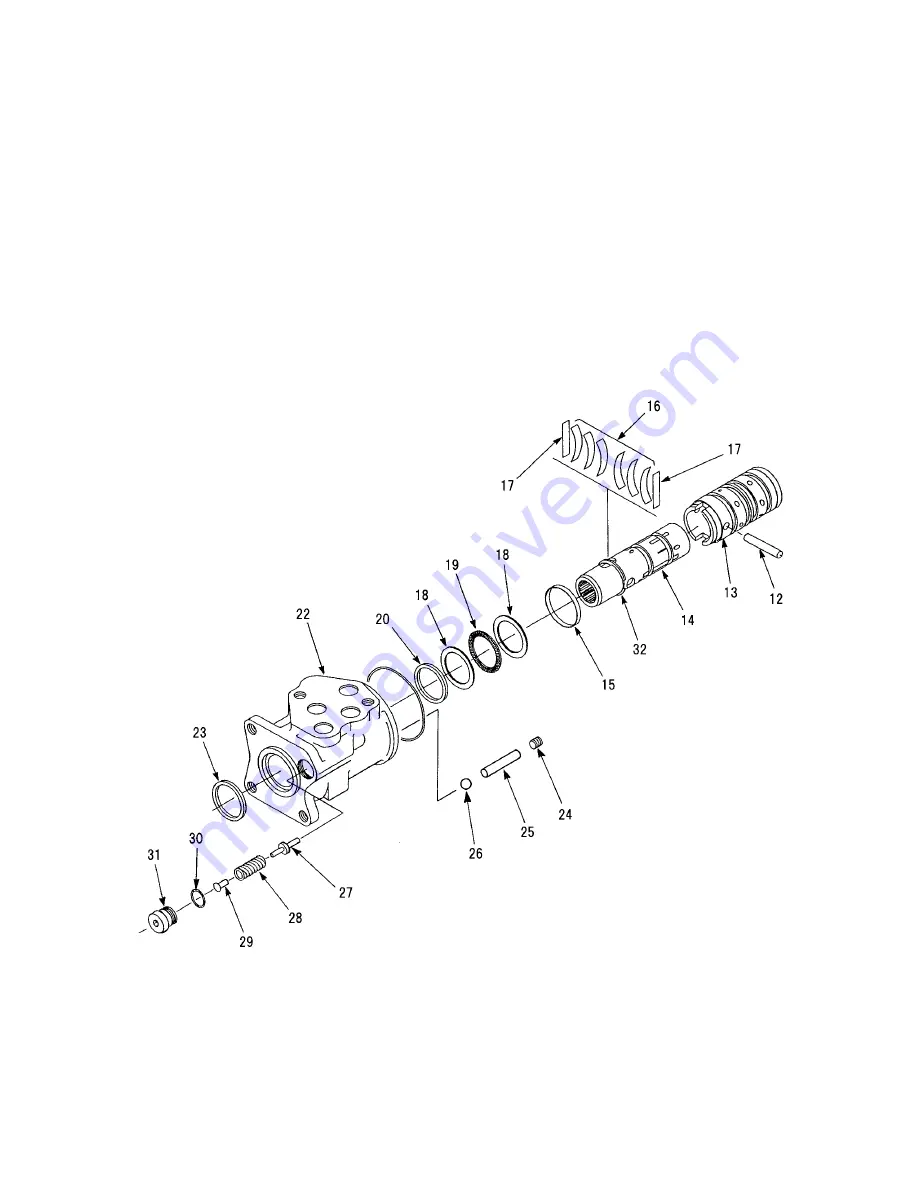
180
11. Remove the retaining ring (15) and pin (12) from the
spool and sleeve assembly.
12. Slide out the spool (14) a little from the sleeve (13)
and remove the centering springs (16) and flat springs
(17) from the spool.
13. Remove the sleeve (13) from the spool while rotate is
slowly.
NOTE: Never remove the retaining ring (32) from
the spool.
14. Remove the bearing laces (18), thrust needle bearing
(19), oil seal (20) and dust seal (23) from the housing
(22).
15. Remove the retainer screw (24), retainer pin (25) and
steel ball (26) from the housing.
16. Measure the depth of the relief adjust plug (31) from
the housing surface before remove it.
NOTE:
•
Do not remove the relief valve from the housing
unnecessary.
•
If removed, need adjust the relief pressure after
installed to the tractor.
17. Remove the relief adjust plug (31) and remove the
O-ring (30) from the plug.
18. Remove the damper collar (29), spring (28) and
poppet (27).
T616
Содержание ST318
Страница 1: ......
Страница 4: ...3 Chapter 1 GENERAL...
Страница 27: ...26...
Страница 28: ...27 Chapter 2 ENGINE Tractor Model Engine Model ST318 S753 ST321 S773 ST324 S773L...
Страница 29: ...28 2 1 Engine Sectional View T100 T101...
Страница 48: ...47 13 Oil flow T140...
Страница 98: ...97 Chapter 3 TRACTOR MAIN BODY...
Страница 115: ...114 3 3 Transmission 1 9 3 MANUAL TRANSMISSION 1 Sectional view z Without Mid PTO T447 z With Mid PTO T447...
Страница 132: ...131 2 HYDROSTATIC TRANSMISSION 1 SPEED PTO MID PTO 1 Sectional view T505 T506...
Страница 154: ...153 Take out the swash plate from the case T566...
Страница 163: ...162 2 Range shift change lever Rear PTO change lever Mid PTO change lever and 4WD change lever T588...
Страница 194: ...193 Model 9 3 shown...
Страница 199: ...198 4 CONTROL VALVE 1 Control valve relief valve 340013400 1 Name of components T658...
Страница 203: ...202 2 Control valve for lifting lowering implement 340016110 1 Name of components T667...
Страница 223: ...221...
Страница 224: ...222...
Страница 225: ...223...
Страница 226: ...224...
Страница 228: ...226 4 LIGHTEING CIRCUIT T702...
Страница 229: ...227 5 HORN CIRCUIT T703...
Страница 230: ...228 6 FUEL LEVEL CIRCUIT T704...
Страница 231: ...229 7 ENGINE STOP SOLENOID CIRCUIT T705...
Страница 232: ...230 8 ENGINE COOLANT TEMPERATURE CIRCUIT ENGINE OIL PRESSURE WARNING CIRCUIT T706...
Страница 233: ...231 9 HST CRUISE CONTROL CIRCUIT T707...
Страница 234: ...232 10 PARKING BRAKE WARNING LIGHT CIRCUIT T708...
Страница 235: ...233 11 BRAKE LAMP CIRCUIT T709...
Страница 236: ...234 12 SAFETY START CIRCUIT T710...
Страница 237: ...235 13 FLASHER AND HAZARD LUMP CIRCUIT T711...
Страница 238: ...236 14 GLOW PLUG AND GLOW LAMP CIRCUIT T712...
Страница 239: ...237 15 ALTERNATOR AND ENGINE STOP SOLENOID CIRCUIT T713...