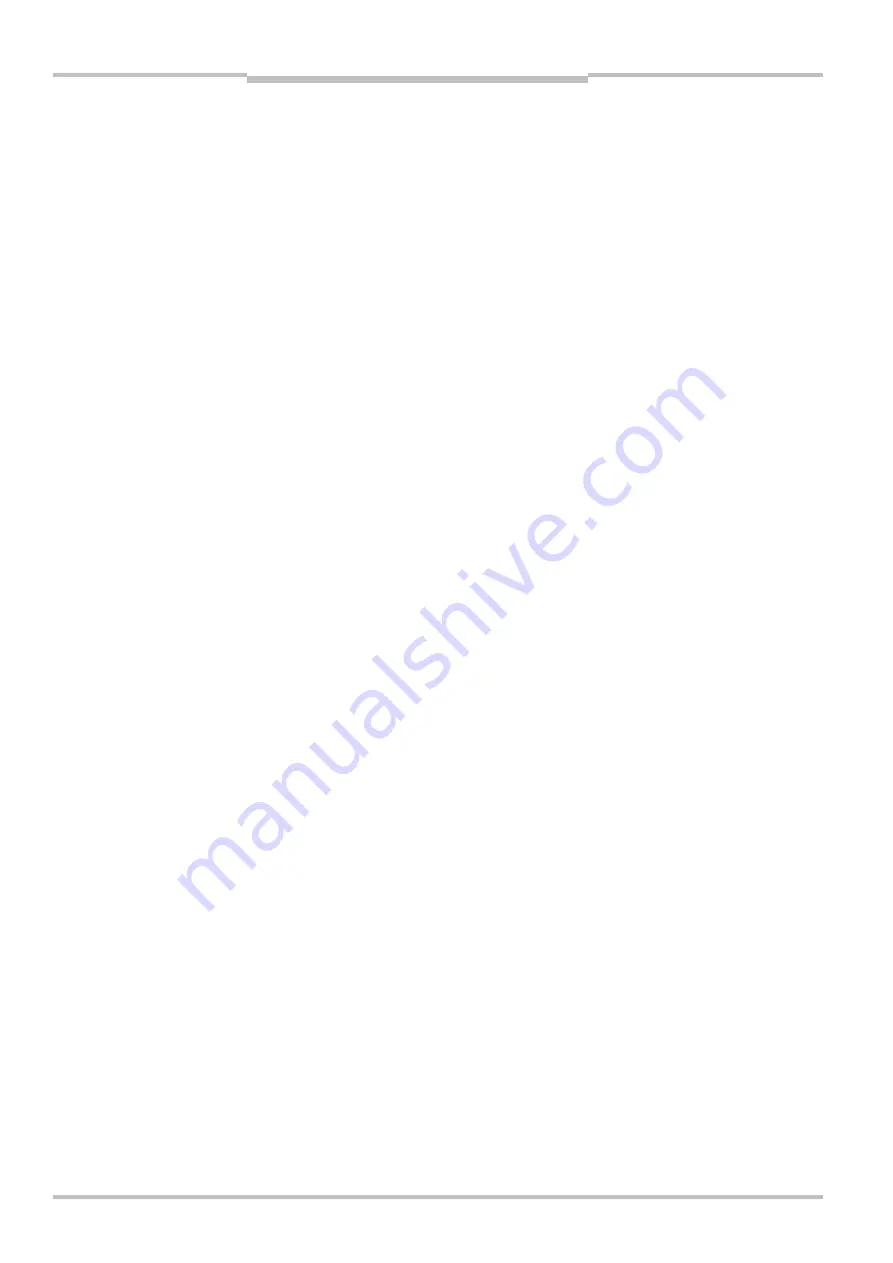
Chapter
5
Operating Instructions
Flexi Soft Gateways
80
© SICK AG • Industrial Safety Systems • Germany • All rights reserved
8012664/XB29/2013-06-11
Subject to change without notice
Ethernet gateways
Define where in the PLC memory the selected data shall be written to or read from:
Enter addresses into the
Holding register address
field (max. 20 characters).
Select
Write all sets in one tag
if all data sets shall be written into one address in the
PLC memory. In this case, the tag/file defined for data set 1 will be used.
For the
Flexi Soft to network
direction, define how often the data shall be transmitted:
– Select
Enable COS update
if the FX0-GMOD is to update the data in the PLC
immediately when changes occur in the data sets.
– Select
Enable heartbeat interval
to activate updating of the selected data sets with
the set Heartbeat rate.
Both options may be selected at the same time.
For the
Network to Flexi Soft
direction, define how often the data shall be read:
– Enter a
Heartbeat rate
to activate updating of the selected data sets with the set
time interval.
Define where the data shall be read from/written to in the Modbus TCP network: Enter
the
PLC IP address
and the Modbus
Device ID
of the PLC.
Max. PLC update rate
defines the maximum rate (the minimum time interval) for send-
ing the data sets to the PLC. Settings occur dependent on the PLC processing speed.
Minimum = 10 ms, maximum = 65,535 ms. The default value of 40 ms is suitable for
most PLCs.
If this value is greater than the
Heartbeat rate
, the heartbeat rate is slowed down to
this value.
Go online and download the configuration to the Flexi Soft system.
Write to PLC
The following restrictions apply when the gateway is master and writes the input data sets
to the PLC:
The input data set address (set via Flexi Soft Designer Tool) must be the same as that
defined on the PLC.
The variable to receive the data on the PLC must be:
– in the 40xxxx address range (for Schneider Modicon type PLCs)
– an array of 16 bit words
– long enough to contain the specified input data set array.
All input data sets are transferred to the PLC in 16 bit word format with the first byte
placed in the least significant, or rightmost byte of the integer and the second byte
placed in the most significant, or leftmost byte of the integer.
Read from PLC
The following restrictions apply when the gateway is master and reads the output data sets
from the PLC:
The output data set addresses must be the same as those defined on the PLC.
The variables to request the data on the PLC must be:
– in the 40xxxx address range (for Schneider Modicon type PLCs)
– for the output data set settings, an array of 16 bit words long enough to contain the
entire output data set.
All output data sets are transferred from the PLC in 16 bit word format and the first byte
must be placed in the least significant, or rightmost byte of the integer and the second
byte placed in the most significant, or leftmost byte of the integer.
Note
Note
Note