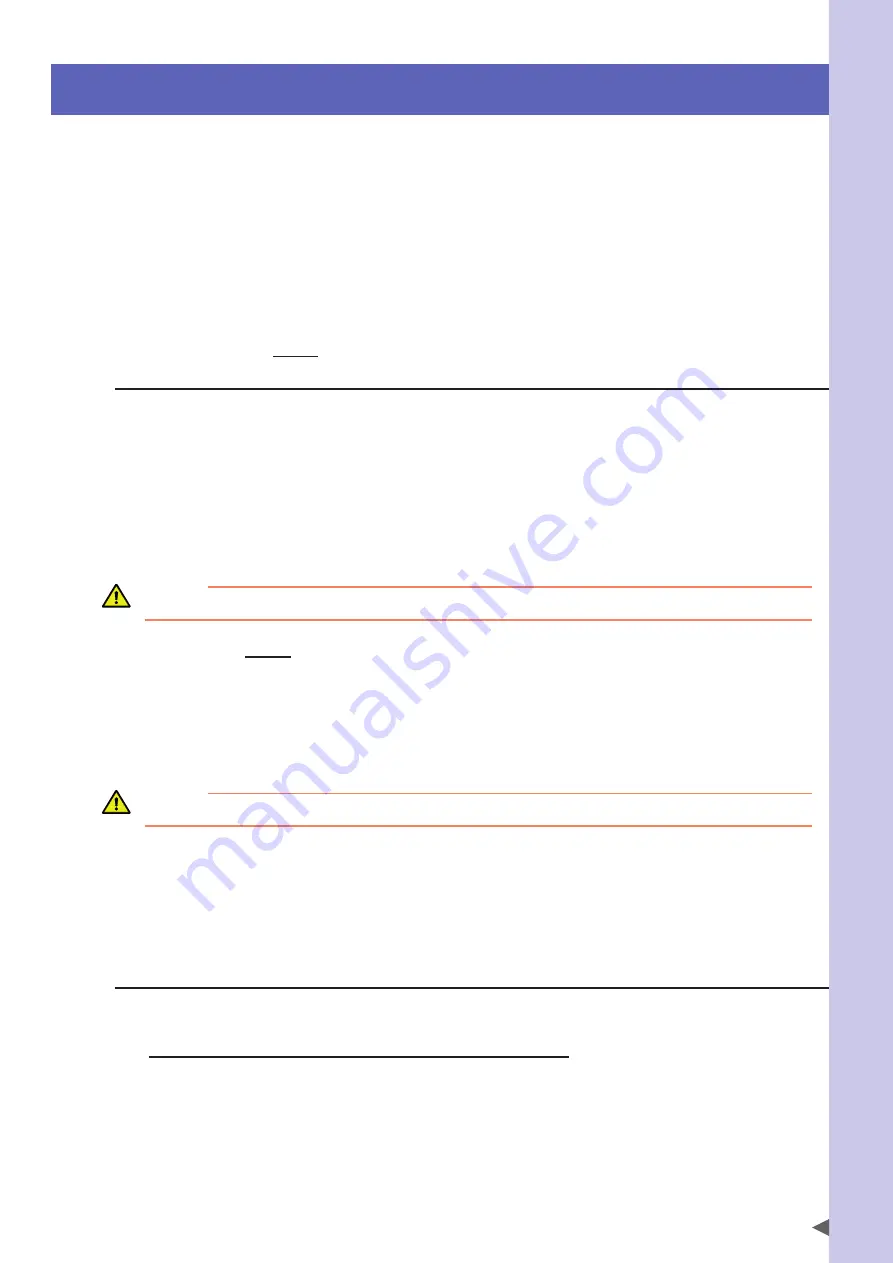
Intr
oduction
i
Before using the robot (Be sure to read the following notes.)
At this time, our thanks for your purchase of this OMRON XG series SCARA robot.
1.
Please be sure to perform the following tasks before using the robot.
Failing to perform the tasks below will require re-teaching of the robot since the origin position cannot be set to the same previous
position. Robot malfunctions (vibration, noise) may also occur.
The origin position of the XG series robots is adjusted to the robot arm extended position at the factory prior to shipment, so the
reference or standard coordinates are temporarily set. The customer should set the origin position before any other job. There are
2 types of origin position settings as shown below.
