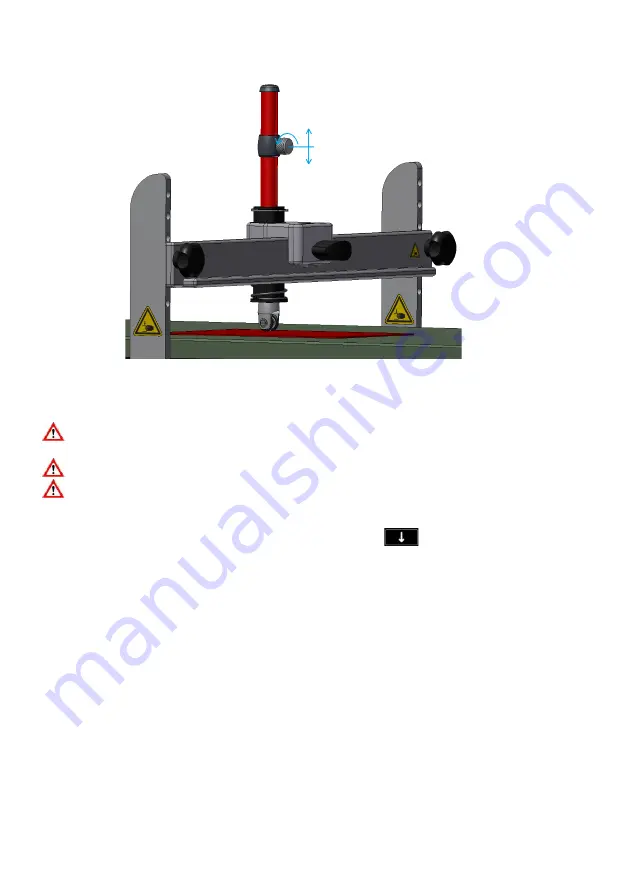
Page 30
•
Set the spring load.
•
Set the stroke length on the display (see chapter 8.1.8
Set the right scratching length: The testing head has to remain on the
sample over the whole stroke length.
Check the correct fit of the scratching set before starting the procedure.
Do not lean over the unit during operation in order to avoid touching the tool
holder (18).
•
Start the scratching test by tapping on the symbol
.
•
Create the evaluation and test report according to the standard.
Содержание ZAA 2600.C
Страница 1: ...Proceq ZAA 2600 C Automatic Crockmeter Instruction Manual...
Страница 2: ......
Страница 13: ...Page 13 4 Device overview 12 13 14 4 1 5 2 11 3 16 9 10 17 7 6 15 8 18...