 2.3.4. for an overview of the APT ActiveX controls).
6.2.1 Settings tab
Fig. 6.1 Settings tab
Output Voltage Range
- use d to set the maxi mum output voltage of the piezo
controller. This must be set up to suit the maximum specified operating voltage of the
piezo actuator connected to the unit. Most Thorlabs piezo actuators are specified for
either 75V or 150V maximum operation. In general, the maximum voltage should not
be exceeded because it can cause damage to the piezo actuator.
The output voltage range can be selected between 75V, 100V and 150V. Of these 3
settings, 75V and 150V are hardware limits: the piezo unit contains an internal
clamping circuit that limits the output voltage to approximately 10% above these
values. (Piezo actuators can tolerate a 10% overvoltage without damage.) The 100V
limit is a software limit: under software control (for example, by turning the ‘Output’
control knob) it is not possible to exceed this limit but using the external inputs (SMA,
Hub channel 1 or Hub channel 2) the limit can be exceeded. Therefore exercise care
when 100V piezo actuators are driven under external input control.