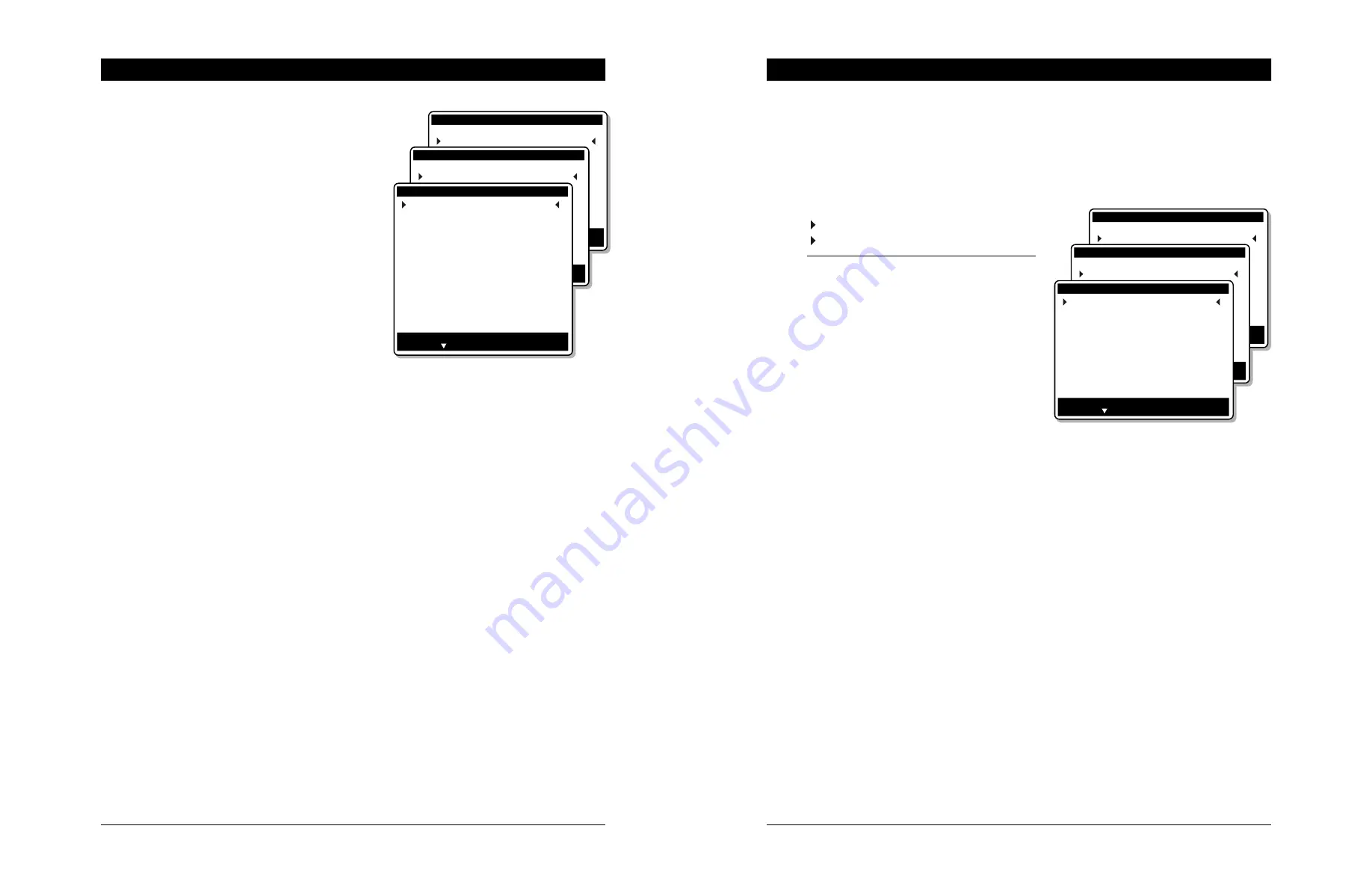
38
ECO II FEEDING rev.06
ECO II FEEDING
Main Menu
10.
Alarm acknowledge
11.
Installation
Installation
2.
Scale settings
3.
Loop settings
Loop settings
Exit: Press BACK
Change: Press Modify
Press to Select an item
Select loop #
1
Loop speed
100 ft/mn
Min distance betwn feeds
25 ft
Loop slip
0 %
Valve open/close time
4 sec
Is flex auger ?
No
Max current
9.5 A
Actual current
0.0 A
Over-current delay
3:00 (m:s)
Prox switch off delay
0:00 (m:s)
Prox switch bypass delay
1:00 (m:s)
Has fill auger ?
Yes
Flex auger Module ID
4
Flex auger Output #
5
Prox switch Module ID
20
Prox switch Output #
6
• Auger Module ID:
Select on which relay panel the flex-
ible auger (or fill auger – if using a
closed loop system) is connected; the
relay panel is identified by its ID num-
ber (ID #4 to ID #19). Tables are avail-
able at the end of this manual to write
down the identification number of each
module.
• Auger Output #:
Select on which relay the auger is con-
nected (relay 1-16). If the output is
connected to relays 17-32 of a 32 out-
put relay panel, select which relay of
the 16-relay strip the output is con-
nected; e.g., relay 17=1, relay 18=2...
relay 32=16. Refer to section 5.9 for
further information
• Loop’s Proximity Switch ID
Select on which PSM-8 module the loop’s proximity switch is connected; the
PSM-8 module is identified by its ID number (ID #20 to ID #44). Tables are
available at the end of this manual to write down the identification number of
each module. For a closed loop system, this proximity switch is located in the
fill auger’s control box.
• Loop’s Proximity Switch’s Input Number
Select on which input of the PSM-8 module the loop’s proximity switch is
connected (input 1-8).
39
ECO II FEEDING rev.06
ECO II FEEDING
5.7
Bin Settings
This section describes how to customize the bins for your particular application. The
controller can monitor up to 4 bins. Refer to section 5.3 to enable the number of bins
in use.
Select
11. Installation *
4. Bin Settings
* Only accessible from the installer mode (s. 5.2).
• Select a bin
The following parameters are associ-
ated with the chosen bin and must be
set separately for each bin in use.
• Max Fill Time (Empty bin alarm):
Maximum time that is required to com-
pletely fill the scale hopper. An alarm
is set off whenever the filling time
exceeds this delay. This type of alarm
usually occurs when a bin is empty.
The maximum filling time can be
adjusted from 1 to 10 minutes.
• Reorder point:
This is minimum allowable amount of feed in a bin. An alarm can be set off it
the amount of feed decreases below this level. Note that the feeding system
keeps on running when this type of alarm occurs. To disable this type of alarm,
decrease the re-order point limit until the word “None” is reached.
• Bin’s Module ID:
Select on which relay panel the bin auger is connected; the relay panel is
identified by its ID number (ID #4 to ID #19). Tables are available at the end of
this manual to write down the identification number of each module.
• Bin’s Output #:
Select on which relay the bin auger is connected (relay 1-16). If the output is
connected to relays 17-32 of a 32 output relay panel, select on which relay of
the second 16-relay strip the output is connected; e.g., relay 17=1, relay
18=2... relay 32=16. Refer to section 5.9 for further information
Main Menu
10.
Alarm acknowledge
11.
Installation
Installation
3.
Loop settings
4.
Bin settings
Bin settings
Exit: Press BACK
Change: Press Modify
Press to Select an item
Select Bin #
1
Max fill time
5
Module ID
4
Output #
1
Re-Order point
65 kg