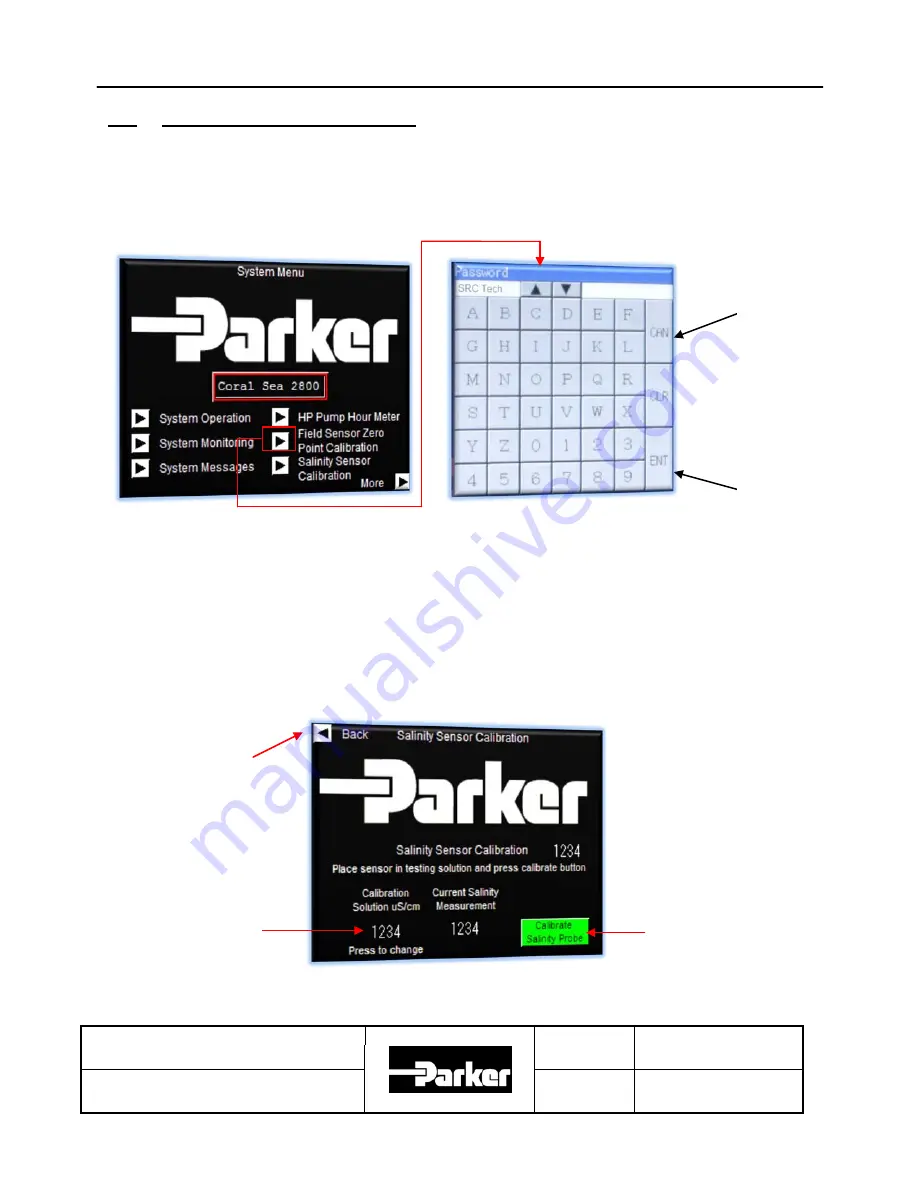
[
CONTROL SYSTEM OPERATIONS MANUAL
]
May, 2015
Project:
Doc:
Version:
Parker Sea Recovery Coral Sea
1010016
01c
Document Name:
Author:
Page:
Control System Operations Manual
AGE
Page 98 of 129
14.2 Performing Salinity Sensor Calibration
To access the salinity sensor calibration screen, press on the arrow next to the text ‘Salinity Sensor
Calibration’ screen. Pressing this button will bring you to the ‘Password Required’ screen as shown
below:
Entry of an incorrect password will result in the password prompt screen remaining visible. The
password you have entered will be erased and the password screen will wait for you to attempt again.
Press the ‘CAN’ key to cancel this request.
Entering the correct password will bring you to the following screen.
Press here to
calibrate sensor
Press here to
enter value
Enter Password
and press here
To cancel
press here
Press Here
To Go Back
Coral Sea Owner's Manual
Содержание Coral Sea
Страница 3: ...SECTION 1 SYSTEM DESCRIPTION Coral Sea Owner s Manual...
Страница 14: ...SECTION 2 PRE INSTALLATION NOTES Coral Sea Owner s Manual...
Страница 25: ...SECTION 3 ELECTRICAL INFORMATION Coral Sea Owner s Manual...
Страница 28: ...SECTION 4 INSTALLATION REQUIREMENTS Coral Sea Owner s Manual...
Страница 34: ...Coral Sea Vertical 6800 Page 4 6 Installation This page is intentionally left blank Coral Sea Owner s Manual...
Страница 35: ...SECTION 5 OPERATIONS MANUAL Coral Sea Owner s Manual...
Страница 36: ...Operation THIS PAGE INTENTIONALLY LEFT BLANK Coral Sea Owner s Manual...
Страница 166: ...Intentionally Left Blank Coral Sea Owner s Manual...
Страница 167: ...SECTION 6 R O MEMBRANE INSTALL CARE Coral Sea Owner s Manual...
Страница 168: ...Coral Sea Vertical 6800 Page 6 ii R O MEMBRANE Page Intentionally Left Blank Coral Sea Owner s Manual...
Страница 193: ...SECTION 7 MAINTENANCE AND REPAIR Coral Sea Owner s Manual...
Страница 194: ...Maintenance Coral Sea Owner s Manual...
Страница 203: ...SECTION 8 COMPONENT USER MANUALS Coral Sea Owner s Manual...
Страница 204: ...Page Intentionally Left Blank Coral Sea Owner s Manual...
Страница 215: ...SECTION 9 DRAWING PULL OUTS Coral Sea Owner s Manual...
Страница 216: ...Page Left Intentionally Blank Coral Sea Owner s Manual...
Страница 247: ...SECTION 10 SPARE PARTS LIST Coral Sea Owner s Manual...