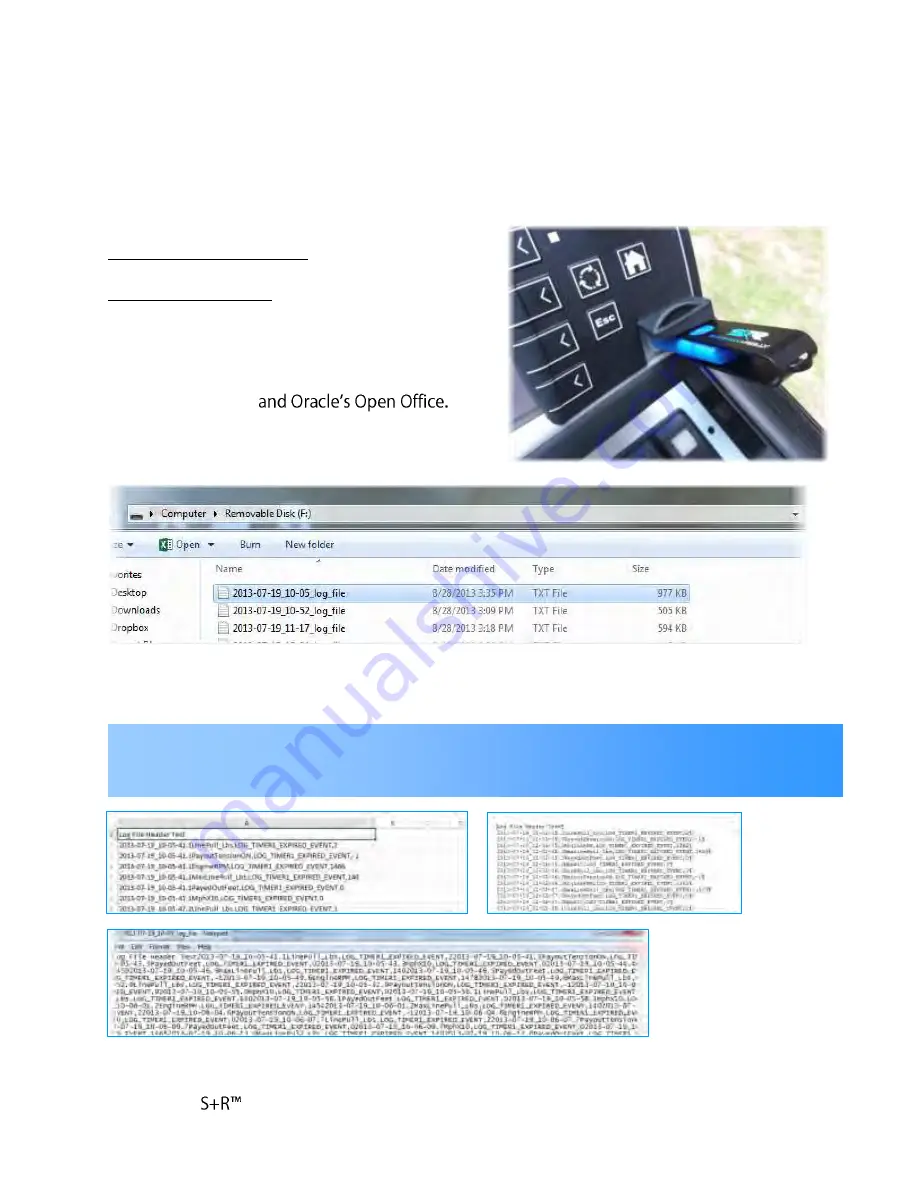
Revolution Series PT-3500 / PT-7500 Puller Tensioner Page 34
Operation
Operator Controls
**For control locations see Operator Control Panel Section on page 20.
System Control Panel
USB Interface (cont.)
Each file saved to the USB drive will be a (.txt-
text) file. These files can be opened with many
computer programs to include: Microsoft Excel,
Windows Note Pad,
The information contained in the file will be displayed in consecutive sequence and time stamped
to the second for which the status/event occurred.
NOTE:
Information within the file may be displayed differently, dependent upon which program the file is opened
with. Microsoft Excel and Word will list the events in a single column by data/time stamp, whereas Note Pad will
display the information in block format- making it difficult to read.
Содержание PT-3500
Страница 1: ...PT 3500 PT 7500 Puller Tensioner Operators Manual...
Страница 2: ......
Страница 6: ......
Страница 9: ......
Страница 22: ...Revolution Series PT 3500 PT 7500 Puller Tensioner Page 20 Operation Operator Controls 2 ReGen Icon PT 3500...
Страница 81: ......
Страница 82: ...S R Revolution Series PT 3500 PT 7500 Puller Tensioner Page 78 Troubleshooting Fuse Relay Wiring Schematic...
Страница 83: ...S R Revolution Series PT 3500 PT 7500 Puller Tensioner Page 79 Troubleshooting...
Страница 84: ...S R Revolution Series PT 3500 PT 7500 Puller Tensioner Page 80 Fuse Relay Wiring Schematic...
Страница 85: ...S R Revolution Series PT 3500 PT 7500 Puller Tensioner Page 80 Troubleshooting PT Trailer Wiring Schematic...
Страница 86: ...S R Revolution Series PT 3500 PT 7500 Puller Tensioner Page 80 Troubleshooting PT Trailer Wiring Schematic...
Страница 87: ...S R Revolution Series PT 3500 PT 7500 Puller Tensioner Page 81 Troubleshooting Hydraulic Schematic 7500...
Страница 88: ...S R Revolution Series PT 3500 PT 7500 Puller Tensioner Page 81 Troubleshooting PT Hydraulic Schematic...
Страница 89: ......
Страница 129: ...Revolution Series PT 3500 PT 7500 Puller Tensioner Page 121...
Страница 131: ...Revolution Series PT 3500 PT 7500 Puller Tensioner Page 123...
Страница 133: ...Revolution Series PT 3500 PT 7500 Puller Tensioner Page 125...
Страница 134: ...Revolution Series PT 3500 PT 7500 Puller Tensioner Page 126 A...