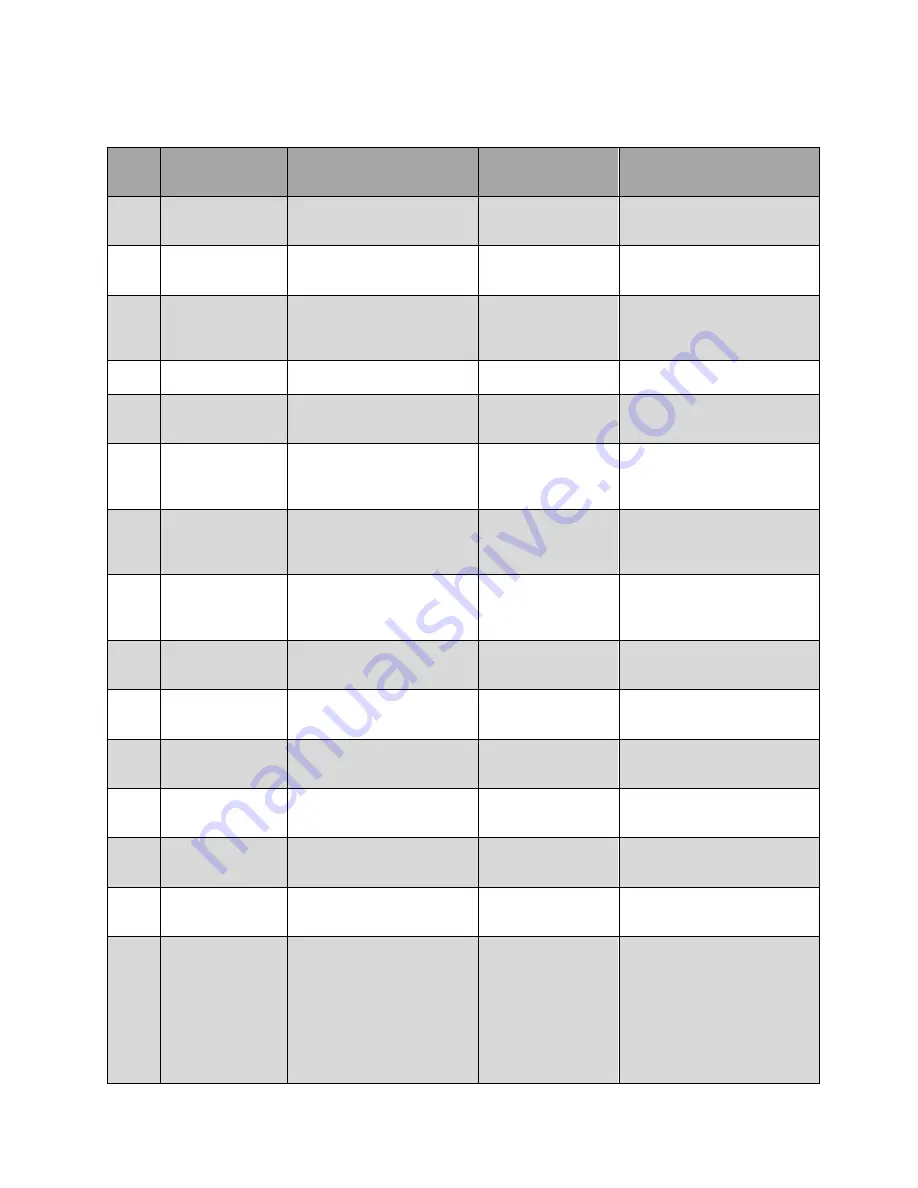
86
14.3 Lockout codes
Lock
out
code
Error
Description
Cause
Solving
0
E2PROM_READ
_ERROR
Internal software error
wrongly
programmed PCB
or PB
reset PCB or replace PCB
and or display unit
1
IGNIT_ERROR
Five unsuccessful ignition
attempts in a row
no gas, wrongly
adjusted gas valve
check gas supply and
adjust gas valve, reset
PCB
2
GV_RELAY_
ERROR
Failure detected in the gas
valve relay
short circuit in coil
of the gas valve,
water on wiring or
gas valve
reset PCB replace gas valve
or wiring harness
3
SAFETY_RELAY
_ERROR
Failure detected in safety
relay
safety relay is not
working correctly
reset PCB or replace PCB
4
BLOCKING_
TOO_LONG
Control had a blocking error
for more than 20 hours
blocking code
active for more than
20 hours
reset and check blocking
code
5
FAN_ERROR_
NOT_RUNNING
Fan is not running for more
than 60 seconds
electrical wiring not
correctly
connected, or Fan
is malfunctioning
Check wiring or replace Fan
if not solved check fuse on
PCB or replace PCB
6
FAN_ERROR_
TOO_SLOW
Fan runs too slow for more
than 60 seconds
electrical wiring not
correctly
connected, or Fan
is malfunctioning
Check wiring or replace Fan
if not solved check fuse on
PCB or replace PCB
7
FAN_ERROR_
TOO_FAST
Fan runs too fast for more
than 60 seconds
electrical wiring not
correctly
connected, or Fan
is malfunctioning
Check wiring or replace Fan
if not solved check fuse on
PCB or replace PCB
8
RAM_ERROR
Internal software error
wrongly
programmed PCB
or PB
reset PCB or replace PCB
and or display unit
9
WRONG_EEPR
OM_SIGNATUR
E
Contents of E2prom is not
up to date
out dated E2prom
reset PCB or replace PCB
10
E2PROM_
ERROR
Wrong safety parameters in
E2prom
wrongly
programmed PCB
or PB
reset PCB or replace PCB
11
STATE_ERROR Internal software error
wrongly
programmed PCB
or PB
reset PCB or replace PCB
12
ROM_ERROR
Internal software error
wrongly
programmed PCB
or PB
reset PCB or replace PCB
13
APS_NOT_
OPEN
Air pressure switch not
opening during pre-purge 0
electrical circuit is
short circuited or
APS is jammed
check wiring or replace APS
14
APS_NOT_CLO
SED_IN_PRE_
PURGE
Air pressure switch not
closing during pre-purge 1
no air transport to
the burner; flue or
air inlet is blocked
or APS is jammed
or air signal hose
not connected to
the air intake pipe
or water in hose
Check if there are any
obstructions in the flue or air
intake, replace APS if
jammed, connect air hose to
the air intake pipe, remove
any water from the hose.
Содержание S-CBX 105
Страница 2: ......
Страница 40: ...40 9 10 Flue Terminal Positioning ...
Страница 42: ...42 9 11 1 FIGURE 12 LINE G ...
Страница 55: ...55 11 5 Ladder Logic Diagram ...
Страница 56: ...56 11 6 Electrical schematics ...
Страница 57: ...57 ...
Страница 137: ......