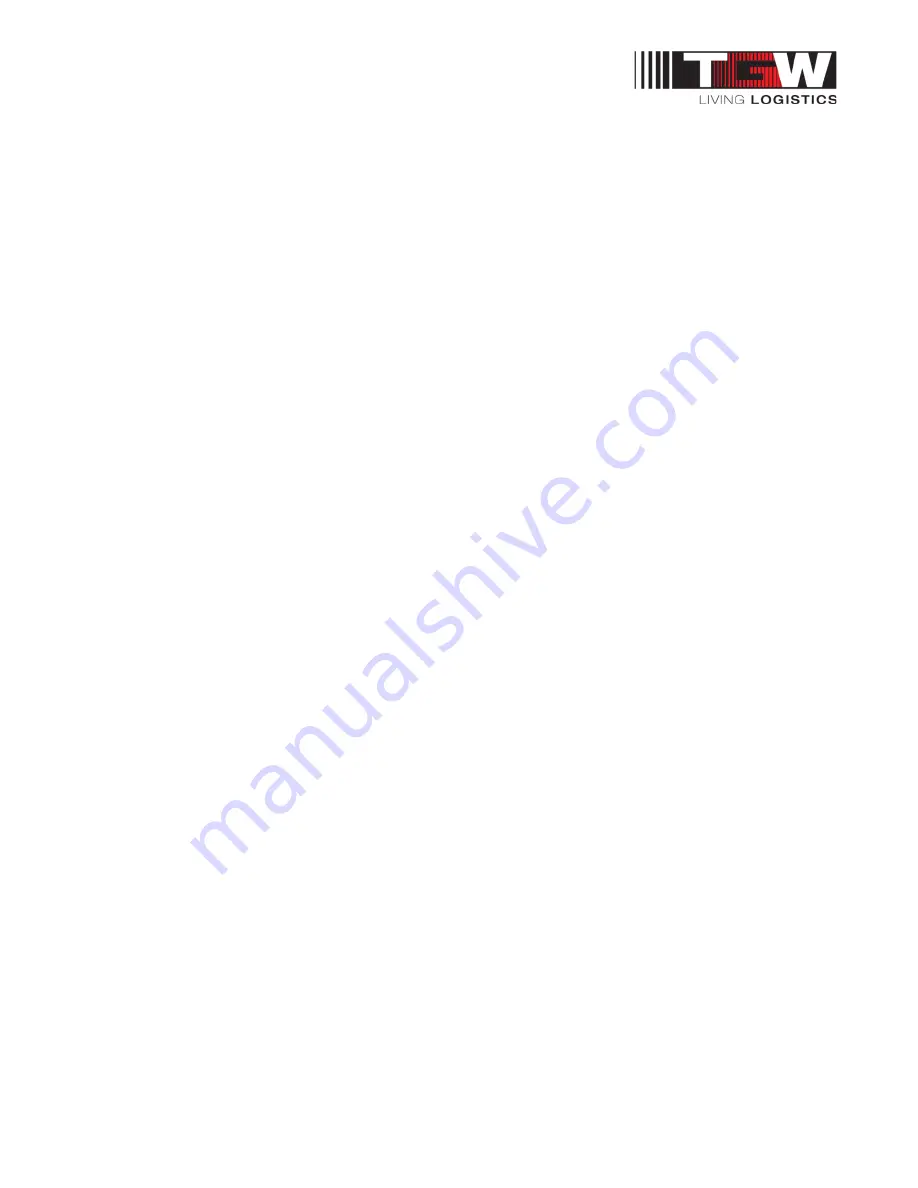
NBC™ Flat Belt - IOM
P/N: 1118140
Rev: 07/29/2020
Page
3
of
129
............................................................................ 48
............................................................................ 55
....................................................................................... 66
...................................................................................... 95
.............................................................................. 111
........................................................................................... 113