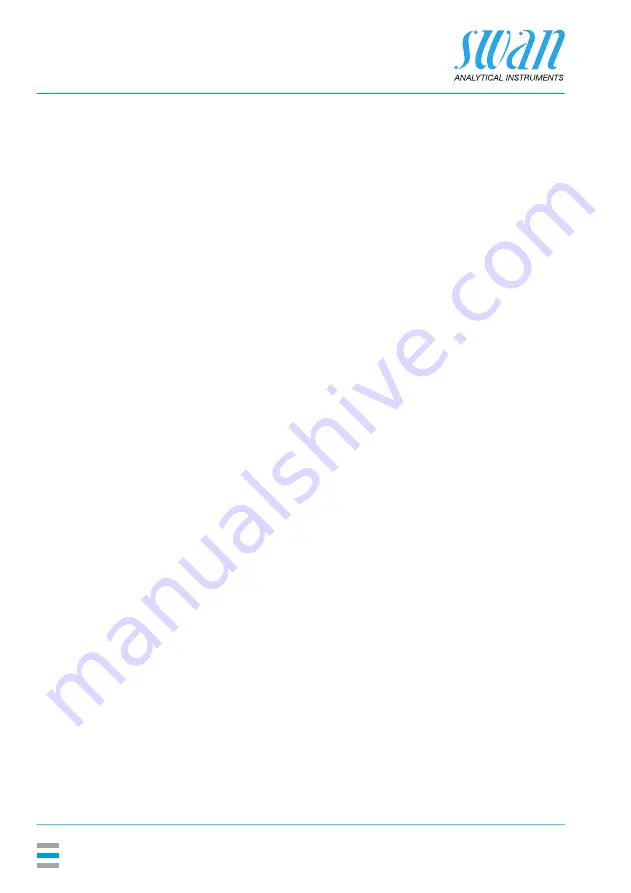
A-96.250.511 / 091120
AMI Turbiwell
Maintenance
74
6.6. Longer Stop of Operation
Do not switch off the instrument if your operation is suspended for
less than a week. Power consumption is very low and the turbidime
-
ter remains ready for use.
If water hardness is very high, lime deposition may precipitate.
1
Stop sample flow.
2
Switch off power.
3
Empty measuring chamber by opening the drain valve. (With
automatic drain valve option, select <Maintenance>/<Drainage>/
<Manual operation>/<Motor valve>/<open> menu item).
4
If necessary clean the measuring chamber (see
).
Содержание AMI Turbiwell
Страница 1: ...Operator s Manual Firmware V6 23 and higher AMI Turbiwell A 96 250 511 091120 ...
Страница 35: ...A 96 250 511 091120 AMI Turbiwell Installation 35 Degasser G B C Degasser sample inlet Drain Waste B G C ...
Страница 108: ...A 96 250 511 091120 AMI Turbiwell Notes 108 12 Notes ...
Страница 109: ...A 96 250 511 091120 AMI Turbiwell Notes 109 ...