[1]Setting the robot arm extended position (the origin position adjusted at the factory prior to shipment) as the origin
position (When setting the origin position with the robot arm extended, you must check that there will not be any
interference from any peripheral equipment during the next absolute reset.)
[2]Setting a position OTHER than the robot arm extended position (the origin position adjusted at the factory prior to
shipment) as the origin position
[1]To set the robot arm extended position (the origin position adjusted at the factory prior to shipment) as the origin position
Absolute Reset
The XG series robots only require the absolute reset to be performed once when the robot is introduced. Once the absolute reset
is performed, you do not need to reperform it when the power is turned on next time. Set the origin position while referring to
absolute reset methods in "2. Adjusting the origin" in Chapter 3 of this manual and in "Absolute Reset" of the "OMRON Robot
Controller User's manual". Setting of standard coordinates is not required in the above case. To set the standard coordinates
with high accuracy, refer to "4. Setting the standard coordinates" in Chapter 3 of this manual and "Setting the Standard
Coordinates" in the "omRon Robot Controller User's manual". If the standard coordinate settings are incorrect, robot
malfunctions (vibration, excessive noise) may occur.
CAUTION
Never enter the robot movement range once the robot servo is turned on as this is extremely hazardous.
[2]To set a position OTHER than the robot arm extended position (the origin position adjusted at the factory prior to
shipment) as the origin position
1.Absolute reset
The XG series robots only require the absolute reset to be performed once when the robot is introduced. Once the absolute
reset is performed, you do not need to reperform it when the power is turned on next time. Set the origin position while
referring to absolute reset methods in "2. Adjusting the origin" in Chapter 3 of this manual and in "Absolute Reset" of the
"omRon Robot Controller User's manual". Set the origin position with the absolute reset.
CAUTION
Never enter the robot movement range once the robot servo is turned on as this is extremely hazardous.
2.Affixing the origin position sticker
Set in emergency stop when absolute reset is complete, and immediately affix the origin point sticker according to instructions in "5.
Affixing stickers for origin positions, movement directions and axis names" in Chapter 3 of this manual.
3.Setting the reference coordinates
Set the reference coordinates while referring to instructions in "4. Setting the reference coordinates" in Chapter 3 of this
manual and also to "Setting the Reference Coordinates" in the "omRon Robot Controller User's manual". Robot
malfunctions (vibration, noise) may occur if the reference coordinates are not set correctly.
Even though there is no problem with the robot, the following error messages are issued when the robot and controller are
connected and power first turned on. (Actual error messages may differ according to how the robot and controller are connected.)
Examples of error messages issued when robot and controller are connected
ABS. battery wire breakage
Backup position data error
Resolver disconnected during power off
Position backup counter overflow
etc.
Содержание R6YXG500
Страница 1: ...ZX T Series Cat No I155E EN 03A R6Y XG series INSTALLATION MANUAL SCARA Robots XG Series...
Страница 2: ......
Страница 10: ......
Страница 36: ......
Страница 38: ......
Страница 39: ...Contents Before using the robot Be sure to read the following notes i Introduction v Introduction...
Страница 40: ......
Страница 46: ......
Страница 48: ......
Страница 56: ......
Страница 169: ...2 Installation 2 111 Installing the extension shaft Extension shaft 1 Upper nut Bolt 2 6 Go out of the safety enclosure...
Страница 174: ......
Страница 176: ......
Страница 220: ......
Страница 221: ...Chapter 4 Periodic inspection Contents 1 Overview 4 1 2 List of inspection items 4 2...
Страница 222: ......
Страница 226: ......
Страница 227: ...Chapter 5 Harmonic drive replacement period Contents 1 Overview 5 1 2 Replacement period 5 2...
Страница 228: ......
Страница 232: ......
Страница 238: ......
Страница 239: ...Chapter 7 Torque limit designated Z axis pushing action Contents 1 Torque limit designated Z axis pushing action 7 1...
Страница 240: ......
Страница 244: ......
Страница 246: ......
Страница 323: ...8 Specifications 8 77 1 3 Robot inner wiring diagram Robot inner wiring diagram R6YXG500...
Страница 330: ...Cat No I155E EN 03A Note Specifications subject to change without notice Authorized Distributor Printed in Europe...